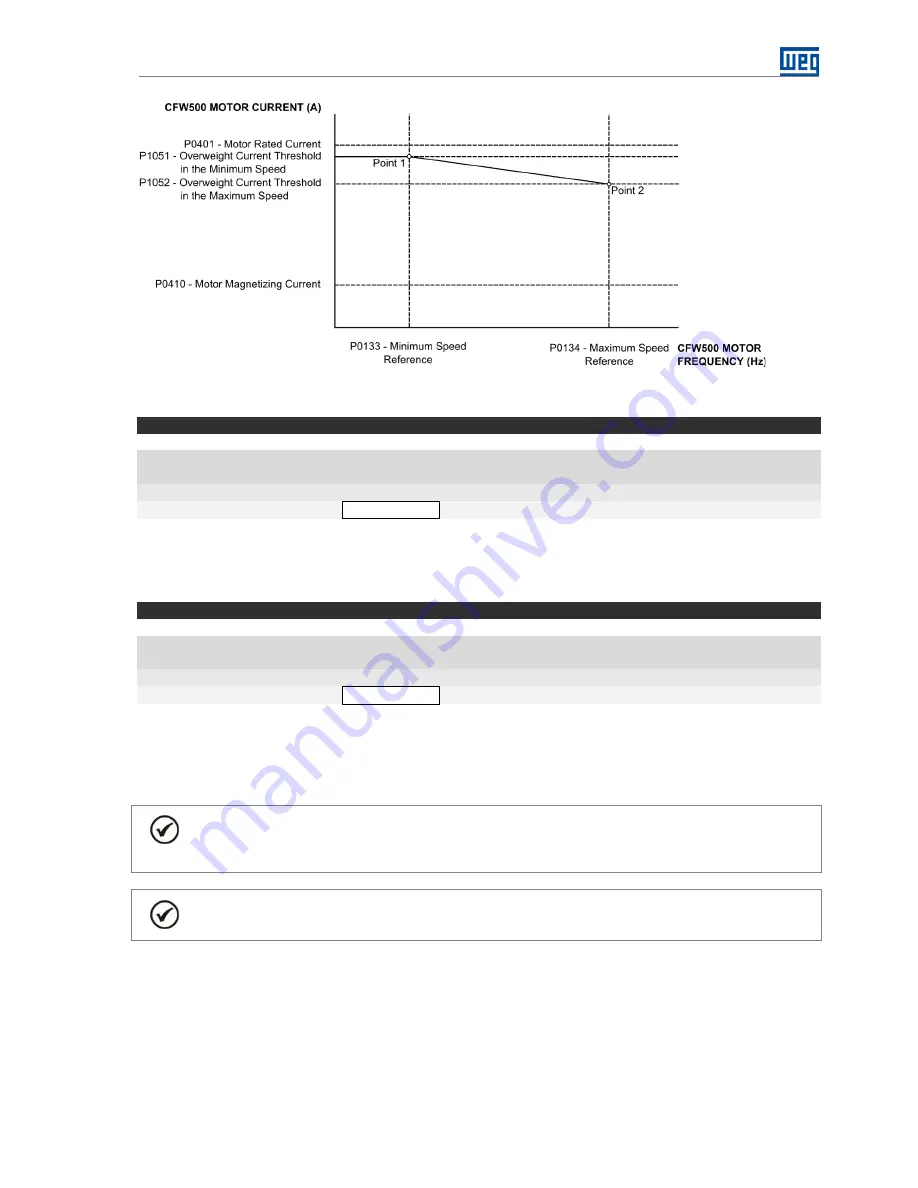
Parameters Description
Crane | 61
Figure 3.7 – Overweight curve
P1053 – Overweight Detection Delay Time
Adjustable
0.00 to 650.00 s
Factory Setting:
1.00 s
Range:
Proprieties:
Access groups via HMI:
SPLC
Description:
This parameter defines a delay time after the hoisting command has been given, before initiating the overweight
monitoring according to the overweight curve defined in P1051 and P1052.
P1054 – Overweight Alarm (A770) Delay Time
Adjustable
0.00 to 650.00 s
Factory Setting:
0.50 s
Range:
Proprieties:
Access groups via HMI:
SPLC
Description:
This parameter defines a delay time after the motor current becomes greater than or equal to the overweight
curve defined in P1051 and P1052, during a hoisting command, before the alarm “A770: Detected Overweight”,
is generated.
NOTE!
With the overweight detection, an emergency stop is executed respecting the ramp defined in
P0101.
NOTE!
The alarm is reset when a load lowering command is given for at least 100 ms.
The overweight detection operation diagram, considering that the crane vertical motion has been configured for
two speed references obtained from the digital input logic, is presented next. Only the motor frequency has
been considered in the brake control logic. The digital output DO4 is used to indicate the overweight alarm.
Содержание Crane CFW500 series
Страница 2: ......