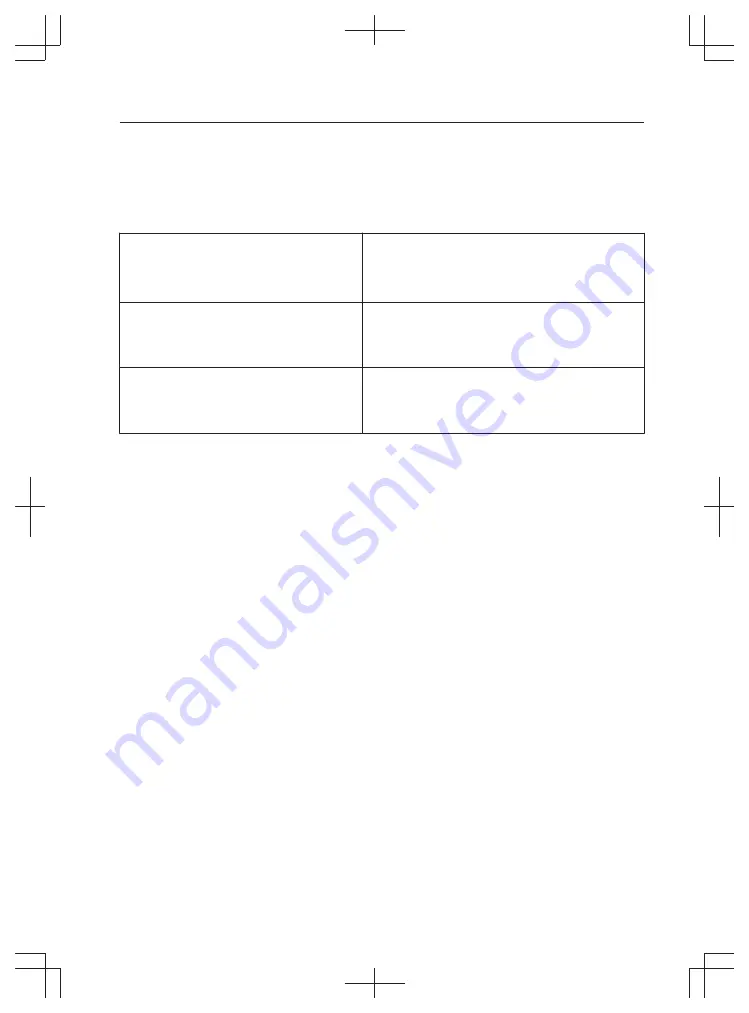
Identification numbers
Enter the identification number of machine and machine parts. This number must be
specified when contacting the manufacturer to order spare parts. Positions and
explanation of the PIN plates, see page
20
.
Manufacturer:
Volvo Construction Equipment sas
rue Pierre Pingon
BP 01303 Belley Cedex
France
PIN (Product Identification Number) of
machine:
Engine:
Foreword
Identification numbers
3
Содержание EC15E
Страница 6: ......
Страница 10: ......
Страница 69: ...Never allow any person to walk or stand under raised equipment or suspended loads Operating instructions 67 ...
Страница 152: ...11 Radiator 12 Coolant filler neck 13 Air filter 14 Battery 15 Battery quick connector 150 Maintenance ...
Страница 169: ...Fuel system bleeding The machine has a self bleeding system Maintenance Maintenance service when required 167 ...
Страница 237: ......
Страница 238: ...236 Alphabetical index Ref No 20051662 A Volvo Eskilstuna English ...