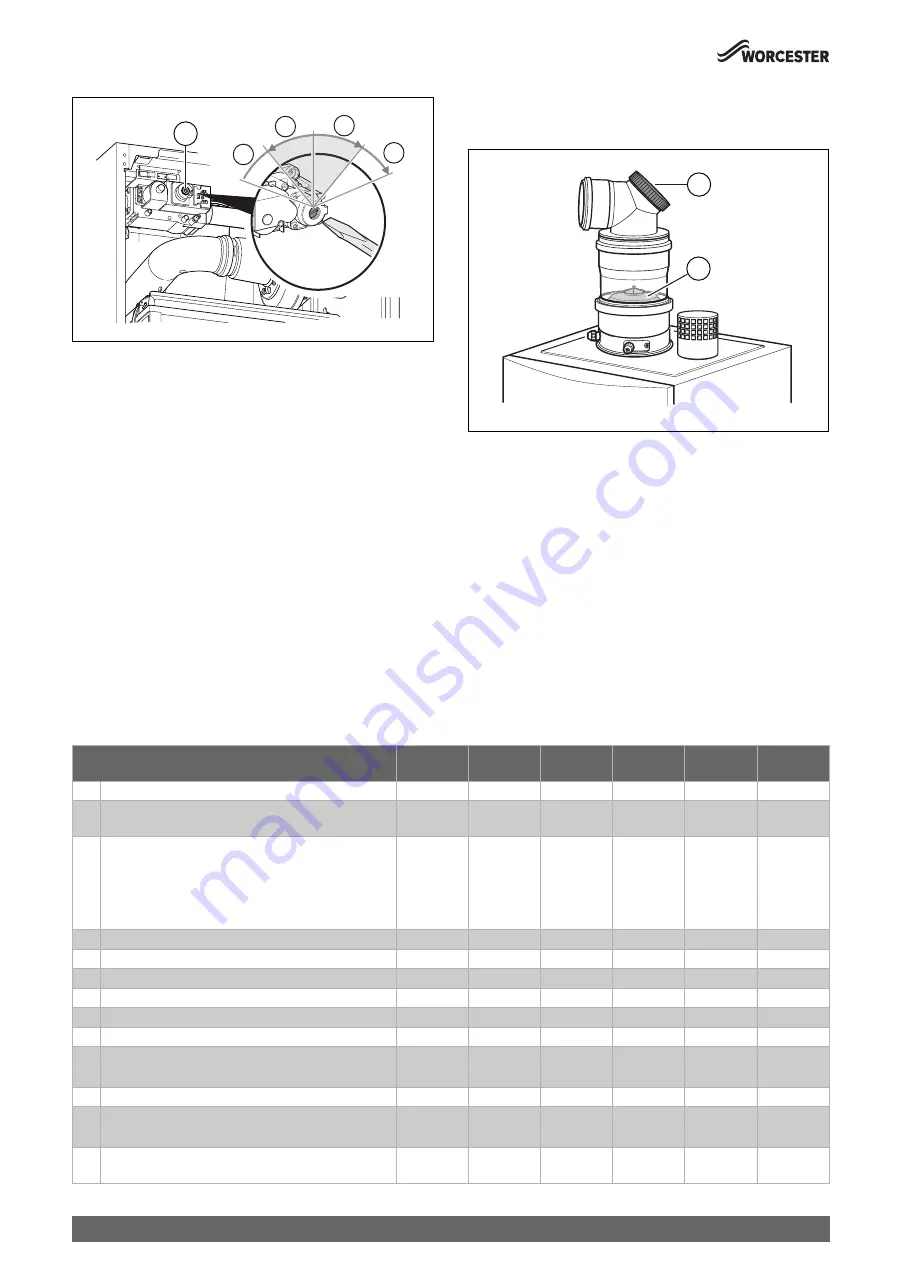
Inspection and servicing
Worcester Commercial Boiler Series – 6720814332 (2019/04)
44
Fig. 94 Setting the gas/air ratio (85-V2 and 100-V2)
[1]
Cap
[2]
Differential pressure incorrect
[3]
Differential pressure correct
▶ Enter the measurement in the maintenance protocol
(
Chapter 11.15 "Inspection and maintenance reports", page 44).
▶ Switch off the chimney sweep mode.
▶ Take the boiler out of operation.
▶ Close the gas isolation valve.
▶ Remove the pressure gauge.
▶ Close the test nipple.
▶ Replace the cap on the adjusting screw.
▶ Open the gas isolation valve.
▶ Bring the boiler into operation.
11.10 Measure CO/CO
2
content
See chapter 8.9 "Measure the CO and CO2 content".
11.11 Check flue gas non-return valve
If the boiler has been installed within an overpressure flue cascade
system, the flue gas non-return valve must be checked.
▶ Open the inspection aperture [1] of the flue gas turret.
▶ Check the flue gas non-return valve [2] for wear, damage or soiling
and replace if necessary.
▶ Close the inspection aperture of the flue gas non-return valve.
Fig. 95 Checking the flue gas non-return valve
[1]
Inspection aperture
[2]
Flue gas non-return valve
11.12 Measure ionisation current
See chapter 8.10 "Measure ionisation current".
11.13 Testing for gas leaks
See chapter 8.11 "Testing for gas leaks".
11.14 Check for correct operating characteristics
▶ Check all fittings for leaks.
▶ Check the system pressure of the boiler and top up if necessary.
In doing so, take the water quality into account (
Chapter 3.2).
▶ Check the boiler settings (
▶ Replace the front casing and tighten the retaining screws.
11.15 Inspection and maintenance reports
0010010060-001
-5 Pa
-10 Pa
0 Pa
1
2
3
3
2
0010010061-001
1
2
Inspection work
Date:
___________
Date:
___________
Date:
___________
Date:
___________
Date:
___________
Date:
___________
1.
Check the general condition of the heating system.
2.
Carry out a visual inspection and function check of the
heating system.
3.
Check the system components in contact with gas and
water for the following:
• tightness during operation
• visible signs of corrosion
• signs of ageing
4.
Check the burner, ignition and monitoring electrodes.
5.
Measure the gas supply pressure.
_______ mbar _______ mbar _______ mbar _______ mbar _______ mbar _______ mbar
6.
Measure gas/air ratio.
_______ Pa
_______ Pa
_______ Pa
_______ Pa
_______ Pa
_______ Pa
7.
Carry out a tightness test during operation.
8.
Measure the CO content (flue gas analysis).
_______ ppm _______ ppm _______ ppm _______ ppm _______ ppm _______ ppm
9.
Measure the ionisation current.
_______ μA
_______ μA
_______ μA
_______ μA
_______ μA
_______ μA
10.
Check the charge pressure:
- Check the charge pressure of the heating system.
_______ bar
_______ bar
_______ bar
_______ bar
_______ bar
_______ bar
11.
Check the combustion air supply and flue gas routing.
12.
Check that the control is set correctly.
▶ Consult the instruction manual of the controller.
13.
Final inspection check, take measurements and
document measurement and test results.