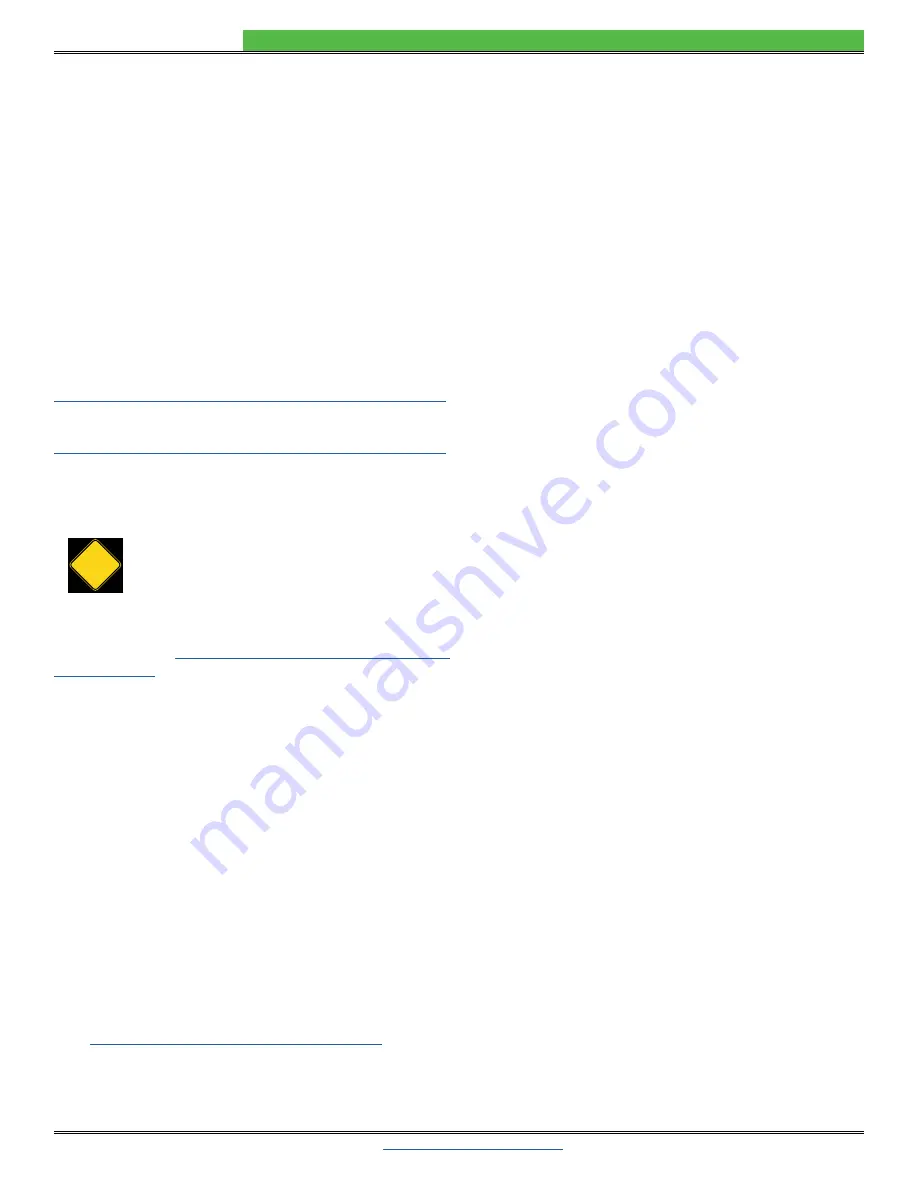
© 2018
8
LDTC2/2 LASER DIODE DRIVER AND TEMPERATURE CONTROLLER
THEORY OF OPERATION
The LDTC2/2 Laser Diode Driver and Temperature
Controller combines the drive power of the WLD3343 with
the temperature stability of the WTC3243.
The LDTC2/2E is enclosed with a cover and base, while the
LDTC2/2O is open frame without cover or base. Accessory
heatsinking is required for LDTC2/2O. Both have the same
functionality.
LASER DIODE DRIVER CURRENT SOURCE
It may be useful to remember that you do not directly set
the laser drive current setpoint; instead, you adjust a voltage
signal that represents the output current. The setpoint
voltage is controlled by the onboard trimpot or by an an
external input.
As current is driven through the load, there is a voltage drop
across the load because of the impedance. As the current
increases, the voltage drop may increase to the point that it
reaches the Compliance Voltage limit of the current source.
Once that occurs, the current source is no longer able to
increase the current driven to the load, even if you increase
the setpoint.
TEMPERATURE CONTROLLER
The WTC3243 delivers bidirectional current to a Peltier Effect
thermoelectric cooler, or unidirectional current to a resistive
heater. The controller adjusts the output current in order to
change the temperature of the sensor that is connected to
the thermal load. The goal is to make the voltage across the
sensor match the setpoint voltage, and then keep them equal
in spite of changes to ambient conditions and variations in
thermal load.
FEATURES
The LDTC2/2 integrated laser driver and temperature
controller includes features that help protect your laser and
make the driver more versatile in a wide array of applications:
• The current limits (laser, heating, cooling) are set by
onboard trimpots and protect the laser from over-current
and over-/under-temperature conditions.
• Slow-start delays the laser current ramp by 250 msec,
and then ramps the current to the setpoint.
• Constant Power operation is available, where the driver
adjusts the laser forward current in order to maintain a
constant photodiode current.
• Available remote LD & TC setpoint control.
• Separate heating and cooling current limits.
SAFETY INFORMATION
& THERMAL DESIGN
CONSIDERATIONS
SAFE OPERATING AREA — DO NOT EXCEED
INTERNAL POWER DISSIPATION LIMITS
Before attempting to operate the LDTC, it is imperative that
you first determine that the laser driver and temperature
controller will operate within the Safe Operating Area (SOA).
Operating the unit outside of the SOA may damage the
controller or the load, and will void the warranty.
Go to the Wavelength Electronics website for the most
accurate, up-to-date, and easy to use SOA calculators:
Laser Diode Drivers:
www.teamwavelength.com/support/design-tools/soa-ld-calculator/
Temperature Controllers:
www.teamwavelength.com/support/design-tools/soa-tc-calculator/
SOA charts are included in this datasheet for quick reference
(
), but we recommend you use the online tools
instead.
To ensure safe operation of the LDTC
controller, it is imperative that you
determine if the unit is going to be operating
within the internal heat dissipation Safe
Operating Area (SOA).
For more information on Safe Operating Area, see our
Application Note
AN-LDTC01: The Principle of the Safe
.
When you assemble and mount the TEC (or heater),
heatsink, and temperature sensor, make sure the physical
connections between the components are solid. We
recommend using thermal paste or thermal washers at the
load/TEC and TEC / heatsink interfaces. The thermistor must
be in firm contact with the load in order to achieve stable and
reliable temperature control.
PREVENT DAMAGE FROM
ELECTROSTATIC DISCHARGE
Before proceeding, it is critical that you take precautions to
prevent electrostatic discharge (ESD) damage to the driver
and your laser. ESD damage can result from improper
handling of sensitive electronics, and is easily preventable
with simple precautions.
For more information regarding ESD, see our Application
Note
AN-LDTC06: Electrostatic Discharge Basics
We recommend that you always observe ESD precautions
when handling the LDTC controller and loads.
!