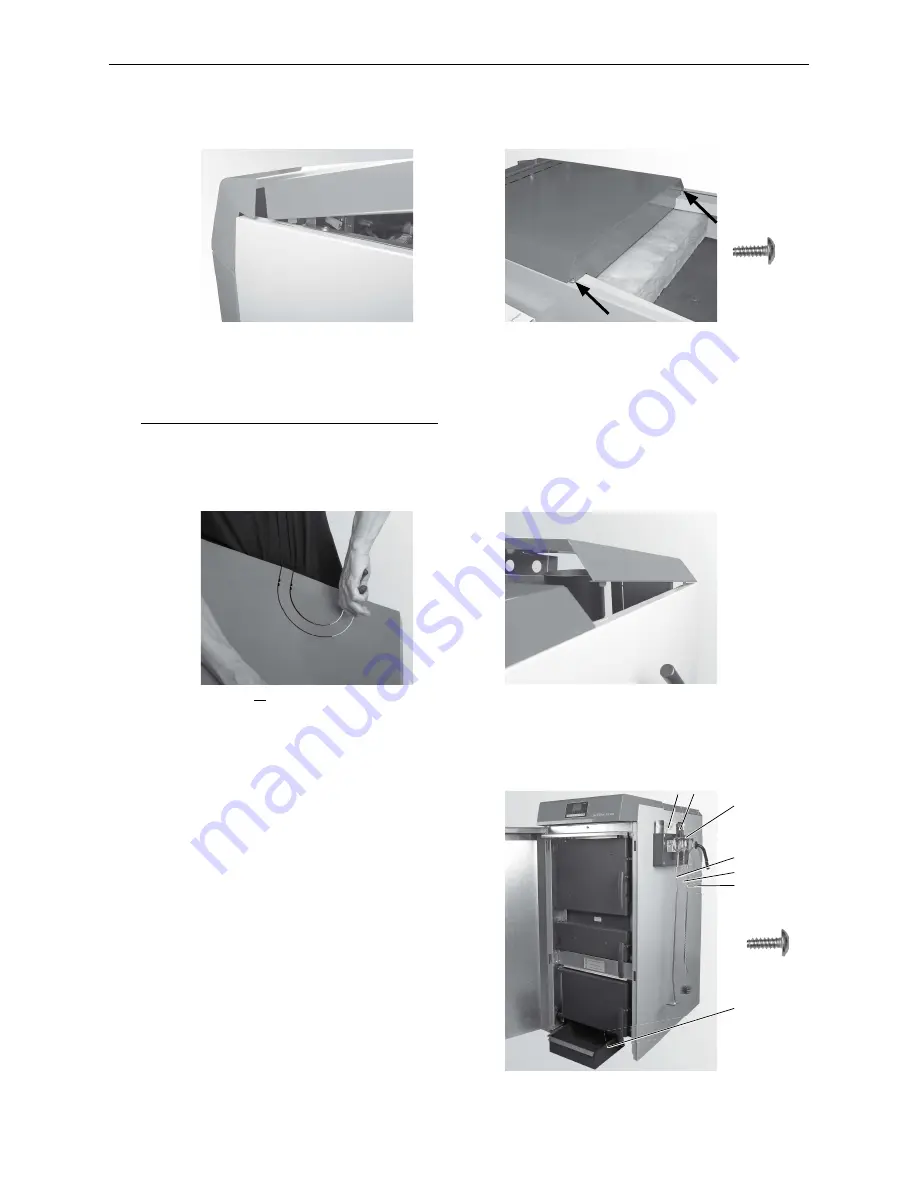
30
2.
For the Installer
2.3.24 Mounting the front boiler cover
– Hook the front boiler cover into the side panels (Fig. 63) and attach at rear with 2 self-tapping screws – Fig. 64.
Fig. 63 Hinging in boiler cover
Fig. 64 Securing boiler cover in 2 places
2 x
2.3.25 Mounting the rear boiler cover
– If no adapter for the flue gas blower (accessories) is being used, break off the cut-out at the rear of the boiler
cover – Fig. 65.
large cut-out = exhaust pipe insulated
small cut-out = exhaust pipe not insulated
do not break off = adapter for flue connection installed
– Hook the rear boiler cover into the slot provided on the side panel cladding – Fig. 66.
Fig. 65 If no adapter for the flue connection is being
used, break off the cut-out
Fig. 66 Hooking in the rear boiler cover
Supplied as standard:
1 ........... Instructions
4 ........... Scratcher
7 ........... Ash pan
Optional accessory: cleaning kit EWK 020:
3 ........... Hanger (for installation on the wall or boiler side panel)
2 ........... Spatula
5 ........... Cleaning brush
6 ........... Poker
2.3.26 Instructions, cleaning and operating implements
– Install the hanger with the instructions folder, cleaning
and operating implements on a side panel of the boiler
(Fig. 67) or on a wall in the boiler room/installation room.
– Keep ash pan under boiler.
4 x
Fig. 67 Fitting hanger, ash pan under
boiler
3
4
5
6
7
1 2