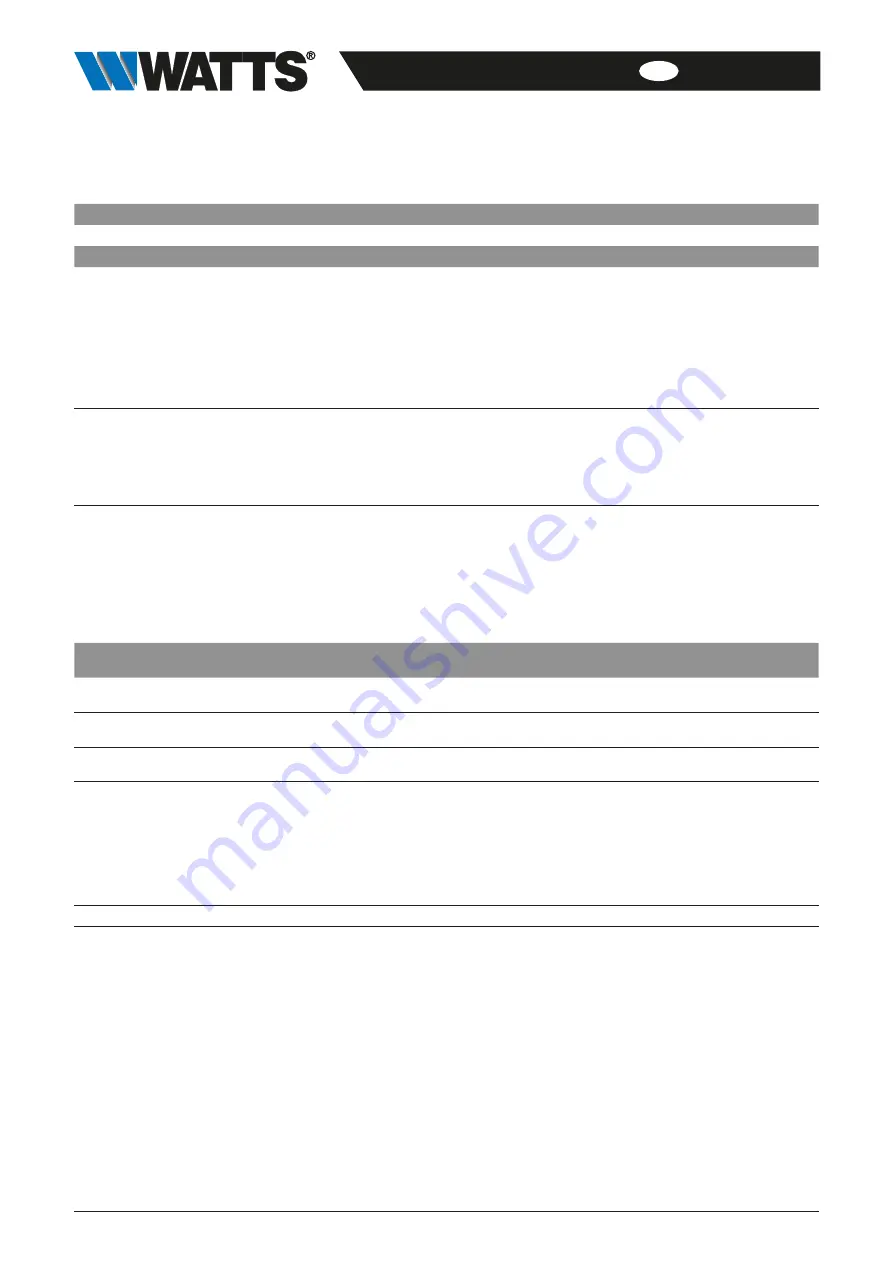
8
ISOMIX F-IM-DE-W-UK-01-2021-Rev4 | Part no. 10070292
EN
ENGLISH
9 Troubleshooting
Fault
Possible cause
Remedy
1
Underfloor heating circuits do not heat up; pump not running
1.1
Temperature limiter (TL) is switching the control station
pump off.
Reason: TL setting is too low.
Set TL to approx. 10 K higher than the underfloor heating
flow temperature.
Note the maximum permitted temperature for the under-
floor heating!
The switching difference of the TL is approx. 5 K.
The control station is ready to operate more quickly if
the TL is removed briefly to cool down to its switching
temperature.
1.2
TL is switching the control station pump off.
Reason: The pump remains switched on despite closed
underfloor heating circuits. The water inside the control sta-
tion is being heated by waste heat from the pump. The TL
switches the pump off when the maximum temperature is
reached!
Remove TL from the control station and fit to supply heat-
ing circuit manifold.
Use electrical control distributor with pump logic (relay). The
pump logic ensures that the pump runs only if at least one
underfloor heating circuit is open.
1.3
The pump is connected to a room thermostat or electrical
control distributor.
If all actuators are closed, the pump switches off. During a
lengthy shutdown, the underfloor heating flow cools down.
The controller therefore causes the 3-way mixer valve to
open. Hot water is injected from the primary heating circuit.
As a result, the control station heats up. When the maxi-
mum temperature of the TL is reached, the contact opens.
The pump does not switch on again.
Remove TL from the control station and fit to supply heat-
ing circuit manifold.
See 1.1
2
Underfloor heating flow temperature cannot be set to the required value or the feed temperature fluctuates
significantly
2.1
Supply and return on the control station have been mixed
up
Check that all connections on the control station are cor-
rect (see Section "Structure" on page <?>)
2.2
The head / pumping level of the pump is set too low
Change the pump setting (see separate pump instruction
manual).
2.3
The differential pressure of the primary pump is too high
(>500mbar)
Change the pump setting (see separate pump instruction
manual) or fit differential pressure controller.
2.4
The heating load is too high for the control station, i.e. heat
consumption exceeds the nominal output of the control sta-
tion. This condition can come about temporarily, for exam-
ple, when heating up a "cold" floor.
Establish maximum heat requirement and compare with
nominal output. The heating circuits may have to be shared
with a second control station with a corresponding heating
circuit distributor.
If this is caused by heating up the underfloor heating for the
first time, it may start working normally after the heating up
phase (2 – 3 days). This is particularly likely in the case of
operation at the upper nominal output limit.
2.5
The thermostat head is defective.
Replace the thermostat head.