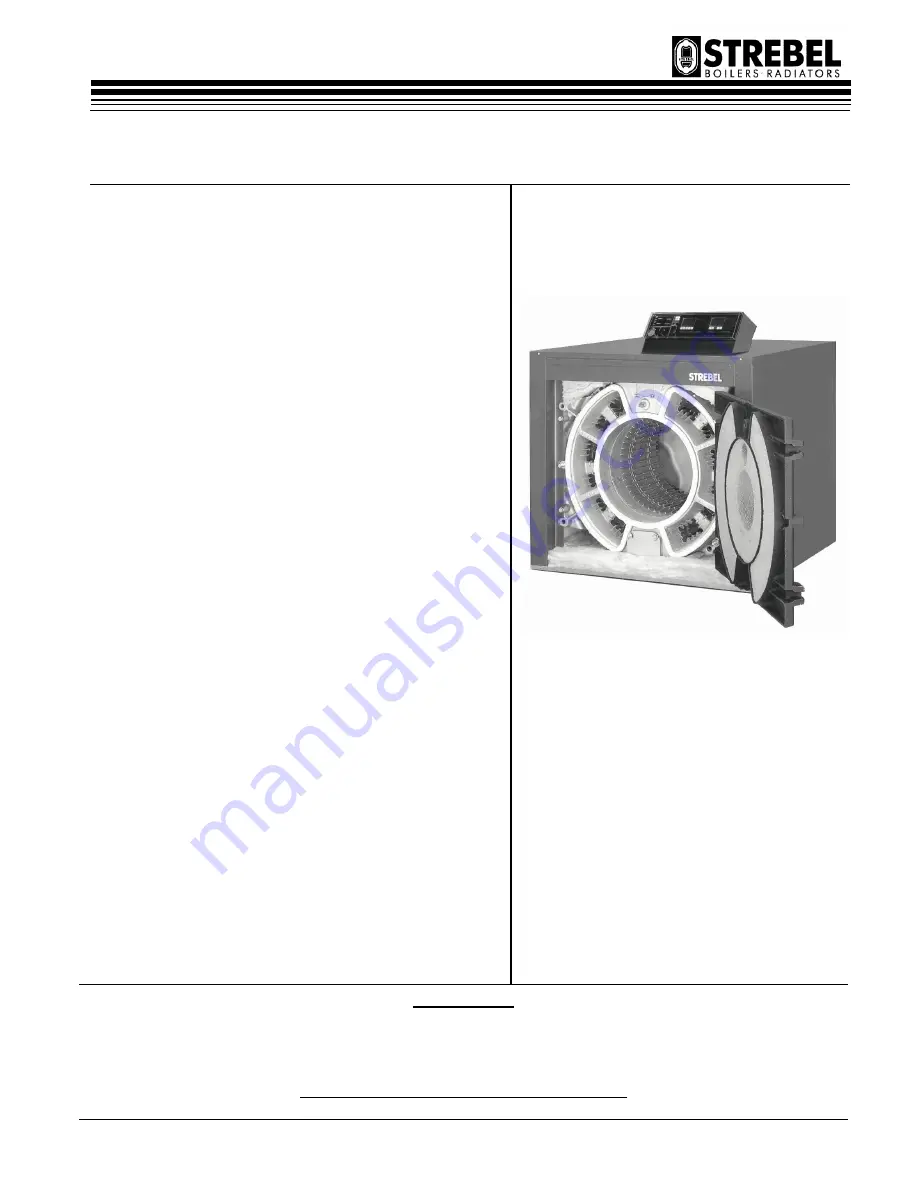
11/07/00
BOILER INSTALLATION INSTRUCTIONS FOR
RU 1S / BRU 1
RU 2S / BRU 2
RU 3S
ASSEMBLY INSTRUCTIONS
General Instructions:
The STREBEL RU boilers are special boilers for oil or gas-fired
(forced) burners. They can be fitted in hot-water heating
installations.
Operating Conditions:
Hot-water Heating installations boiler
Maximum Heat limit Temperature 110ºC / 130ºC
Operating excess pressure normal working 4 bar
Operating excess pressure multi-storey working 6 bar
Please note all relevant instructions when assembling the boilers
The Installation: The connecting and initial setting in operation
should be carried out by a qualified heating specialist.
The boiler base is to be constructed in accordance with our
diagrams.
IMPORTANT
THERE IS A STOP NUT BETWEEN THE BOILER DOOR AND THE DOOR SEAL
(TO PROTECT THE DOOR SEAL DURING TRANSIT)
THIS NUT MUST BE REMOVED ON SITE.