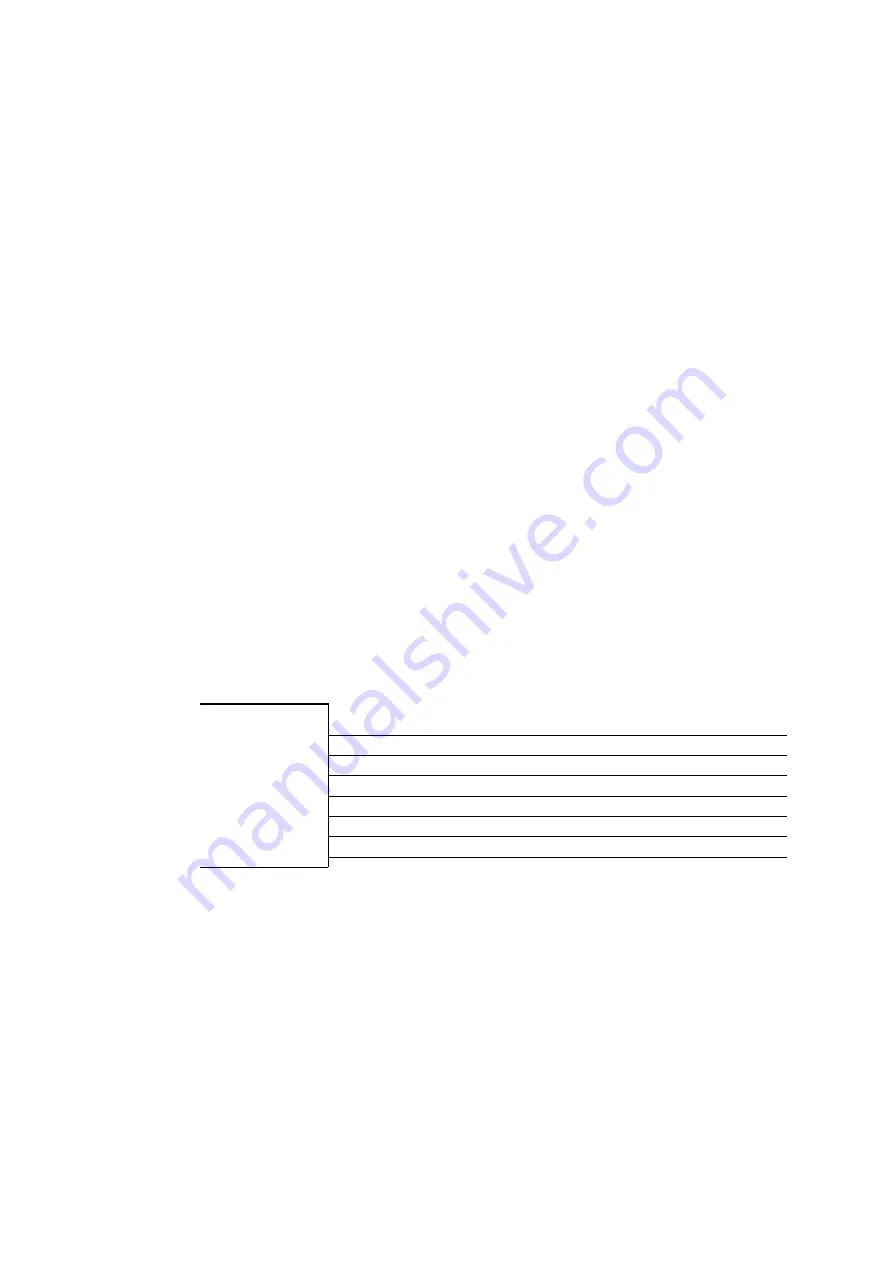
Technical data
i
j
| BA 14.0197 | 11/2010
13
3.1.1
General information
The spring−applied brake is designed for the conversion of mechanical work and kinetic energy
into heat. For operating speed, see
15 Rated data. Due to the static brake torque, the brake
can hold loads without speed difference. Emergency braking is possible at high speed,
Rated data. The more friction work, the higher the wear.
The spring−applied brake BFK464 is a single−disk brake with two friction surfaces. The brake
torque is generated in two electrically and mechanically separated braking circuits by several
compression springs (1.2) by friction. The braking circuits are released electromagnetically.
With its two braking circuits, the brake is particularly suitable for lift and stage technology. The
brake is selected according to the rated torque for one braking circuit. The second braking
circuit fulfills the demand for redundancy.
By dividing the armature plate (2) with the corresponding compression springs (1.2) and
electromagnetic coils (8) into two parts, the braking circuits are divided. Through the separate
connection cables for each coil group and the armature plate segment, each braking circuit
can be switched individually (
32). Each braking circuit is equipped with a microswitch (16)
that monitors the switching status of the spring−applied brake. The supply voltage (AC voltage)
is rectified by the corresponding switchgears and after brake release reduced after a short
time. In this way, the mean electrical brake power is reduced.
The stator (1) is designed in thermal class F. The limit temperature of the coils (8) is 155°C.
The spring−applied brake BFK464 is designed for a maximum operating time of 60 % with
holding current reduction.
Certificate
Type
EC type−examination certificate
INTORQ BFK464−18
S
ABV (in preparation)
INTORQ BFK464−19
S
ABV (in preparation)
INTORQ BFK464−20
S
ABV 849
INTORQ BFK464−20
S.1
ABV 850
INTORQ BFK464−25
S
ABV 851
INTORQ BFK464−28
S
ABV (in preparation)
3.1.2
Braking
During braking, the rotor (3), which is axially movable on the hub (4), is pressed against
the friction surface − via the armature plates (2) − by means of the springs (1.2). The
asbestos−free friction linings ensure a high braking torque with low wear. The braking
torque is transmitted between hub (4) and rotor (3) via the splines.