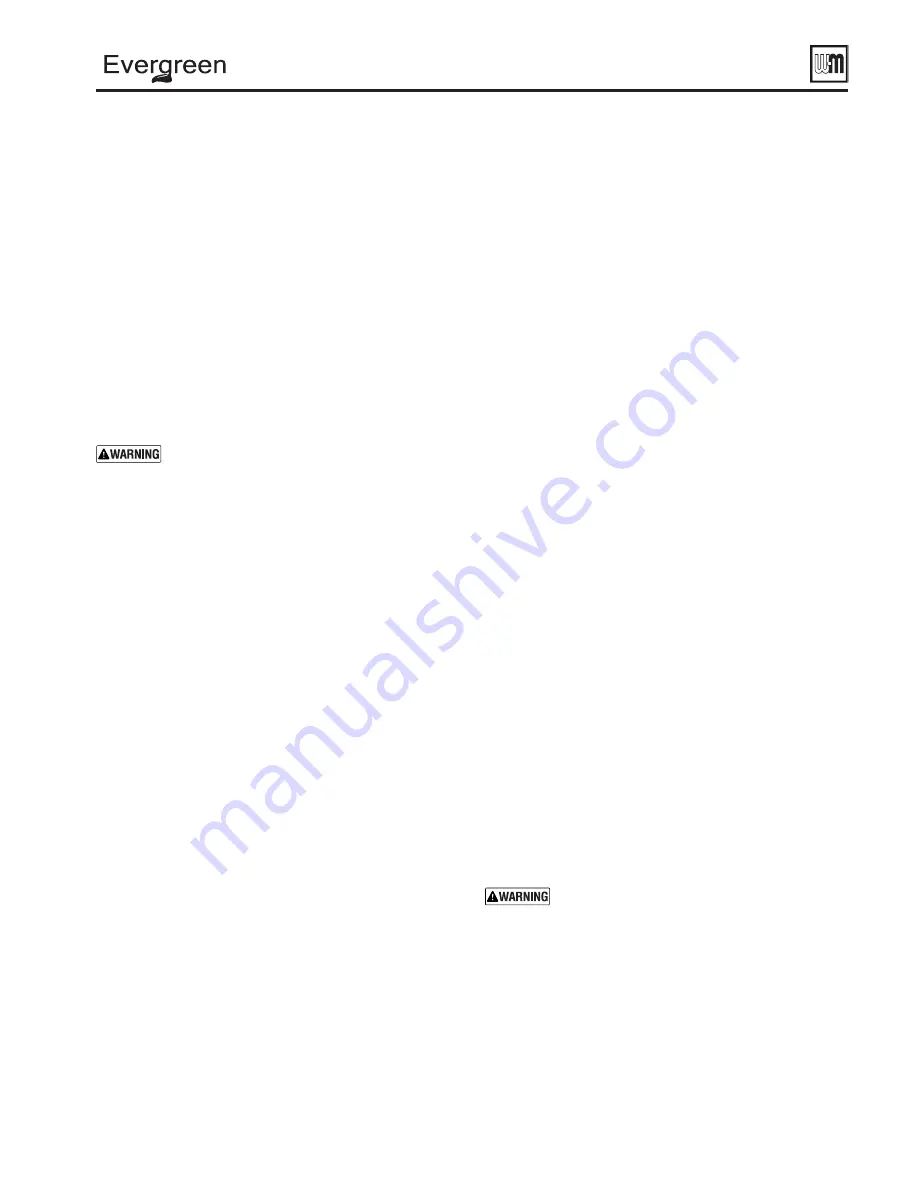
Annual startup
(continued)
Check air openings
1. Verify that combustion and ventilation air openings to the
boiler room and/or building are open and unobstructed.
2. Check operation and wiring of automatic combustion air
dampers, if used.
3. Verify that boiler vent discharge and air intake are clean and
free of obstructions.
Flue vent system a nd air piping
1. Visually inspect entire flue gas venting system and
combustion air piping for blockage, deterioration or leakage.
Repair any joints that show signs of leakage in accordance
with vent manufacturer’s instructions. Verify that air inlet
piping is connected and properly sealed.
Failure to inspect for the above conditions and
have them repaired can result in severe personal
injury or death.
Check water syste m
1. Verify all system components are correctly installed and
operational.
2. Check the cold fi ll pressure for the system. Verify it is correct
(usually around 12 PSIG).
3. Watch the system pressure as the boiler heats up (during
testing) to ensure pressure doesn’t rise too high. Excessive
pressure rise indicates expansion tank sizing or performance
problem.
4. Inspect automatic air vents and air separators. Remove air
vent caps and briefl y press push valve to fl ush vent. Reinstall
caps. Make sure vents do not leak. Replace any leaking vents.
5. Check system water chemistry (pH, hardness and inhibitor
level). See page 91 .
Check e xpansion tank(s)
1. Expansion tanks provide space for water to move in and
out as the heating system water expands due to temperature
increase or contracts as the water cools.
2. See page 41 or page 45 depending on system type for
information.
3. Tank
types
•
Closed-type
— welded gas tight and located above
boiler. Tank is partially fi lled with water, leaving an air
cushion for expansion.
• Make sure a closed-type tank is fi tted with a tank
fi tting, such as the B & G Tank-trol or Taco Taco-
trol. This fi tting reduces gravity circulation of air-
saturated tank water back to the system and prevents
the air from bubbling up through the water as it
returns from the system.
• Do not use automatic air vents in systems with
closed-type tanks. The air will escape from the system
instead of returning to the tank.
• Eventually, the tank will waterlog and no longer
control pressurization. The boiler relief valve will
weep frequently.
•
Diaphragm- or bladder-type
— welded gas tight with
a rubber membrane to separate the tank pressurizing air
and the water. May be located at any point in the system,
but preferably located on the suction side of the system
circulator.
• Systems with this type of expansion tank require at
least one automatic air vent, preferably located on
top of an air eliminator, as shown in examples in
this manual.
4. If relief valve has tended to weep frequently, the expansion
tank my be water logged or undersized.
a.
Diaphragm- or bladder-type expansion tank
— fi rst,
check tank size to be sure it is large enough for the system.
If size is too small, add additional tank (or tanks) as
necessary to provide suffi cient expansion. If tank size is
large enough, remove tank from system and check charge
pressure (usually 12 PSIG for residential applications). If
tank won’t hold pressure, membrane has been damaged.
Replace tank.
b.
Closed-type expansion tank
— tank is most likely
waterlogged. Install a tank fitting if not already
installed. Then check fi ll level per fi tting manufacturer’s
instructions. If fi ll level is correct, check tank size against
manufacturer’s instructions. Replace with a larger tank
if necessary.
Inspect ignition elec trode
1. Remove the ignition electrode from the boiler heat exchanger
access cover (see item 23, page 4 ). Disconnect the ground wire
and ignition cable connected to the electrode.
2. Discard the ignition electrode gasket.
3. Remove any white oxides accumulated on the ignition
electrode using steel wool. If the ignition electrode cannot be
cleaned satisfactorily, replace ignitor with a new one.
4. Slide new gasket on to the ignition electrode. Reinstall
ignition electrode, making sure gasket is in good condition
and correctly positioned.
TORQUE LIMIT
— Use a torque wrench when
tightening the two ignition electrode retainer
screws. DO NOT exceed 20 inch-pounds.
Part number 550-100-191/0917
103
®
g
as-fired water boiler —
70/110/155
Boiler Manual
Содержание Evergreen EVG 110
Страница 71: ...Part number 550 100 191 0917 71 gas fired water boiler 70 110 155 Boiler Manual Notes...
Страница 90: ...Part number 550 100 191 0917 90 gas fired water boiler 70 110 155 Boiler Manual Notes...
Страница 116: ...Part number 550 100 191 0917 116 gas fired water boiler 70 110 155 Boiler Manual Notes...