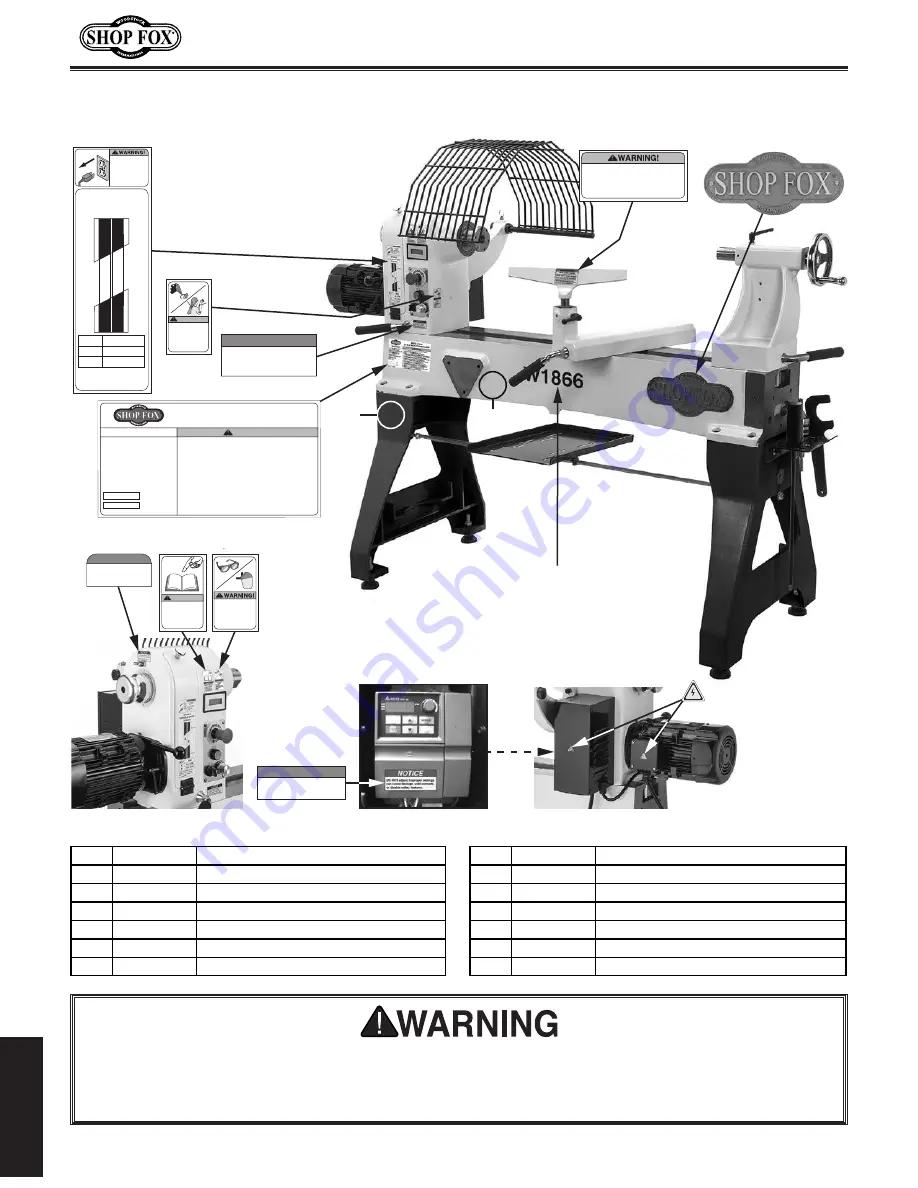
-54-
Model W1866 (For Machines Mfd. Since 11/18)
PA
RT
S
Labels.&.Cosmetics
Safety.labels.warn.about.machine.hazards.and.how.to.prevent.serious.personal.injury..The.owner.
of.this.machine.MUST.maintain.the.original.location.and.readability.of.all.labels.on.this.machine..
If.any.label.is.removed.or.becomes.unreadable,.REPLACE.that.label.before.allowing.machine.to.
be.operated.again..Contact.us.at.
(
360
)
.734-3482.or.www.woodstockint.com.to.order.new.labels..
W1866
IMPACT INJURY HAZARD!
Improperly supported or positioned cutting tools can “catch”
on workpiece, ejecting tool from your hands with great force.
To reduce this risk, always ensure tool rest is properly
positioned for each type of operation, cutting tool is firmly
supported against tool rest BEFORE cutting, and cutting tool
is properly positioned for tool and operation type.
Specifications
MODEL W1866
24" X 36" BOWL-TURNING LATHE
To reduce risk of serious personal injury while using this machine:
1. Read and understand manual before starting.
2. Always wear safety glasses, face shield, and respirator.
3. Avoid getting entangled in rotating workpiece—tie back long hair, roll
up long sleeves, and DO NOT wear loose clothing, gloves, or jewelry.
4. Properly set up lathe and tighten all locks before operating.
5. Rotate workpiece by hand to ensure clearance before applying power.
6. DO NOT turn split workpieces or those containing knots.
7. Rough out workpiece to remove excess material before mounting.
8. Use the lowest speed when starting a new workpiece.
9. Always support cutting tool on properly adjusted tool rest.
10. Disconnect power before setting up, adjusting, or servicing lathe.
11. DO NOT operate when tired or under influence of drugs/alcohol.
12. DO NOT expose to rain or operate in a wet environment.
13. Prevent unauthorized use by children or untrained users; restrict
access or disable machine when unattended.
WARNING!
Power Supply: 220V, 1-Ph, 60 Hz, 20A
Motor: 3 HP, 220V, 3-Ph, 8.5A
Full-Load Current Rating (w/VFD): 15.8A
Spindle Speeds: 60–2300 RPM
Distance Between Centers: 36-3/4"
Swing Over Bed: 24"
Swing Over Tool Rest Base: 19"
Spindle Taper: MT#2
Tailstock Taper: MT#2
Weight: 723 lbs.
Mfd. for Woodstock in China
Date
S/N
Pin must be pulled out before
operating machine. Failure to
do so can damage motor or
machine components.
NOTICE
Always wear
ANSI-approved safety
glasses and face shield
when using this
machine.
EYE/FACE INJURY
HAZARD!
READ and UNDERSTAND
MANUAL to avoid serious
injury! If a manual is not
available, DO NOT use
machine! Instead, go to
www.woodstockint.com
or call (360) 734-3482.
WARNING!
NOTICE
To restart lathe after engaging
Emergency Stop, turn spindle
direction switch to middle position
and reset Emergency Stop button.
NOTICE
DO NOT adjust. Improper settings
can cause damage, void warranty,
or disable safety features.
SPINDLE
VARIABLE-SPEED
RANGES
BELT
RPM
A
B
60–1200
120–2300
A
B
NOTE: To maximize spindle
torque, use Belt Position A
when turning at speeds less
than 1200 RPM.
Spindle
Motor
INJURY/SHOCK
HAZARD!
Disconnect power
before adjustments,
maintenance, or
service.
ENTANGLEMENT
HAZARD!
Tie back long hair, roll up
long sleeves, and remove
loose clothing, jewelry, or
gloves to prevent getting
caught in moving parts.
WARNING!
201
202
203
204
205
206
207
208
209
210
211
212
214
213
REF PART #
DESCRIPTION
REF PART #
DESCRIPTION
201
X1866201
DISCONNECT/SPINDLE RANGE LABEL
208
X1866208
ELECTRICITY LABEL
202
X1866202
MACHINE ID LABEL
209
X1866209
DO NOT ADJUST VFD NOTICE
203
X1866203
ENTANGLEMENT LABEL
210
X1866210
EYE/FACE INJURY LABEL
204
X1866204
RESTART LATHE NOTICE
211
X1866211
READ MANUAL LABEL
205
X1866205
IMPACT WARNING LABEL
212
X1866212
SPINDLE PIN NOTICE
206
X1866206
SHOP FOX NAMEPLATE
213
X1866213
TOUCH-UP PAINT, SHOP FOX BLACK
207
X1866207
MODEL NUMBER LABEL
214
X1866214
TOUCH-UP PAINT, SHOP FOX WHITE
Содержание W1866
Страница 57: ...Model W1866 For Machines Mfd Since 11 18...
Страница 60: ......