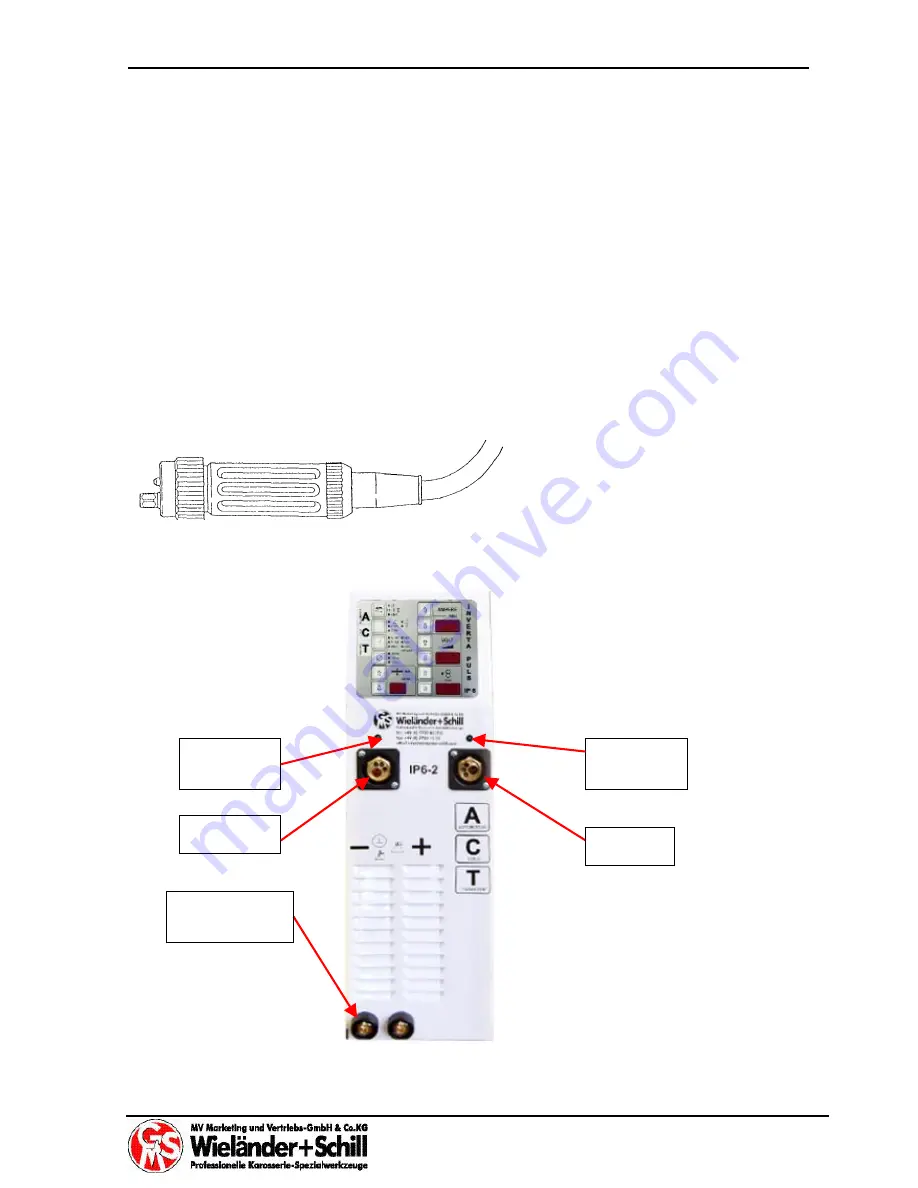
Operation manual
Inverta Puls IP6-2 ACT
Page 5 of 20
2 PUTTING INTO OPERATION
2.1 Connecting to the electric network
Check if the voltage stated on the device label complies with rated voltage of alternate volta-
ge of your electric network.
The device can be connected to electric socket equipped with protective contact installed by
authorized electrician. Current circuit of socket must be protected with 16Amp melting safety
fuse or circuit breaker.
The device is delivered without plug. For connections can be used only plugs and sockets
according to CEE standard.
2.2 Connecting the MIG/MAG torch
For torch connecting is used EURO Standard torch connector.
Please, tighten the connector well to eliminate the conduction losses. A loose connection
can cause damage of the machine and torch.
Work piece
clamp
Torch A
Torch B
Torch B
state LED
Torch A
state LED