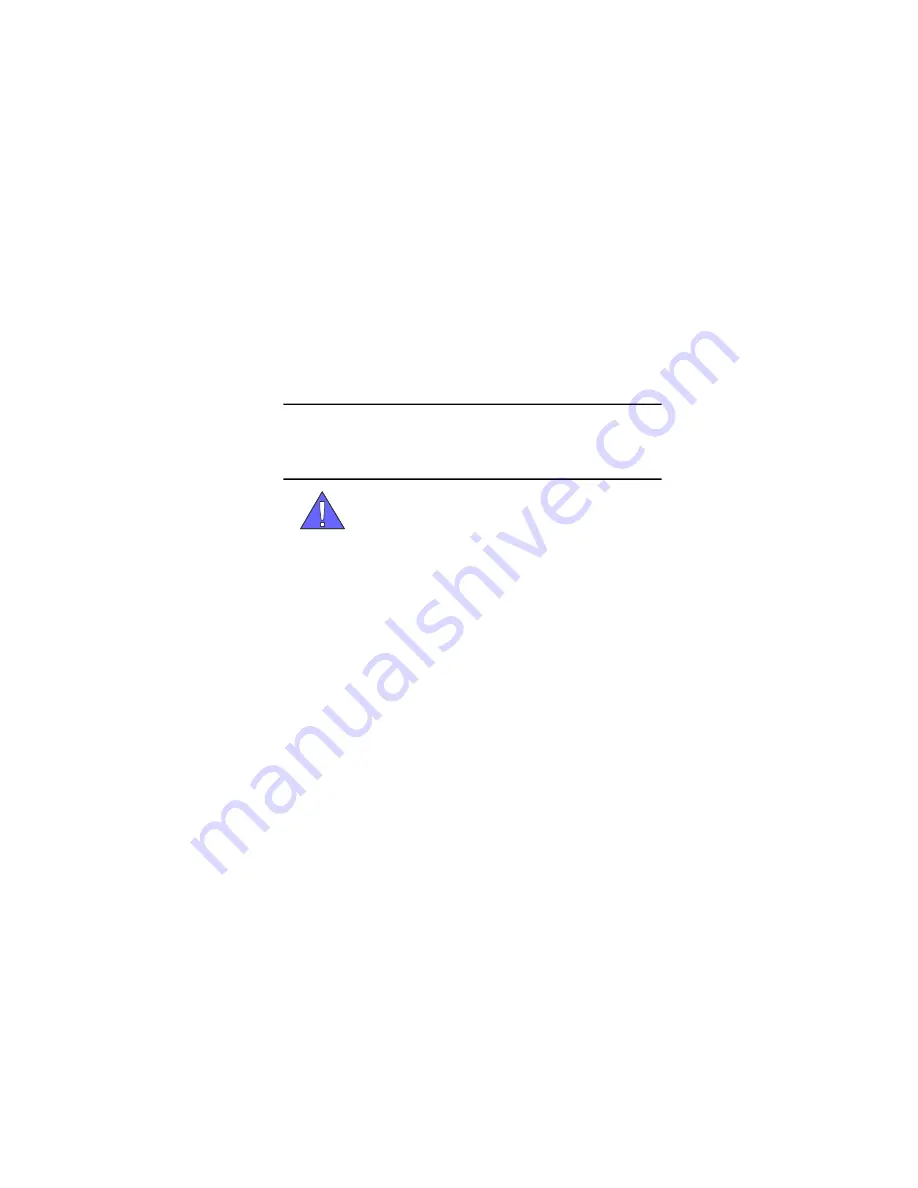
LX250
Wood-Mizer
®
Sawmill
Safety, Setup, Operation
& Maintenance Manual
LX250
rev. A2.01
Safety is our #1 concern!
Read and understand
all safety information and instructions before oper
-
ating, setting up or maintaining this machine.
Form #2370