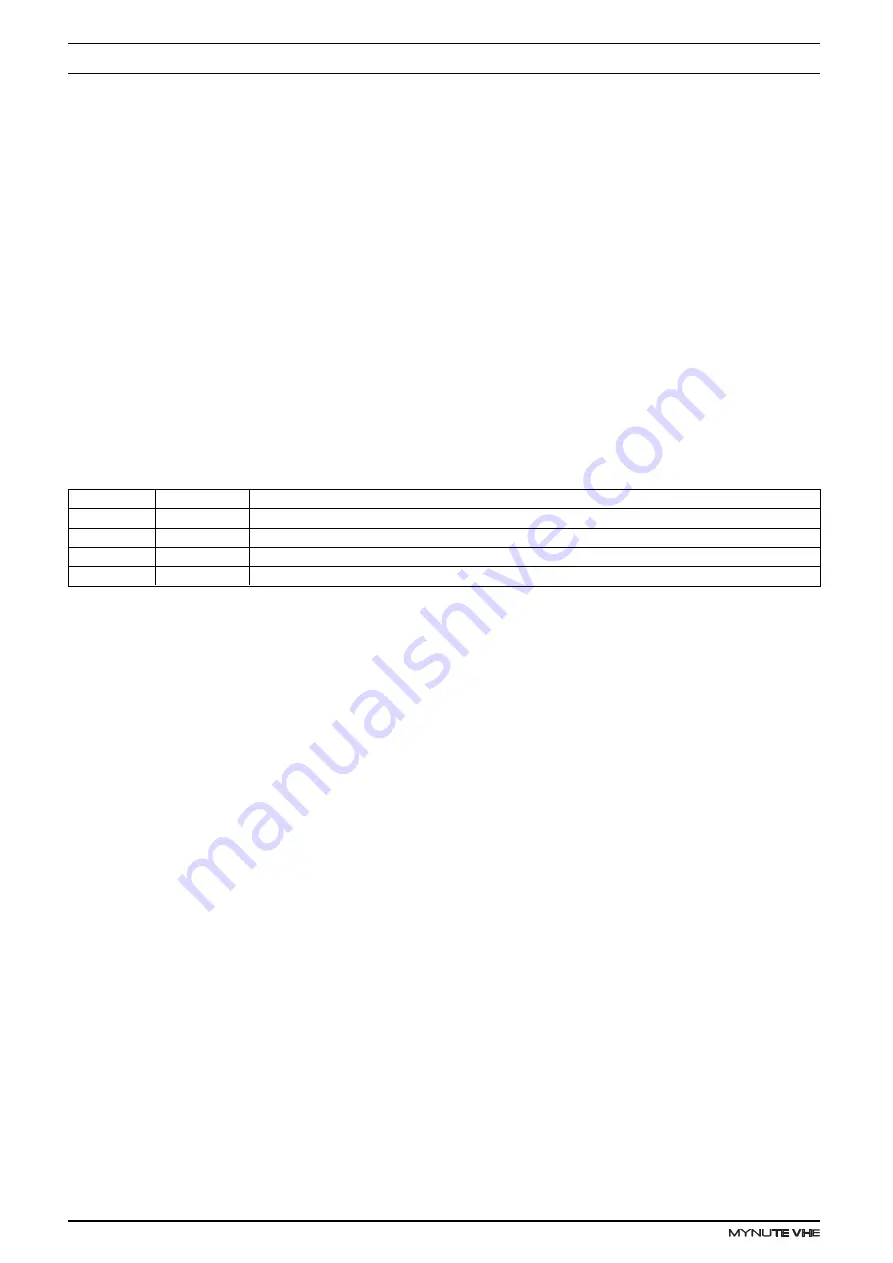
6
SECTION 3
GENERAL REQUIREMENTS (UK)
This appliance must be installed by a competent person
in accordance with the Gas Safety (Installation & Use)
Regulations.
3.1 RELATED DOCUMENTS
The installation of this boiler must be in accordance with
the relevant requirements of the Gas Safety (Installation &
Use) Regulations, the local building regulations, the current
I.E.E. wiring regulations, the bylaws of the local water
undertaking, the Building Standards (Scotland) Regulation,
and Building Standards (Northern Ireland) Regulations.
It should be in accordance also with any relevant
requirements of the local authority and the relevant
recommendations of the following British Standard Codes
of Practice.
3.2 LOCATION OF APPLIANCE
The appliance may be installed in any room or internal
space, although particular attention is drawn to the
requirements of the current I.E.E. wiring regulations, and
in Scotland, the electrical provisions of the Building
Regulations, with respect to the installation of the appliance
in a room or internal space containing a bath or shower.
When an appliance is installed in a room or internal space
containing a bath or shower, the appliance or any control
pertaining to it must not be within reach of a person using
the bath or shower.
The location chosen for the appliance must permit the
provision of a safe and satisfactory flue and termination.
The location must also permit an adequate air supply for
combustion purposes and an adequate space for servicing
and air circulation around the appliance. Where the
installation of the appliance will be in an unusual location
special procedures may be necessary, BS 6798 gives
detailed guidance on this aspect.
A compartment used to enclose the appliance must be
designed and constructed specifically for this purpose. An
existing compartment/cupboard may be utilised provided
that it is modified to suit.
Details of essential features of compartment/cupboard
design including airing cupboard installations are given in
BS 6798. This appliance is not suitable for external
installation.
3.3 GAS SUPPLY
The gas meter – as supplied by the gas supplier – must be
checked to ensure that it is of adequate size to deal with
the maximum rated input of all the appliances that it
serves. Installation pipes must be fitted in accordance with
BS 6891.
Pipe work from the meter to the appliance must be of
adequate size. Pipes of a smaller size than the appliance
gas inlet connection must not be used. The installation
must be tested for soundness in accordance with BS6891.
If the gas supply serves more than one appliance, it must
be ensured that an adequate supply is maintained to each
appliance when they are in use at the same time.
3.4 FLUE SYSTEM
The terminal should be located where the dispersal of
combustion products is not impeded and with due regard
for the damage and discoloration that may occur to building
products located nearby. The terminal must not be located
in a place where it is likely to cause a nuisance (see fig. 4).
In cold and/or humid weather, water vapour will condense
on leaving the terminal; the effect of such pluming must be
considered.
If installed less than 2m above a pavement or platform to
which people have access (including balconies or flat
roofs) the terminal must be protected by a guard of durable
material. The guard must be fitted centrally over the
terminal. Refer to BS 5440 Part 1, when the terminal is 0.5
metres (or less) below plastic guttering or 1 metre (or less)
below painted eaves.
3.5 AIR SUPPLY
The following notes are intended for general guidance only.
This appliance is a room-sealed, fan-flued boiler,
consequently it does not require a
Permanent air vent for combustion air supply.
When installed in a cupboard or compartment, ventilation
for cooling purposes is also not required.
3.6 WATER CIRCULATION
Detailed recommendations are given in BS 5449 Part 1 and
BS 6798. The following notes are for general guidance
only.
3.6.1 PIPEWORK
It is recommended that copper tubing to BS 2871 Part 1 is
used in conjunction with soldered capillary joints.
Where possible pipes should have a gradient to ensure air
is carried naturally to air release points and that water flows
naturally to drain cocks.
Except where providing useful heat, pipes should be
insulated to avoid heat loss and in particular to avoid the
possibility of freezing. Particular attention should be paid
to pipes passing through ventilated areas such as under
floors, loft space, and void areas.
3.6.2 AUTOMATIC BY-PASS
Vokera recommend that an automatic bypass is installed
to ensure the required minimum flow-rate is achieved at all
times. Additionally, the design of the system and its
controls should ensure that an adequate temperature
differential is met, and should be such that it prevents
boiler ‘cycling’.
BS 5440
BS 5440
BS 5449
BS 6798
BS 6891
PART 1
PART 2
PART 1
FLUES
FLUES & VENTILATION
FORCED CIRCULATION HOT WATER SYSTEMS
INSTALLATION OF BOILERS OF RATED INPUT NOT EXCEEDING 60kW
LOW PRESSURE INSTALLATION PIPES