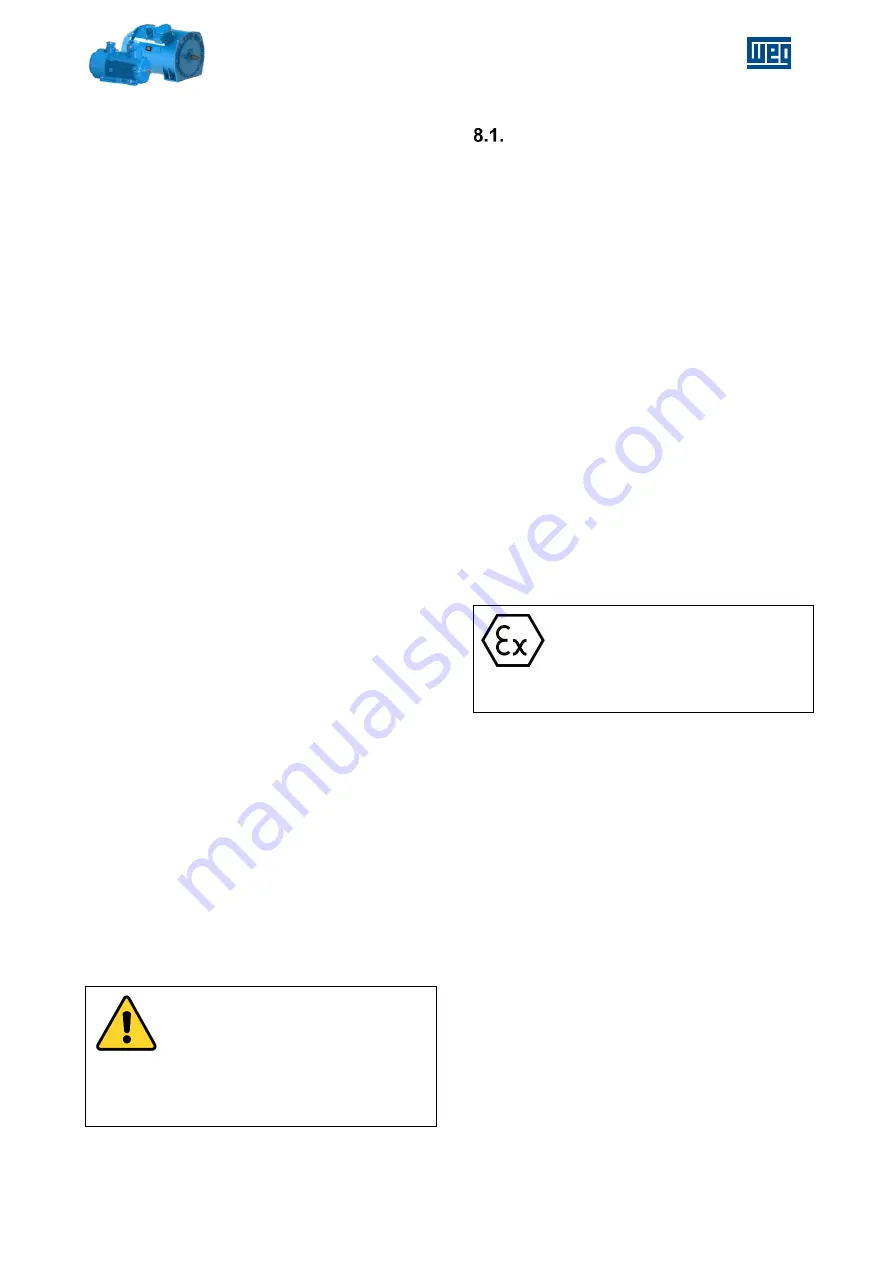
Flameproof motors | 37
www.weg.net
7.
NOISE LEVEL
To ensure a low noise level operation, the source
of noise must be identified and how such noise is
transmitted through the ambient. The following
motor components may generate noises within an
audible range:
- Cooling system;
- Bearings;
- Magnetic circuit.
The noise level of an electric motor, however,
depends mainly on its size, cooling system, speed
and degree of mechanical protection (enclosure).
Cooling system is airborne and usually affects only
the noise level in the area where motor is installed.
This noise level may be reduced by using mufflers.
Noises caused by bearings or the magnetic circuit
are originated from mechanical vibrations of
individual parts or the motor set, and they are
transmitted through the foundation, walls and
machine cooling tubes. This type of noise can be
reduced by installing the motor on suitable
designed anti-vibration dampers. It is important to
note that incorrect dampers may even increase
vibrations.
8.
MAINTENANCE
A well-programmed maintenance of electric motors
can be summed up as a periodical inspection of
insulation levels, temperature rise (winding and
bearings), wears, bearing lubrication and useful
life, occasional checking of fan air flow and
vibration levels.
For a flameproof motor enclosure and flameproof
joints
condition,
vigilance
and
external
housekeeping must also be in the maintenance
program.
In case one of the above items is not followed
accordingly, unexpected stops of the equipment
may occur. Inspection cycles depend on the type
of the motor and conditions under which it
operates.
Frame must be kept clean, free of dust, dirt or oil in
order to make the cooling process easier.
ATTENTION
On any transportation, motors fitted
with roller, angular contact ball
bearings or sleeve bearings must have
their shaft locked in order to avoid
bearing damage.
To lock the shaft use the shaft locking device
shipped together with the motor. See section 2.2.
CLEANLINESS
Motors should be kept clean, free of dust, dirt and
oil. Soft brushes or clean cotton rags should be
used to clean the motors. A jet of compressed air
should be used to remove non-abrasive dust from
the fan cover and any accumulated grime from the
fan and cooling fins.
Oil or damp impregnated impurities can be
removed with rags soaked in a suitable solvent.
The heat exchanger tubes (if any) must be kept
clean and free of any obstructing object to facilitate
the air circulation.
For the cleanliness of the tubes, a stick with a round
brush at the ends can be used which, inserted in
such tubes, remove all accumulated dirt. In order
to affect this cleanliness, remove the DE noise
suppressor and insert the stick with the brush into
the tubes to remove all the accumulated dust. If
necessary, remove also the fan cover.
Terminal boxes should also be cleaned; their
terminals should be free of oxidation, in perfect
mechanical condition, and all unused space
dust-free.
EX ATMOSPHERE INFORMATION
Before
perform
any
cleaning
operation
make
sure
that
no
potentially explosive atmosphere is
present.
8.1.1. PARTIAL CLEANING
- Drain the condensed water.
- Clean the inside of the terminal boxes.
- Clean the ribs in the frame for ribbed cooled
motors.
- Clean the heat exchanger for tube cooled
motors.
- All flameproof joints, after have been exposed
shall be covered with a corrosion inhibiting
grease (guarantee that they are free of rust
corrosion).
8.1.2. COMPLETE CLEANING
- Clean the dirty windings with a soft brush.
- Grease, oil and other impurities which adhered
on the winding can be removed with a rag
soaked in alcohol. Dry the windings with a jet of
compressed air.
- A jet of compressed air should be used to clean
the bearings and the air ducts in the stator and
rotor cores.
- Drain the condensed water and clean the inside
of the terminal boxes.
- Measure the insulation resistance (see Table