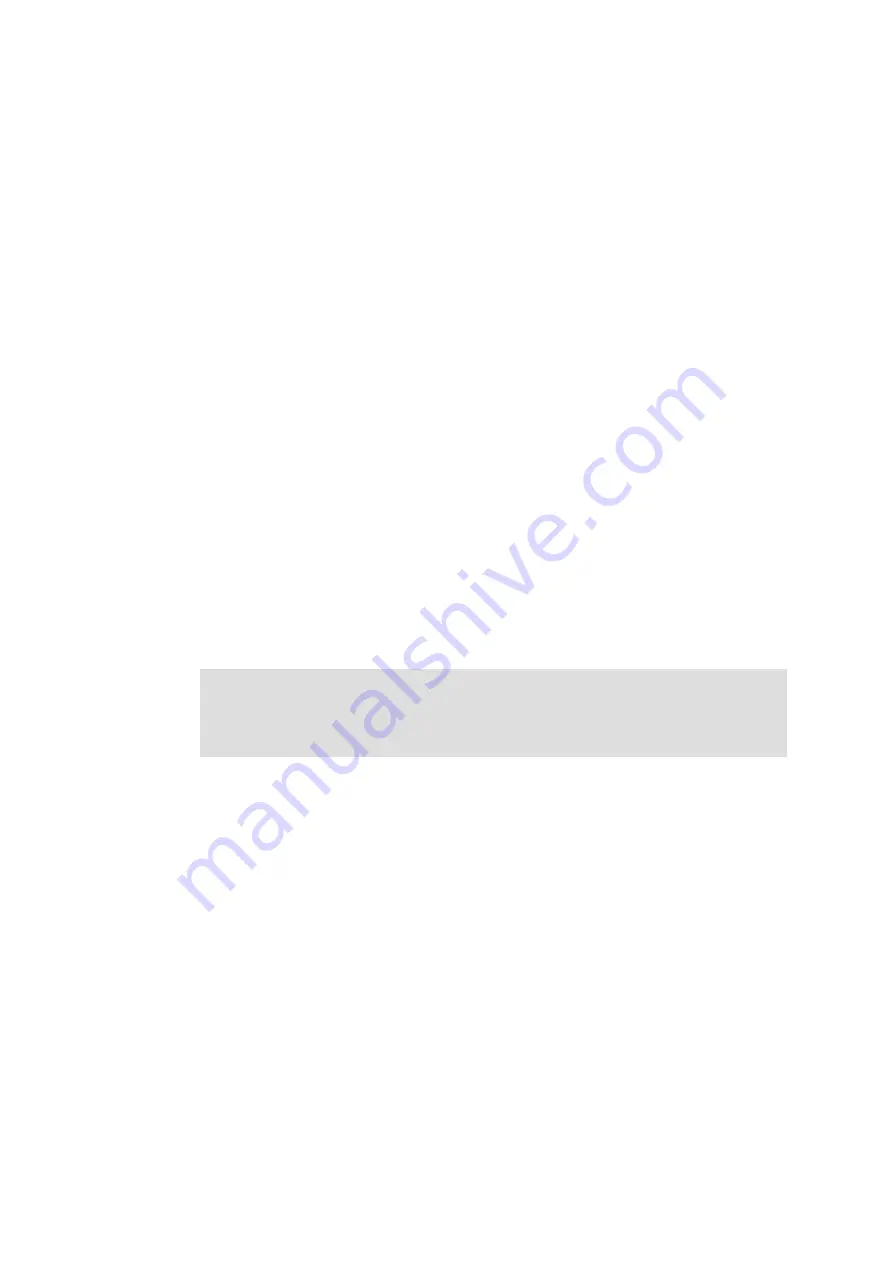
Technical data
j
| BA 14.0197 | 11/2010
14
3.1.3
Brake release
In braked state, there is an air gap "s
Lü
" between the stator (1.1) and the armature plate
segments (2). To release the brake, the coils (8) of the two magnetic circuits are excited with
the DC voltage provided. The magnetic force generated attracts the armature plate segments
(2) towards the stator (1.1) against the spring forces. The rotor (3) is then released and can
rotate freely.
3.1.4
Release monitoring
The spring−applied brake BFK464 is equipped with one microswitch (16) each per braking
circuit for monitoring the switching status. When the braking circuits are released, the
microswitches (16) change over. This means that the operation of the drive against the
applied brake can be excluded. The microswitches can be connected both as NO and NC
contacts.
For checking the correct functioning of the microswitches, we recommend to check the
switching status (see Tab. 5) both when the brake is released and when the brake is
applied.
3.1.5
Manual release (optional)
Instead of the transport safety bolts usually used, a manual release is optionally available
for short−term release when no voltage is applied. The manual release is used for both
braking circuits.
Note!
| The manual release is designed for operation using a Bowden cable.
| The braking circuits can only be released electrically.
Tip!
The manual release can be retrofitted,
3.1.6
Encapsulated design (optional)
This design not only avoids the penetration of spray water and dust, but also the spreading
of abrasion particles outside the brake. This is achieved by:
|
a cover seal over the armature plate and rotor,
|
a cover in the adjuster nut,
|
a shaft seal in the adjuster nut for continuous shafts (option).