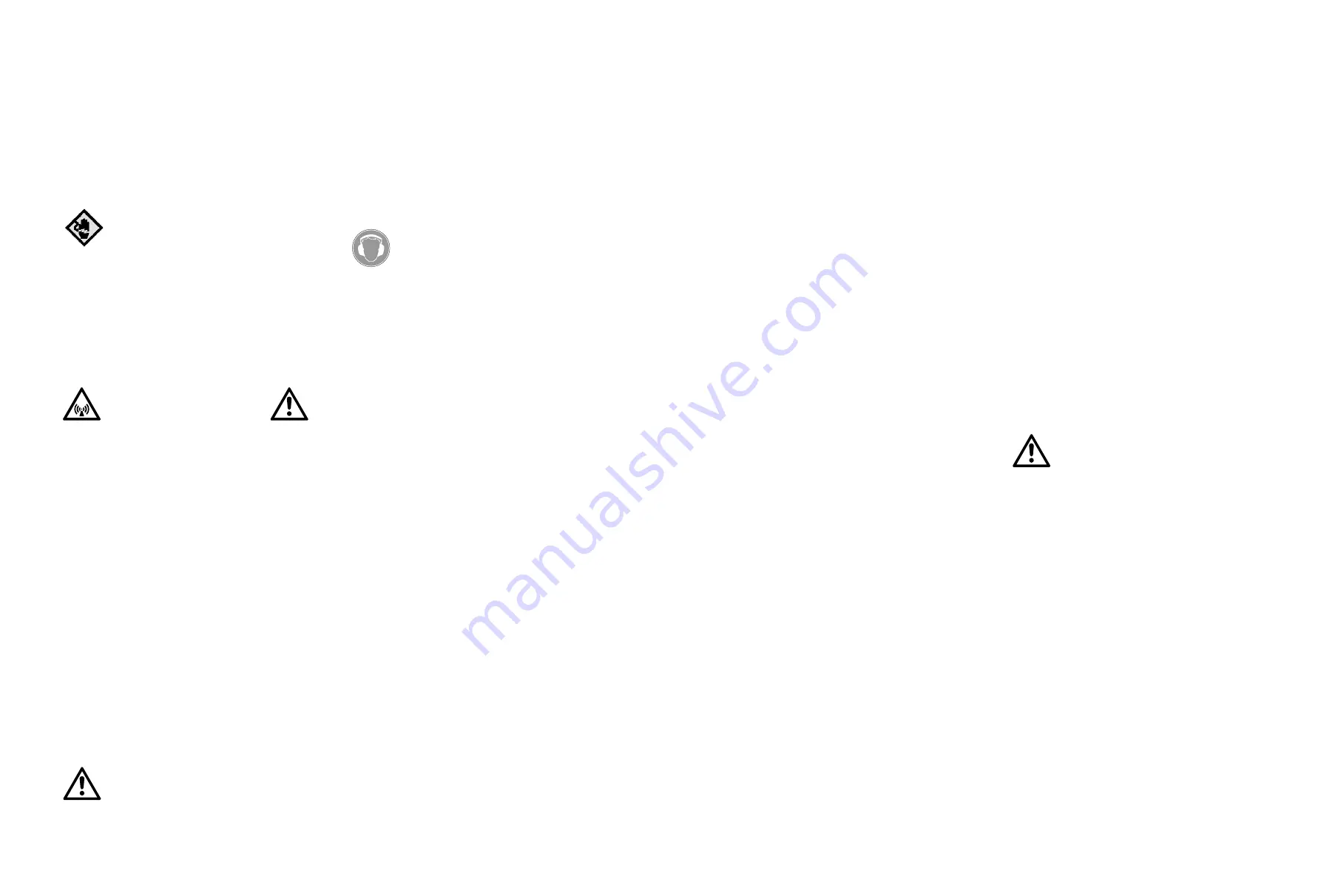
20
21
English
English
2.9 Electrical work & Electrical connection
Our electrical products are operated with alternating or industrial
high-voltage current.
The “Electrical connection” data sheet must be observed when
connecting the product. The technical specifications must be
strictly adhered to.
If the machine has been switched off by a protective device,
it must not be switched on again until the error has been
corrected.
Beware of damp
Moisture penetrating cables can damage them and
render them useless. Never immerse cable ends in
the pumped fluid or other liquids. Any unused wires
must be disconnected.
When the machine is connected to the electrical control panel,
especially when electronic devices
such as soft startup control or frequency drives are used, the
relay manufacturer's specifications
must be followed in order to conform to EMC. Special separate
shielding measures e.g. special
cables may be necessary for the power supply and control
cables.
The connections may only be made if
the relays meet the harmonized GB/EU
standards. Mobile radio equipment may
cause malfunctions.
2.10 Ground connection
Our products (machine including protective devices and operating
position, auxiliary hoisting gear) must always be grounded. If
there is a possibility that people can come into contact with
the machine and the pumped liquid (e.g. at construction sites),
the grounded connection must be additionally equipped with a
fault current protection device.
The electrical products conform to motor protection class IP
68 in accordance with the valid norms.
2.11 Safety and control devices
Our products are equipped with various safety and control
devices. These include, for example suction strainers, thermo
sensors, sealed room monitor etc. These devices must never
be dismantled or disabled.
Equipment such as thermo sensors, float switches, etc. must
be checked by an electrician for proper functioning before
start-up. Please remember that certain equipment requires a
relay to function properly, e.g. posistor and PTC sensor. This
relay can be obtained from the manufacturer or a specialist
electronics dealer.
Staff must be informed of the installations used and
how they work.
Never operate the machine if the safety and
monitoring devices have been removed or damage,
or if they do not work.
2.12 Sound pressure
Depending on the size and capacity (kW), the products produce
a sound pressure of approximately 70 dB (A) and 110 dB (A).
The actual sound pressure, however, depends on several
factors. These include, for example, the instal-lation type (wet,
dry, transportable), fastening of accessories (e.g. suspension
unit) and pipeline, operat-ing site, immersion depth, etc.
Once the product has been installed, we recommend that the
operator make additional measurements under all operating
conditions.
In accordance with the laws in effect, guidelines,
standards and regulations, ear protection must be
worn if the sound pressure is greater than 85 dB (A)!
The operator is responsible for ensuring that this is
observed!
2.13 Warranty
This chapter contains the general information on the warranty.
Contractual agreements have the highest priority and are not
superseded by the information in this chapter!
The manufacturer is obliged to correct any defects found in
the products it sells, provided that the following requirements
have been fulfilled:
General information
- The defects are caused by the materials used or the way the
product was manufactured or designed.
- The defects were reported in writing to the manufacturer
within the agreed warranty period.
- The product was used only as prescribed.
- All safety and control devices were connected and inspected
by authorized personnel.
Warranty period
If no other provisions have been made, the warranty period
applies to the first 12 months after initial start-up or to a max.
of 18 months after the delivery date. Other agreements must
be made in writing in the order confirmation. They will remain
valid at least until the agreed warranty period of the product
has expired.
Spare parts, add-ons and conversions
Only original spare parts as supplied by the manufacturer may
be used for repairs, replacements,add-ons and conversions.
Only these parts guarantee a long working life and the highest
level of safety. These parts have been specially designed for
our products. Self-made add-ons and conversions or the use
of non-original spare parts can seriously damage the product
and/or injure personnel.
Maintenance
The prescribed maintenance and inspection work should be
carried out regularly. This work may only be carried out by
qualified, trained and authorized personnel. The maintenance
and inspection log supplied must be properly updated.
This enables you to monitor the status of inspections and
maintenance work. Quick repairs not listed in this operation
and maintenance manual and all types of repair work may only
be performed by the manufacturer and its authorized service
centers.
Damage to the product
Damage as well as malfunctions that endanger safety must be
eliminated immediately by authorized personnel. The product
should only be operated if it is in proper working order. During
the agreed warranty period, the product may only be repaired
by the manufacturer or an authorized service workshop! The
manufacturer reserves the right to recall the damaged product
to the factory for inspection!
Exclusion from liability
No liability will be assumed for product damage if one or more
of the following points apply:
- Incorrect design on our part due to faulty and/or incorrect
information provided by the operator or customer
- Non-compliance with the safety instructions, the regulations
and the requirements set forth by law and this operating
and maintenance manual
- Incorrect storage and transport
- Improper assembly/dismantling
- Improper maintenance
- Unqualified repairs
- Faulty construction site and/or construction work
- Chemical, electrochemical and electrical influences
- Wear
This means the manufacturer’s liability excludes all liability for
personal, material or financial injury.
2.14 technical condition
Our products are manufactured by the most advanced technology
and meet the technical safety standards of the State. See
technical Documentation for additional information.
2.15 technical terms
Dry run
The product is running at full speed, however, there is no liquid
to be pumped. A dry run is to be strictly avoided. If necessary, a
safety device must be installed.
“wet” installation type
This installation type requires the product to be immersed in
the pumped fluid. It is completely surrounded by the pumped
fluid. Please observe the values for the maximum submersion
depth and the minimum water coverage.
“transportable” installation type
With this installation type. the product is equipped with a
pedestal. It can be installed and operated at any location.
Please observe the values for the maximum submersion depth
and the minimum water coverage, and remember that the
surfaces of the product become very hot.
“S1” operating mode (continuous operation)
At the rated load, a constant temperature is reached that
does not increase even in prolonged operation. The operating
equipment can operate uninterruptedly at the rated load
without exceeding the maximum permissible temperature.
“S2” operating mode (short-term operation)
The period of service at the rated load is short in comparison
to the subsequent pause. The maximum operating period
is indicated in minutes, for example, S2-15. The operating
equipment can operate during this time uninterruptedly at
the rated load without exceeding the maximum permissible
temperature. The pauses must continue until the machine
temperature no longer exceeds that of the coolant by more
than 2K .
“Siphoning operation”
Siphoning operation is similar to dry running. The product
operates at fullspeed, but only small amounts of liquid are
pumped. Siphoning operation is only possible with certain
types;
Dry-run protection
The dry-run protection is designed to automatically shut
down the product if the water level falls below the minimum
water coverage value of the product. This is made possible by
installing a float switch.
Level control
The level control is designed to switch the product on or
off depending on the filling level. This is made possible by
installing a float switch.
Use in siphoning mode is not permitted. According
to the type of installation,the machine must be
submerged in pumped liquid at least up to the top
edge of the pump or motor housing.
3 Product description
3.1 Overview
The machine is manufactured with great care and is subject to
constant quality controls. Trouble-free operation is guaranteed
if it is installed and maintained correctly.
3.2 Proper use and fields of application
Submersible motor pumps are used in pumping sewage water,
waster water, surface water and clear water in municipal
application,building services and part of industrial usage. The
dirty waste water may also contain solid particles depending
on the model of the machine. Motors are installed wet.
3.3 Conditions of use
- The machine can be used to pump slightly dirty water.
- The machine must be used in proper range of Head (-30%
to +10% of rated Head). The maximum submersion is 10m.
Depending on the installation types, the machine must be
submerged in pumped liquid at least 1/2 up to the top edge
of motor. 30kW and up can run with the motor exposing
above water, but the minimum water coverage is required.