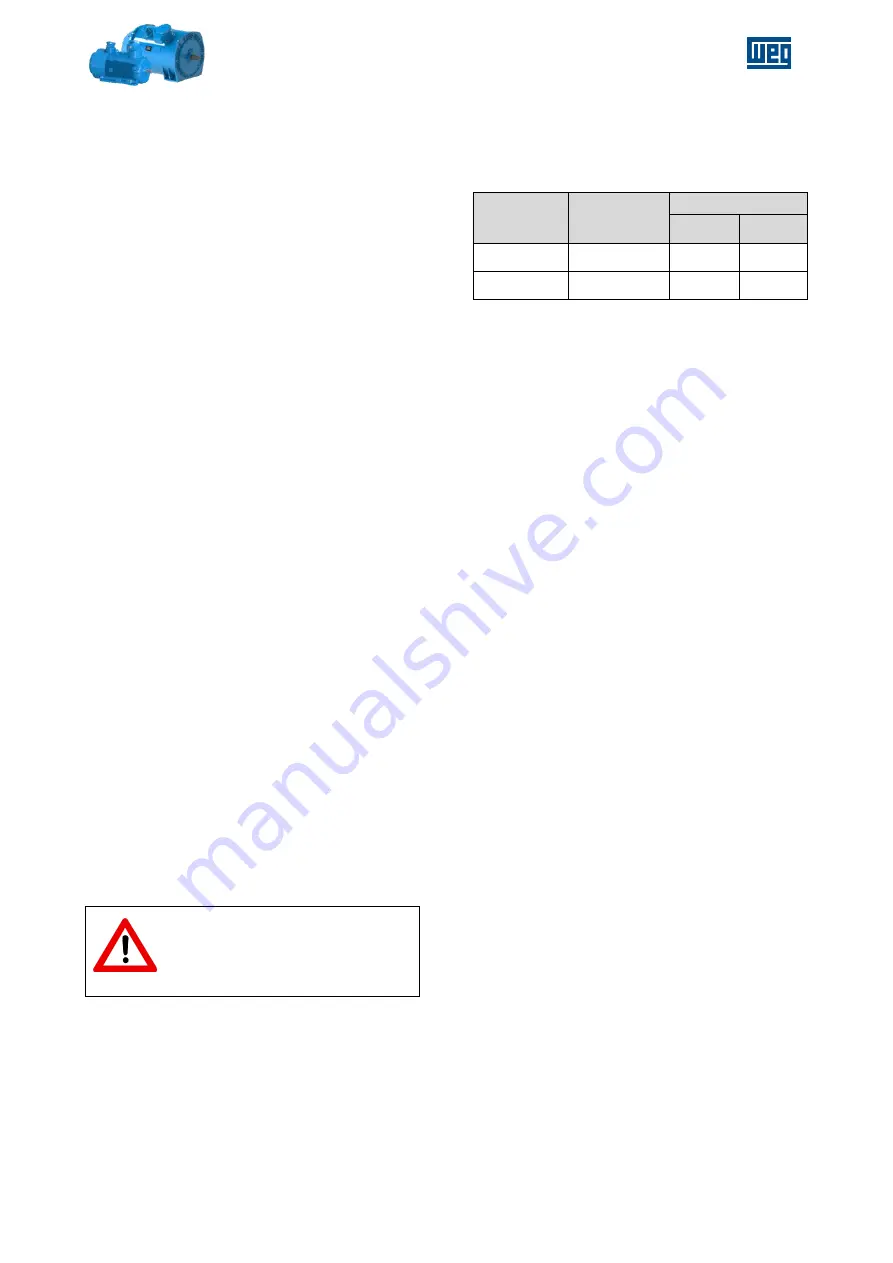
Flameproof motors | 47
www.weg.net
8.2.10.1 GENERAL INSTRUCTIONS
Sleeve bearing performance is dependent on
proper installation, lubrication and maintenance.
Before assembling the bearing carefully read all
instructions contained herein to become familiar
with the complete bearing assembly procedure.
A proper maintenance of sleeve bearings includes
periodical checking of the level and actual condition
of the lubricating oil, checking of noise level and
vibration of the bearings, follow-up of the operating
temperature, and fastening of the fixing and
assembly bolts. The frame must be kept clean, free
from dust, oil and dirt to facilitate cooling system.
Threaded holes for connecting the thermometer, oil
sight glass, oil inlet, and immersion heater, or
cooling coil (for oil sump thermometer or circulating
pump with adapter) are provided on either side, so
that all connections can be made on the right or left
side of the bearing housing as required.
The oil drain plug is located centrally on the
underside of the bearing housing.
In case of circulating oil lubrication, the outlet
connection should be screwed into the threaded
hole of an oil sight glass.
If the bearing is electrically insulated, the spherical
liner seat surfaces in the housing are lined with a
non-conducting material.
Do not remove this lining.
The antirotation pin is also insulated and the shaft
seals are manufactured from a special non-
conducting material.
Temperature monitoring instruments with contact
to the bearing liner should be insulated
appropriately (i.e., insulated protection tubes,
synthetic fittings, etc.)
Water-cooled bearings are provided with the
cooling coil installed. Care must be taken to protect
the connections from damage when handling the
housing prior to installation.
DANGER
Do not remove the breathing
devices (20) when the motor is in
operation.
8.2.10.2 OIL
TYPE
AND
CHARACTERISTICS
Table 8-16 - Oil specification and characteristics
Polarity
Lubricant
Specification
Viscosity Range
ISO 40ºC
[cSt]
SSU
100ºF [s]
2 poles
Mineral oil ISO
VG32
28.8
–
35.2
137
– 164
4+ poles
Mineral oil ISO
VG46
41.4
–
50.6
193
– 235
8.2.10.3 DISASSEMBLY OF THE SLEEVE
BEARING SYSTEM (TYPE "EF")
To disassemble the bearing liner and all associated
parts from the bearing housing, carry out the
following
instructions.
Carefully
store
all
disassembled parts in a safe location (see Figure
8-4)
Drive end side:
- Throughly clean the exterior of the bearing
housing. Loosen and remove the oil drain plug
(1) at the bottom of the bearing housing. Drain
the oil from the bearing housing.
- Loosen and remove the bolts (4) that connect
the top half of the bearing housing (5) to the
motor frame cover (3).
- Loosen and remove the bolts (6) that join the
top and bottom half of the bearing housing (2
and 5).
- Use the lifting eyebolts (7) to lift (by hand or
hoist) the top half of bearing housing (5) straight
up, so that the cap is completely disengaged
from the lower halves of the stationary baffle (9)
labyrinth seals, labyrinth seal carrier (18) , and
the bearing liner (10).
- Pull the top bearing housing forward out of and
away from the bearing area. Loosen and
remove the bolts (17) securing the top half of
the stationary baffle. Loosen and remove the
bolts (8) securing the upper half of the seal
carrier (18).
- Lift (by hand or hoist) the upper half of the
bearing liner (11) and remove it.
- Loosen and remove the bolts at the split line of
the oil ring (12). Carefully disengage the dowels
holding the oil ring halves together and remove
the oil ring.
- Remove the garter springs that encircle the
labyrinth seals and remove the top half of each
seal. Rotate the bottom half of each seal out of
the grooves in the seal carrier and bearing
housing and remove them.
- Disconnect and remove RTD's, thermocouples,
or any other temperature detecting instruments
that enter the lower half of the bearing liner.
- Using a hoist or jack, raise the shaft slightly so
that the lower half of the bearing liner can be
rolled out of the bearing housing.