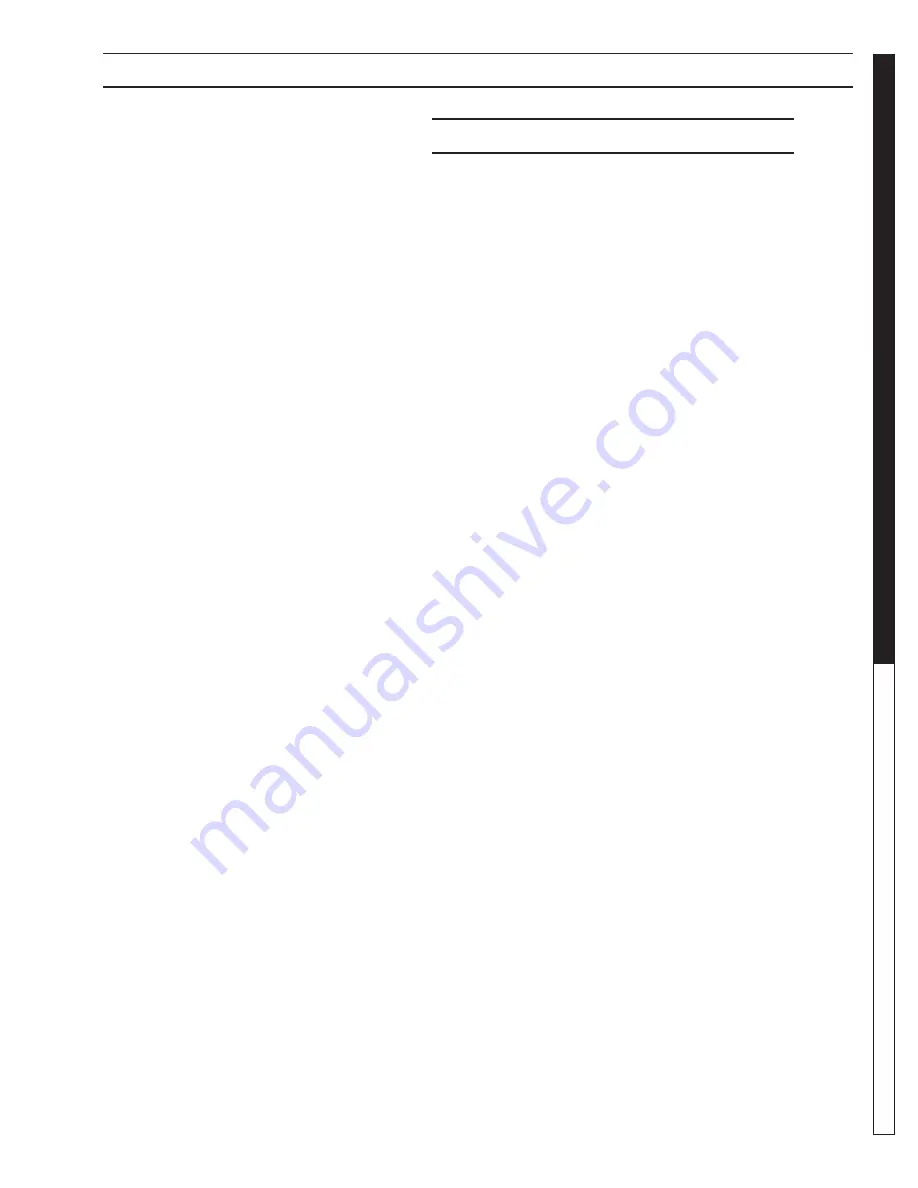
8.913-970.0 - L • WATERMAZE CLP 5024/7034
7
W
A
TER
TREA
TMENT
SYSTEM
OPERA
T
OR’S MANU
AL
INSTALLATION INSTRUCTIONS
c. Keep visitors at a safe distance from work area.
d. Make the workshop safe with padlocks and
master switches.
13. Running the system without water will damage the
pumps and will void the warranty.
14. Release all pressure within the system before
servicing any component.
15. Drain all liquids from the component before
servicing.
16. Check hoses for weak or worn conditions before
each use, making certain that all connections are
secure.
17. Periodically inspect pump and system components.
Perform routine maintenance as required.
18. Do not touch an operating motor. Modern motors
are designed to operate at high temperatures.
19. Do not handle a pump or pump motor with wet hands,
when standing on a wet or damp surface, or in water.
20. The pump motors are equipped with an automatic
resetting thermal protector and may restart unex-
pectedly. Tripping is an indication of motor overload-
ing as a result of operating the pumps at low heads
(low discharge restriction), excessively high or low
voltage, inadequate wiring, incorrect motor connec-
tions, or a defective motor or pump.
21.
IMPORTANT NOTE:
The sump pump is not a
trash pump and is subject to premature failure
unless sump pit baffl ing or additional protection is
provided.
22. Do not stand on the bracket that supports the
Electrical Box, Ozone Generator and the ORP/pH
Controller or on tanks 1 or 2. During installation and
maintenance obtain an OSHA approved ladder.
23. Keep machine from freezing.
24. Do not spray water directly at machine.
INSTALLATION INSTRUCTIONS
1. Because of the nature of the equipment, it is recom-
mended these machines be installed indoors.
2. Locate the CLP on a containment pad to prevent
contamination.
3. Level machine by using shims that will provide ample
support and will not corrode or deteriorate over time.
4. Have a qualifi ed electrician connect the proper
power supply to the electrical control box. It is rec-
ommended that a ground fault circuit interrupter be
installed in the circuit breaker for the CLP.
NOTE:
An electrician needs to locate where the
power supply will enter the electrical box and punch
a hole.
5. Install Orp/pH probes into cone bottom tank. Remove
cap and immerse probes into water. Don't let probes
dry. Save cap for future need.
6. Install the angle face dump valve on bottom of cone
bottom tank. Run air hose from angle face dump
valve to air valve assembly. Follow electrical wiring
diagram for air switch wires.
7. Plumb oil decanter barrel.
8. Run ORP/pH pump hoses from pumps to injectors.
9. Run air from air compressor to machine. Use at least
a 3 CFM air compressor with 60-100 psi.
10. Drill holes for 2" bulkheads and install bulkheads.
Connect the sludge tub assembly by placing the
sludge bag support into the sludge tub. Attach the
sludge bag onto the sludge inlet fi tting using the
screw clamp provided.
11. Attach the 2" fl ex hose to the sludge tub by screwing
the hose barbs into the bulkhead connectors, then
attach the 2" fl ex hose to the hose barb using a hose
clamp. The return line should gravity return to the
catch basin. The 2" inlet fl ex hose should connect
between the cone tank discharge valve and the
sludge bag inlet connector.
12. Build the inlet plumbing from the sump pump dis-
charge port (min. 1-1/2" pipe) to the CLP 1-1/2" inlet
line. If the pipe is to be under the concrete, use 2"
pipe. Lower the sump pump into the sump pit.
13. Position the sump pump in the bottom of sump pit.
a. Elevate on a stand or cinder blocks, 6" off the
pit fl oor, to keep pump from sucking in rocks
or other heavy material that may plug pump or
plumbing.
b. Position the pump away from incoming water to
help prevent cavitation.