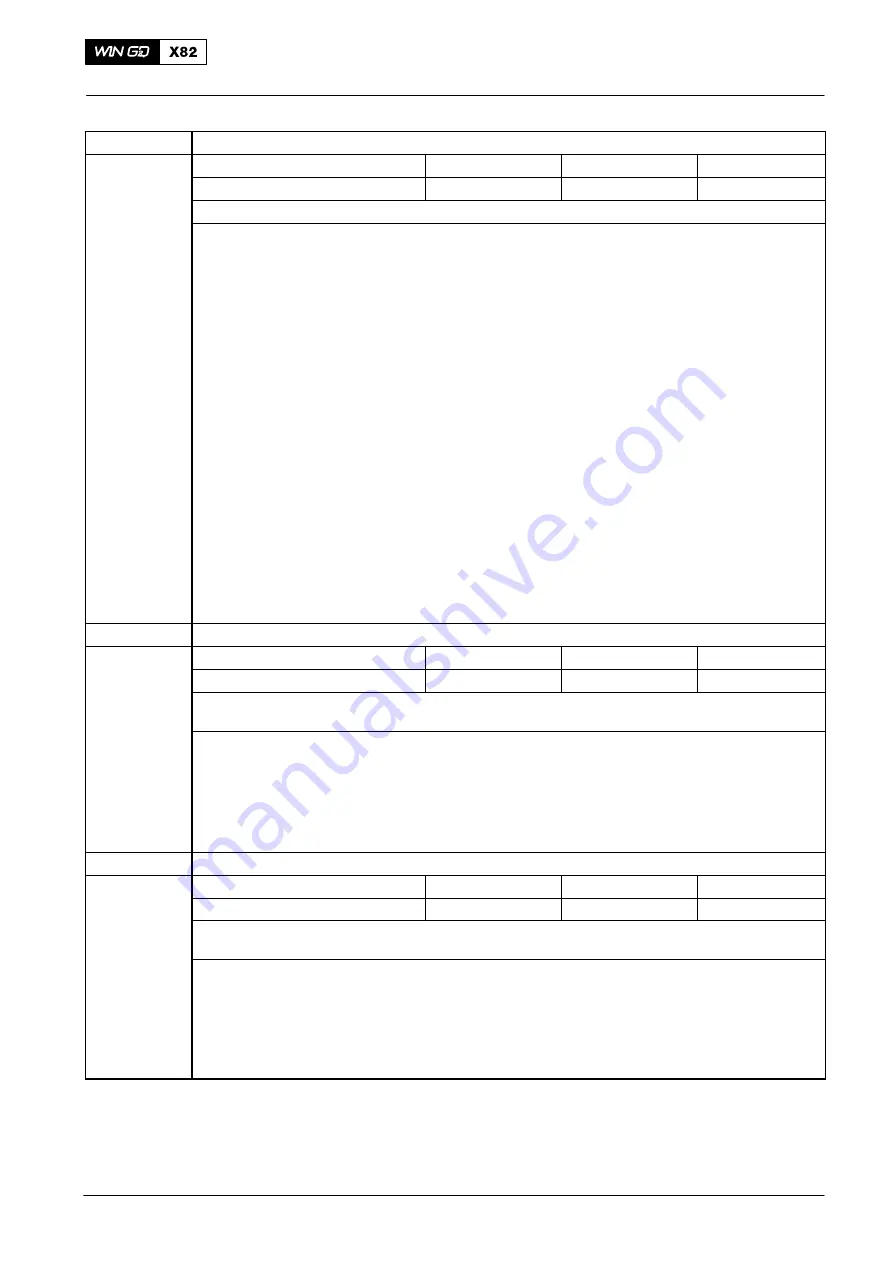
Operation
0850
−
1/A1
Winterthur Gas & Diesel Ltd.
Failure Text
WECS cylinder lubrication passive failure. (ID 2.5)
FCM
−
20 No.
LED
Failure ID
Display
Indication
#03 and #04
None
125
2.5
Cause Disconnected power supply #1 or #2.
Procedure
⇒
In E85, E90 and E41.xx, make sure that the cables have no damage and are connected
correctly.
⇒
In E85, make sure that the all circuit breakers are set to on.
⇒
Repair the cables and connections in E85, E90 (terminals 40/41) and E41.xx (plug X2,
terminals 21/22).
⇒
In the FCM
−
20 (plug X22, terminals 55/56) of the last and last but one cylinders, make sure
that the cables and connections have no damage and are connected correctly.
⇒
Do a check of the related ALM-20 CAN
−
M bus indications (LED CAN 1 or CAN 2).
⇒
If the bus indications show a failure, repair the cables of the last and last but one FCM
−
20 (plug
X22, terminals 55/56).
⇒
Repair the cables in the related CAN
−
M bus. Make sure that the related ALM
−
20 operates.
⇒
If after all ALM
−
20 are started and the related ALM
−
20 did not start, make sure that the cable
address on the plug X1 of the related ALM-20 is connected correctly.
⇒
Do a check of the ALM-20 (plug X1, terminals 16/17) and the related resistors (see
Resistor in plug X1, paragraph 5.2).
⇒
Repair the cables and connections in the related ALM
−
20.
⇒
If necessary, replace the defective ALM-20.
Failure Text
ME waste heat recovery valve #1 not closed (ID 3.2.)
FCM
−
20 No.
LED
Failure ID
Display
Indication
#01
None
232
3.2.
Cause Waste heat recovery valve #1 (main valve) is not closed. A command to close the main valve
was sent to the valve, but the sensor responses that the valve is in the open position.
Procedure
⇒
Do a check of the position switch ZS5372C.
⇒
Make sure that the cables between the FCM-20 #01 and position switch ZS5372C have no
damage and are connected correctly.
⇒
If necessary, repair or replace the damaged cables.
⇒
If necessary, replace the position switch ZS5372C.
Failure Text
ME waste heat recovery valve #1 not open (ID 3.3.)
FCM
−
20 No.
LED
Failure ID
Display
Indication
#05
None
233
3.3.
Cause Waste heat recovery valve #1 (main valve) is not open. A command to open the main valve
was sent to the valve, but the sensor responses that the valve is in the close position.
Procedure
⇒
Do a check of the position valve ZV7076C.
⇒
Make sure that the cables between the FCM-20 #05 and position valve ZV7076C have no
damage and are connected correctly.
⇒
If necessary, repair or replace the damaged cables.
⇒
If necessary, replace the position valve ZV7076C.
2014
Failures and Defects of WECS Components
Содержание W-X82
Страница 10: ...Intentionally blank...
Страница 14: ...Intentionally blank...
Страница 18: ...Intentionally blank...
Страница 28: ...Intentionally blank...
Страница 34: ...Intentionally blank...
Страница 38: ...Intentionally blank...
Страница 44: ...Intentionally blank...
Страница 52: ...Intentionally blank...
Страница 58: ...Intentionally blank...
Страница 60: ...Intentionally blank...
Страница 62: ...Intentionally blank...
Страница 68: ...Intentionally blank...
Страница 70: ...Intentionally blank...
Страница 76: ...Intentionally blank...
Страница 78: ...Intentionally blank...
Страница 86: ...Intentionally blank...
Страница 92: ...Intentionally blank...
Страница 94: ...Intentionally blank...
Страница 96: ...Intentionally blank...
Страница 100: ...Intentionally blank...
Страница 104: ...Intentionally blank...
Страница 108: ...Intentionally blank...
Страница 112: ...Intentionally blank...
Страница 114: ...Intentionally blank...
Страница 116: ...Intentionally blank...
Страница 138: ...Intentionally blank...
Страница 140: ...Intentionally blank...
Страница 142: ...Intentionally blank...
Страница 144: ...Intentionally blank...
Страница 146: ...Intentionally blank...
Страница 150: ...Intentionally blank...
Страница 154: ...Intentionally blank...
Страница 172: ...Intentionally blank...
Страница 174: ...Intentionally blank...
Страница 208: ...Intentionally blank...
Страница 210: ...Intentionally blank...
Страница 250: ...Intentionally blank...
Страница 252: ...Intentionally blank...
Страница 254: ...Intentionally blank...
Страница 258: ...Intentionally blank...
Страница 262: ...Intentionally blank...
Страница 272: ...Intentionally blank...
Страница 282: ...Intentionally blank...
Страница 286: ...Intentionally blank...
Страница 294: ...Intentionally blank...
Страница 310: ...Intentionally blank...
Страница 332: ...Intentionally blank...
Страница 334: ...Intentionally blank...
Страница 337: ...Operation 4003 3 A1 Winterthur Gas Diesel Ltd 3 21 WCH00345 2014 Air Supply...
Страница 338: ...Operation 4003 3 A1 Winterthur Gas Diesel Ltd 4 21 018 071 09 2014 Bearing and Cooling Oil Supply...
Страница 339: ...Operation 4003 3 A1 Winterthur Gas Diesel Ltd 5 21 WCH01167 2014 Servo Oil Supply 6 cylinders to 8 cylinders...
Страница 340: ...Operation 4003 3 A1 Winterthur Gas Diesel Ltd 6 21 WCH01167 2014 Servo Oil Supply 9 cylinders...
Страница 341: ...Operation 4003 3 A1 Winterthur Gas Diesel Ltd 7 21 WCH01167 2014 Fuel Supply 6 cylinders to 8 cylinders...
Страница 342: ...Operation 4003 3 A1 Winterthur Gas Diesel Ltd 8 21 WCH01123 2014 Fuel Supply 9 cylinders...
Страница 343: ...Operation 4003 3 A1 Winterthur Gas Diesel Ltd 9 21 016 805 08 2014 Starting System...
Страница 344: ...Operation 4003 3 A1 Winterthur Gas Diesel Ltd 10 21 016 335 07 2014 Speed Control...
Страница 346: ...Operation 4003 3 A1 Winterthur Gas Diesel Ltd 12 21 WCH03265 2015 07 Cylinder Lubrication Pulse Jet 9 cylinders...
Страница 351: ...Operation 4003 3 A1 Winterthur Gas Diesel Ltd 17 21 WCH03265 2015 07 Exhaust Valve Drive Air Spring 9 cylinders 3 pumps...
Страница 352: ...Operation 4003 3 A1 Winterthur Gas Diesel Ltd 18 21 WCH03265 2015 07 Fuel Injection 6 cylinders to 8 cylinders...
Страница 353: ...Operation 4003 3 A1 Winterthur Gas Diesel Ltd 19 21 WCH03265 2015 07 Fuel Injection 9 cylinders...
Страница 354: ...Operation 4003 3 A1 Winterthur Gas Diesel Ltd 20 21 018 138 09 2014 Cooling Water...
Страница 355: ...Operation 4003 3 A1 Winterthur Gas Diesel Ltd 21 21 WCH03265 2015 07 Main Bearing Lubrication Piston Cooling OMD...
Страница 356: ...Intentionally blank...
Страница 360: ...Intentionally blank...
Страница 366: ...Intentionally blank...
Страница 372: ...Intentionally blank...
Страница 376: ...Intentionally blank...
Страница 380: ...Intentionally blank...
Страница 386: ...Intentionally blank...
Страница 390: ...Intentionally blank...
Страница 400: ...Intentionally blank...
Страница 404: ...Intentionally blank...
Страница 408: ...Intentionally blank...
Страница 416: ...Intentionally blank...
Страница 422: ...Intentionally blank...
Страница 442: ...Intentionally blank...
Страница 450: ...Intentionally blank...
Страница 452: ...Intentionally blank...
Страница 478: ...Intentionally blank...
Страница 484: ...Intentionally blank...
Страница 510: ...Intentionally blank...
Страница 516: ...Intentionally blank...
Страница 520: ...Intentionally blank...
Страница 522: ...Intentionally blank...
Страница 526: ...Intentionally blank...
Страница 542: ...Intentionally blank...
Страница 546: ...Intentionally blank...