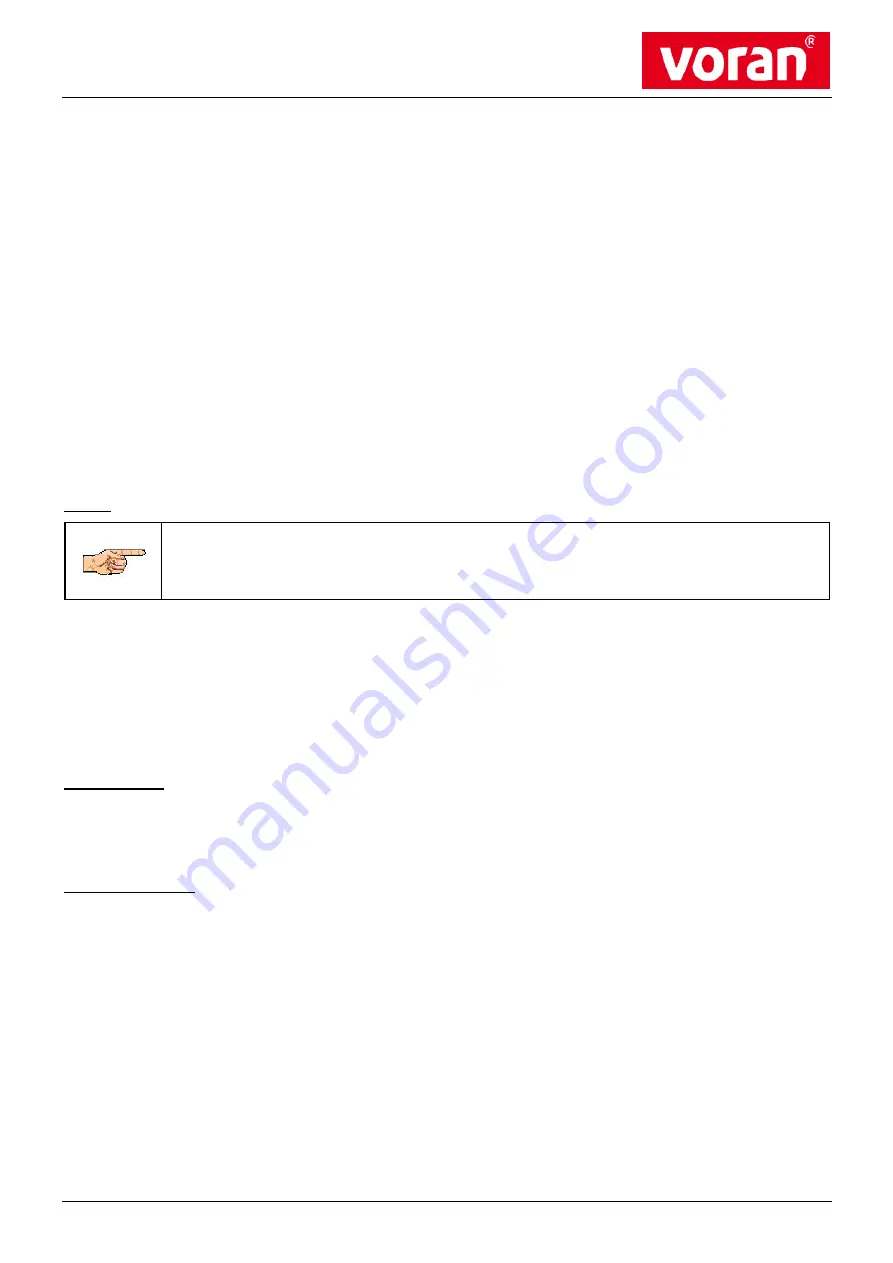
Packing Press 100 P2
Version: 111300001, M0004459B
Date: 13.12.2013
- 27 / 44 -
Electrical equipment such as for example:
- Switch and relay transmission devices such as e.g. mechanical limit switches
- current supply cables
- Any local operational control points
are in principle maintenance-free. They should, however, be checked in a monthly sequence and
– insofar
as this is required
– they should be cleaned. Damaged parts are to be replaced at once.
Any deviations from standard operation, such as:
- higher power draw
- increased noise development
- higher acceleration or delay, high oscillation amplitudes
- unusual noises or unusual smells
- unmotivated actuation of the safety devices
clearly indicate that the functionality of the machine / unit is impaired.
The occurrence of these or similar deteriorated states must at all events be reported by the operator
to the responsible superior at once.
NOTE!
The machine / unit is generally to be cleaned regularly and kept in a tidy state.
Checks must be carried out at regular intervals in order to assure a fault-free operation of the
machine/line.
Differentiation is made here between:
- Safety checks
- Functional checks
- Visual inspections
Safety checks
The applicable statutory safety regulations (both regional and
international) must be observed.
Also see the instructions contained in the secti
on “Safety regulations for operational states” .
Functional checks
The functional checks are the result of the tasks for which the device is used in accordance with
the operational cycle of the machine/line. The checks comprise the testing of the
fixtures and clamps of devices and cables as also the testing of temperatures and
noises.
Fixtures and clamps must be tightened. Should it no longer be possible to tighten the fixtures and clamps
the relevant parts must be replaced.
Defective devices must be replaced at once!
Electrical devices are often cooled with ventilators. Where these are in use their
cooling effect must be checked!