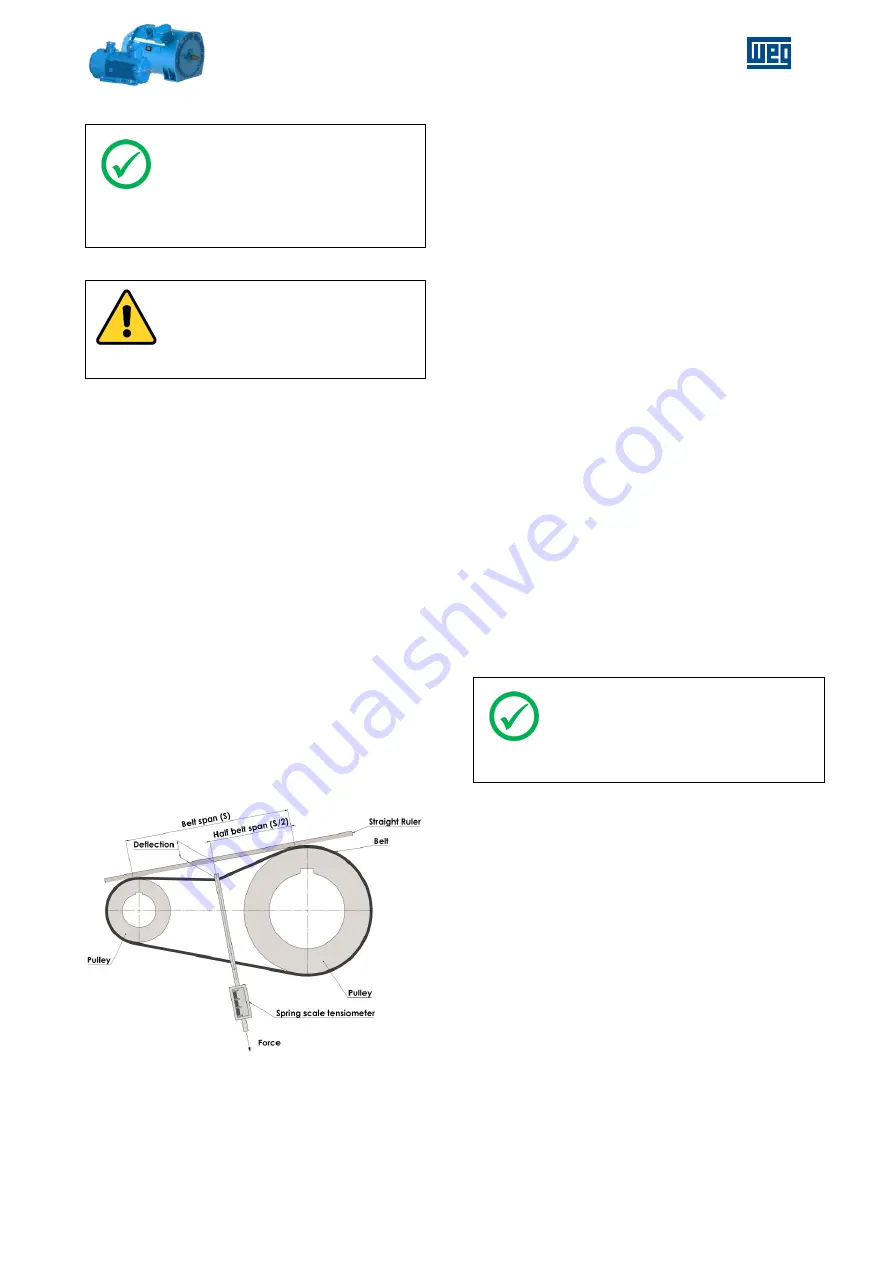
Flameproof motors | 29
www.weg.net
NOTE
A belt with excessive tension
increases the force on the shaft end
causing
vibrations
and
fatigue
leading to a possible shaft rupture.
ATTENTION
Excessive belt tension may cause
bearing damage and lead to shaft
rupture.
BELT TENSION:
In general, proper belt tensions
should be the lowest possible at which the belts will
not slip at peak load conditions.
Maintaining the proper belt tension is very
important. If tension is too high, the drive could
overload bearings and pull shafts out of alignment.
Belt tensions must be measured with a tension
tester.
The belt should be monitored regularly during the
first hours of operation.
Correct tension of the drive may be obtained if the
belt tension is measured, set and checked using
one of the following methods:
MEASURING BELT TENSION BY DEFLECTION
Force deflection method
– The belt tension is
determined, with a tensiometer or other spring
scale type tester, by measuring the required force
to deflect the center of the belt a given distance.
Tensiometers may be obtained through belt
manufacturers or distributors.
Figure 5-15 - Belt span lenght.
With a tensiometer or other spring scale type tester
press the opposing end of the equipment to the
midpoint of the belt span and apply a force on the
equipment to obtain a desired belt deflection of
0.4mm for every 26mm of belt span. For example,
if the span length is 1000mm (1m), the disired belt
deflection is 16mm.
For a single belt drive, the deflection observed in
the tensiometer should be lined up with the bottom
of a straight edge placed on the outside diameters
of the two sheaves. For a multiple belt drive, the
belt deflection is lined up with the top of the next
belt. Take a reading from each belt for an average.
The tensiometers instructions for use and belt
tension measurement are supplied with the
equipment and they are very simple, allowing the
installers or end users to perform a correct belt
tensioning adjustment taking into account the
recommendations
of
the
equipment
manufacturers.
MEASURING BELT TENSION BY FREQUENCY
An electronic tensiometer is used to measure the
vibration of the belt span and instantly it converts
the vibration frequency into belt static tension. By
measuring the natural frequency of the tensioned
belt, the tension of the belt can be calculated.
To determine the status of the belt, the force
obtained by the deflection or frequency methods
should be compared with the values of tension
forces recommended in the tables of the belt
manufacturers.
Excessively small pulleys should be avoided; these
cause shaft flexion as belt traction increases with
the decrease of pulley size.
NOTE
When specific pulleys are required,
contact WEG in order to insure a
correct designing.
Due to the existing tensions on the belts, there is a
reaction acting as radial load over the motor shaft
end.
The data to calculate such reaction (radial force)
are:
- Output transmitted [kW] (P);
- Motor speed [rpm] (RPM);
- Diameter of driven pulley [mm] (DPMV);
- Diameter of driver pulley [mm] (DPMT);
- Distance between centers [mm] (
I
);
- Friction coefficient [-] (MI) - (normally 0.5);
- Slip coefficient [-] (K);
- Belt contact angle on smaller pulley [rad] (alfa);
- Radial force applied to the shaft end [N] (FR).