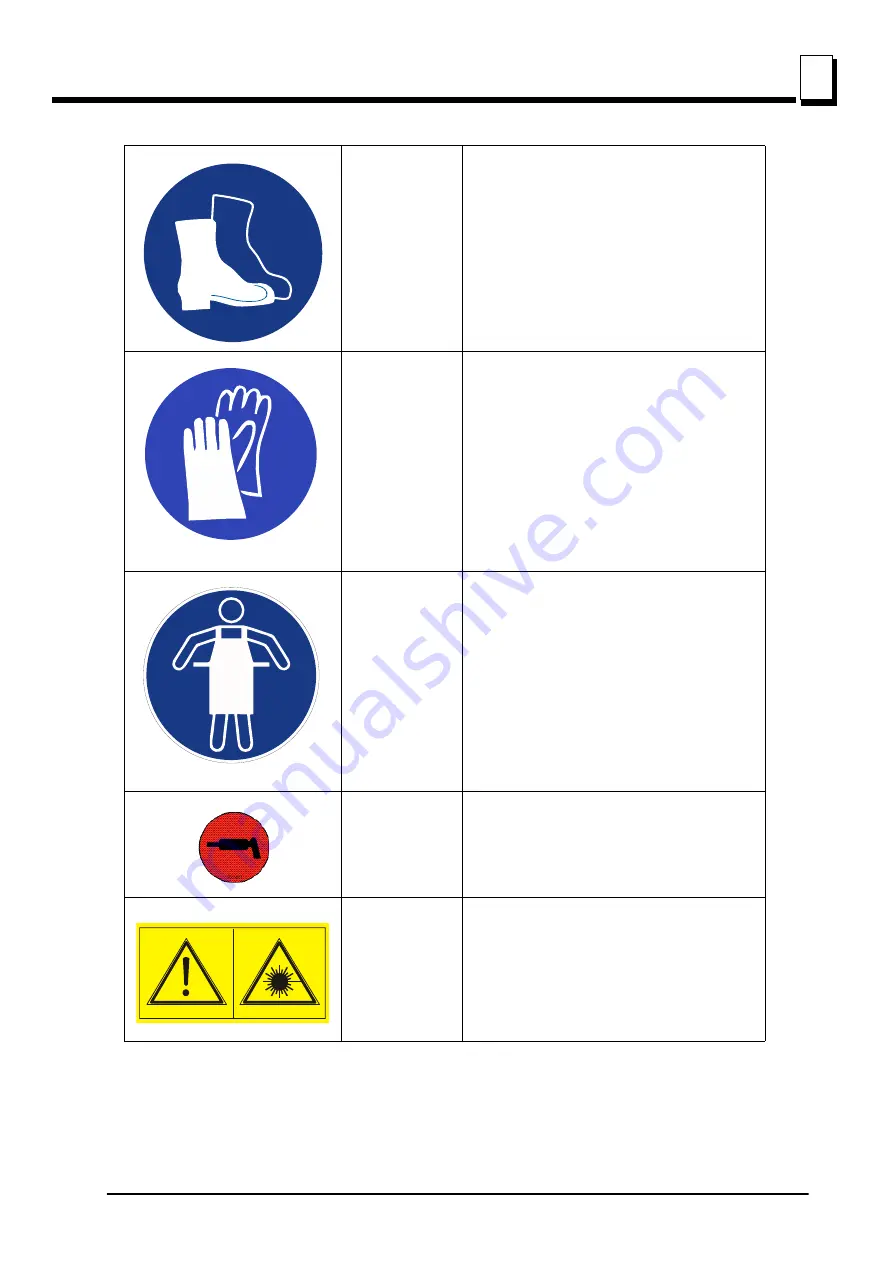
SAFETY
Safety Labels Description
Safety
EGdoc031621
2-9
2
501465
Always wear safety boots when operating
this machine.
510080
Always wear protective gloves when
operating the edger!
539211
Always wear protective apron when
operating the edger!
501467
Lubrication point
099504
Visible and/or invisible laser radiation.
Avoid eye or skin exposure to direct or
scattered radiation.
TABLE 2-1
099504
Содержание EG350EH15S
Страница 1: ......
Страница 2: ......
Страница 62: ...Laser Information 7 7 1 MHdoc031621 Specifications SECTION 7 LASER INFORMATION ...
Страница 64: ...Laser Information 7 7 3 MHdoc031621 Specifications ...