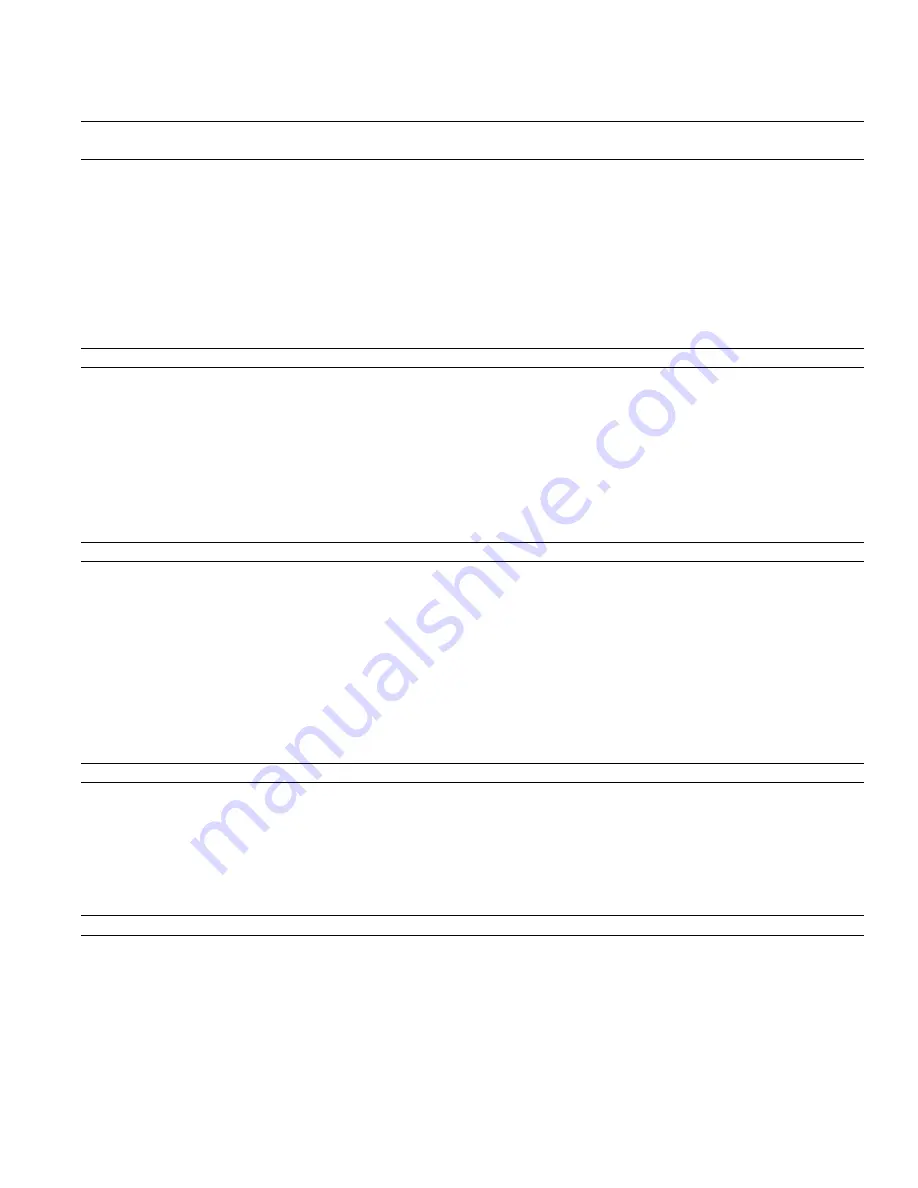
Warner Electric • 800-825-9050
P-2105-WE 819-0549 5/17
9
System Troubleshooting
A. Symptom:
Green LED indicator marked “Power” does not come on when power is applied to the CBC-200 Controller.
Probable Cause
Solution
No Power is applied to the Control
• Check that AC power is applied to the control .
• Incorrect wiring on AC power to the control .
• Check for 120 VAC at Terminals 2 and 3 with an AC Voltmeter .
Internal line fuse is blown
• Check for blown fuse – replace .
Indicator LED is defective
• Check for 120 VAC at Terminals 2 and 3 of the control .
• Check for output voltage at output terminals for Channel 1 and
Channel 2 . If voltage is not present, replace control or board .
B. Symptom: Red LED marked “short” illuminates
Probable Cause
Solution
Shorted magnet coil
• Check resistance of magnet coil used and replace if necessary .
Wiring between control and magnet shorting
• Check for shorted conditions in wiring between the magnets and the
control, and wiring to chassis ground .
Improper magnet coil voltage
• Check magnet for proper coil voltage rating .
Transient noise
• Check for source of transient noise and suppress . Wire control using
shielded cables . Segregate wiring runs .
C. Symptom: Magnets do not engage when power is applied.
Probable Cause
Solution
External switching improperly wired
• Check wiring and switch connections and rewire if necessary .
Torque adjust set to zero (0)
• Set torque adjustment potentiometer to maximum level .
Current range switch improperly set
• Check DIP Switch settings per chart and reset if required .
No power applied to the control
• Refer to Symptom A above .
System incorrectly wired
• Check wiring per the wiring diagram and rewire if necessary .
Fail safe brake used in place
• Check to insure that a fail safe brake is not being used in place of
of power applied brake
a power applied brake . Replace brake with correct brake .
D. Symptom: Magnets do not disengage when power is removed
Probable Cause
Solution
External switches incorrectly wired
• Check wiring of switching circuits and rewire if necessary .
Fail safe brake magnet being used
• Check to see if fail safe brake is being used in place of power applied
brake .
Faulty control
• Replace control and see if problem is resolved .
E. Symptom: Magnets do not appear to have enough torque
Probable Cause
Solution
DIP Switch improperly set
• Check DIP switch setting per chart and reset if necessary .
Magnets incorrectly wired
• Check wiring between control and magnets and rewire if required .
Torque adjust potentiometer set too low
• Check setting of torque adjust potentiometer and set to maximum if
required .
Magnets are incorrectly sized
• Verify sizing is correct by repeating selection process .