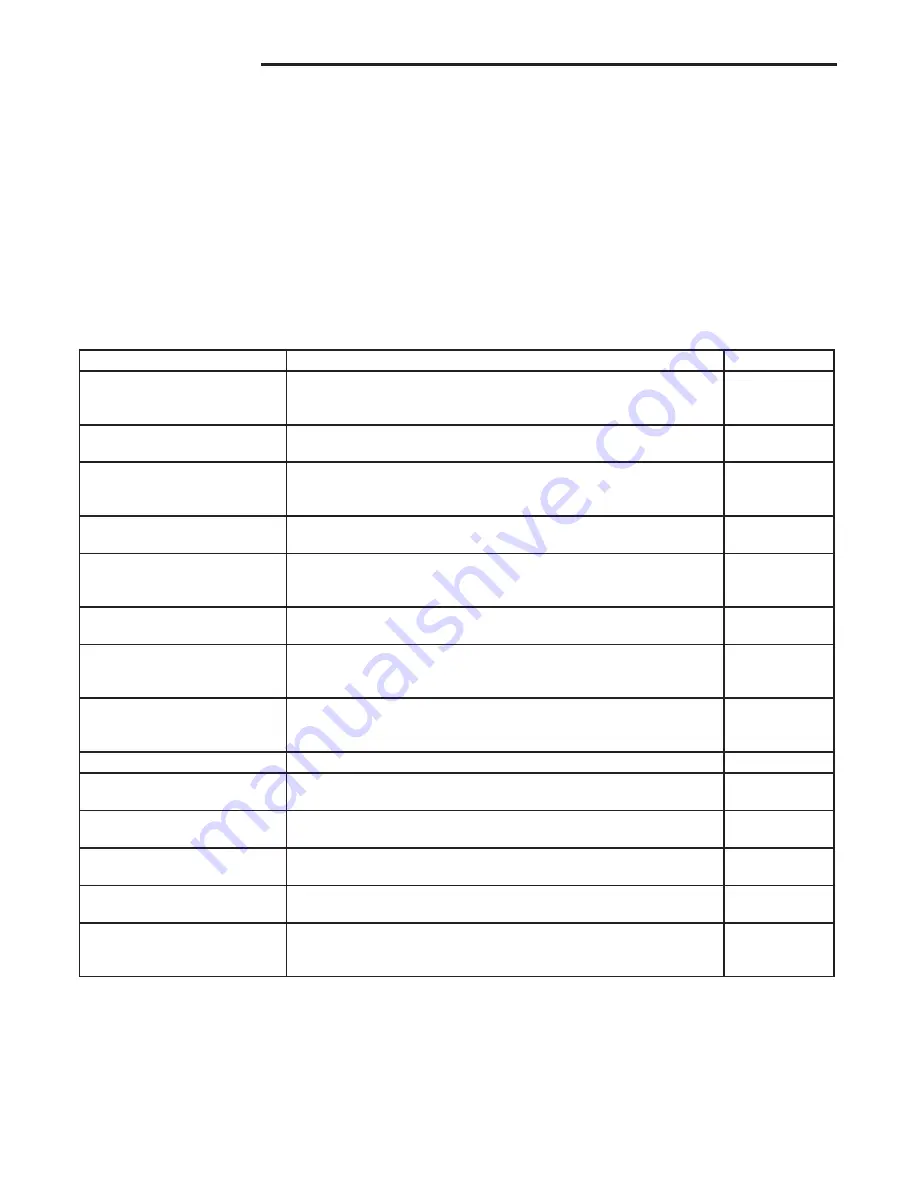
2
SPECIFICATIONS
ELECTRICAL RATINGS [@ 77
O
F (25
O
C)]:
Input Voltage:
120 VAC, 60 Hz (Class II transformer required)
Max. Input Current @ 24 VAC:
800mA + MV
Relay Load Ratings:
1st Stage Gas Valve Relay: 1.5 amps @ 24 VAC, 60 Hz
2nd Stage Gas Valve Relay: 0.5 amps @ 24 VAC, 60 Hz
Ignitor: 2.0 amps @ 132 VAC, 60 Hz
Inducer Relays: 2.2 FLA - 3.5 LRA @ 120 VAC
Humidifier Load: 1.0 A max @ 120 VAC
Electronic Air Cleaner Load: 1.0 A max @ 120 VAC
Circulator Output :
12 mA RMS @ 30 VAC
Flame Current Requirements:
Minimum current to ensure flame detection: 0.3 µa DC*
OPERATING TEMPERATURE RANGE:
-40° to 175°F (-40° to 80°C)
HUMIDITY RANGE:
5% to 93% relative humidity (non-condensing)
Timing Specs:
(@ 60 Hz**)
maximum
Flame Failure Response Time:
2.0 sec
Gases Approved:
Natural, Manufactured, Mixed, Liquid Pe-
troleum, and LP Gas Air Mixtures are all approved for use.
50M58-289 TIMING TABLE
(All times are in seconds, unless noted otherwise)
Event
Definition
Time
Pre-purge Time
The period of time intended to allow for the dissipation of any unburned
gas or residual products of combustion at the beginning of a furnace
operating cycle prior to initiating ignition
15
Igniter Warm-up Time
The length of time allowed for the igniter to heat up prior to the initiation
of gas flow.
17
Trial for Ignition Period (TFI)
The period of time between initiation of gas flow and the action to
shut off the gas flow in the event of failure to establish proof of the
supervised ignition source or the supervised main burner flame.
4
Ignition Activation Period (IAP)
The period of time between energizing the main gas valve and
deactivation of the ignition means prior to the end of TFI
3
Retries
The additional attempts within the same thermostat cycle for ignition
when the supervised main burner flame is not proven within the first
trial for ignition period.
2 times
Valve Sequence period
Valve sequence period equals 5 seconds trial for ignition period x
(1 initial try + 2 retries) + 12 seconds.
15
Inter-purge
The period of time intended to allow for the dissipation of any unburned
gas or residual products of combustion between the failed trial for
ignition and the retry period.
30
Post-purge Time
The period of time intended to allow for the dissipation of any unburned
gas or residual products of combustion at the end of a furnace burner
operating cycle. Post-purge begins at the loss of flame sense.
15
Lock-Out Time
ANSI standard rated module timing.
300
Heat Delay-To-Fan-On
The period of time between proof of the supervised main burner flame
and the activation of the blower motor at Heat speed.
30
Heat Delay-To-Fan-Off*
The period of time between the loss of a call for heat and the
deactivation of the blower motor at Heat speed.
90/120/150/180
Cool Delay-To-Fan-On
The period of time after a thermostat demand for cool before
energizing the circulator blower motor at Cool speed.
5
Cool Delay-To-Fan-Off
The period of time between the loss of a call for cool and the
deactivation of the blower motor at Cool speed.
45
Automatic Reset Time
After one (1) hour of internal or external lockout, the control will
automatically reset itself and go into an auto restart purge for 60
seconds.
60 minutes
*These times will vary depending on option switch position.