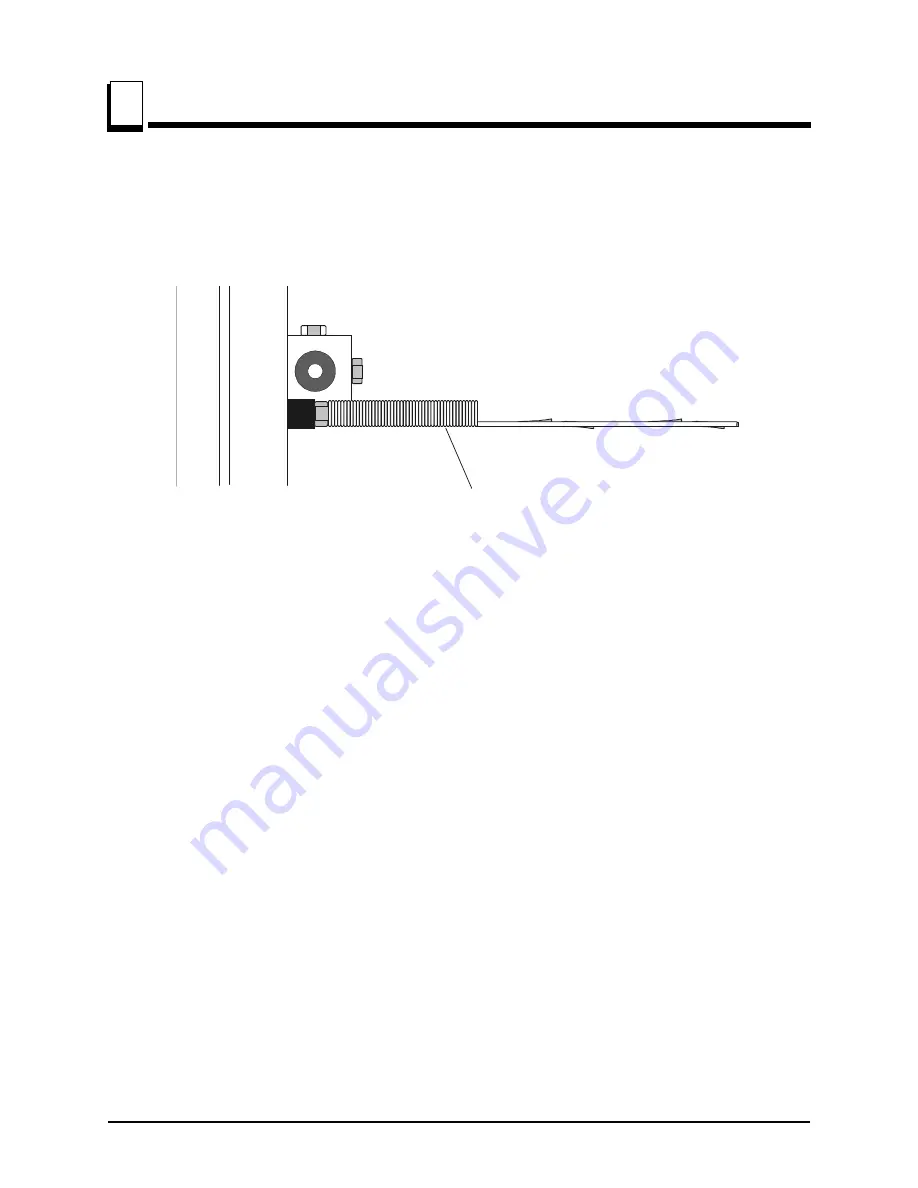
Setup & Operation
Blade Height Sight Gauge
2
2-26
HD92doc042701
Setup & Operation
2.17 Blade Height Sight Gauge
See Figure 2-16. The sight gauge is provided on the cutting head carriage to help you
decide where to make the first cuts on a log.
Move the carriage forward until the blade is close to the end of the log.
Position yourself so that your eyes are level with the bottom of the sight gauge spring.
With one eye closed, move your head up or down until the bottom of the sight gauge is
lined up with the bottom of the blade.
Sight down the length of the log. You should be able to see where the blade will pass
through the log down its entire length. Raise or lower the cutting head until you get the
blade height you want.
HINT: After judging by eye where you want to make your first slab cut, check the scale.
Move the up/down crank to fine-tune the blade height to an even measurement on the
blade height scale.
Example: Adjust the blade up to 15" rather than cut at 14 13/16". This will make adjust-
ments for the next cuts easier to figure on the scale.
FIG. 2-16
Sight gauge eye-level
with bottom of blade
SM0047