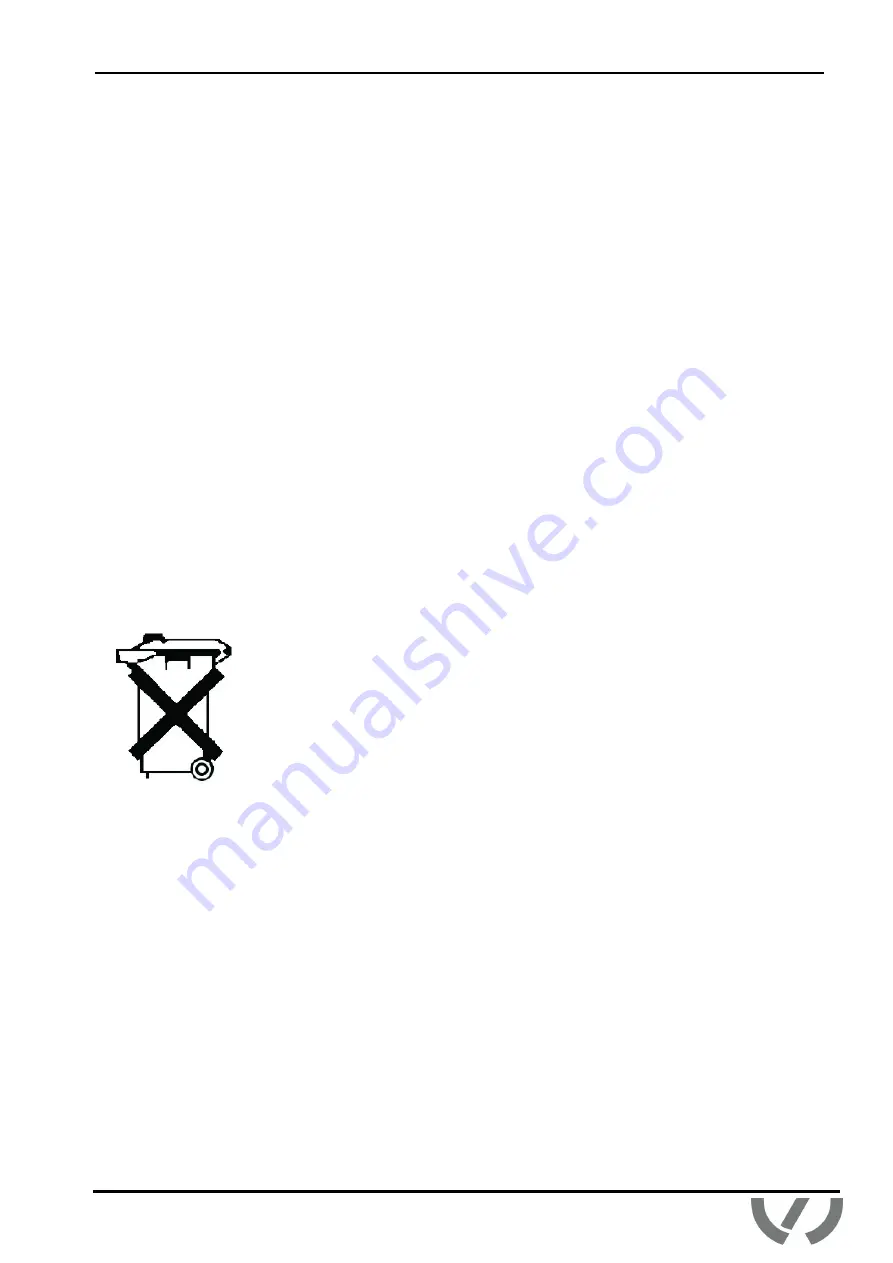
Operation Manual
MIG-MAG Alu welding - brazing / VAS 821 003
©
Wieländer + Schill
Page 21
5 MAINTENANCE
Disconnect the power cable from the socket before any maintenance and troubleshooting.
The device is almost maintenance free.
It`s necessary to check feeding wheel, pressure roller and inflow nozzle regularly. Clean
nozzles and tips regularly.
Please, change the contact tip on the torch regularly
The complete set of pressure hoses should be cleaned up from time to time, because of em-
bedded dust and parts.
The contact nozzle of the torch is wearing up subsequently. When the hole in the nozzle is
too large, it is necessary to change the nozzle. The metal drops are embedding in the inner
walls of the torch cover. Take them out if necessary. The separator is helpful and it is also
a prevention against the firm spatter build-up.
Any damaged cables must be changed at once.
5.1 Disposal of the machine
Do not dispose of electrical equipment together with the normal waste!
In observance of European Directive 2002/96/EC on Waste Electrical
and Electronic Equipment and its implementation in accordance with
national law, electrical equipment that has reached end of its life must
be collected separately and returned to an environmentally compatible
recycling facility.
Содержание VAS 821 003
Страница 1: ...02 2021 MIG MAG ALU welding brazing Operation Manual REV 1 0 VW AG I VAS 821 003 UK ...
Страница 30: ...MIG MAG Alu welding brazing VAS 821 003 _Operation Manual Page 30 Wieländer Schill ...
Страница 31: ...Operation Manual MIG MAG Alu welding brazing VAS 821 003 Wieländer Schill Page 31 ...
Страница 32: ...MIG MAG Alu welding brazing VAS 821 003 _Operation Manual Page 32 Wieländer Schill ...