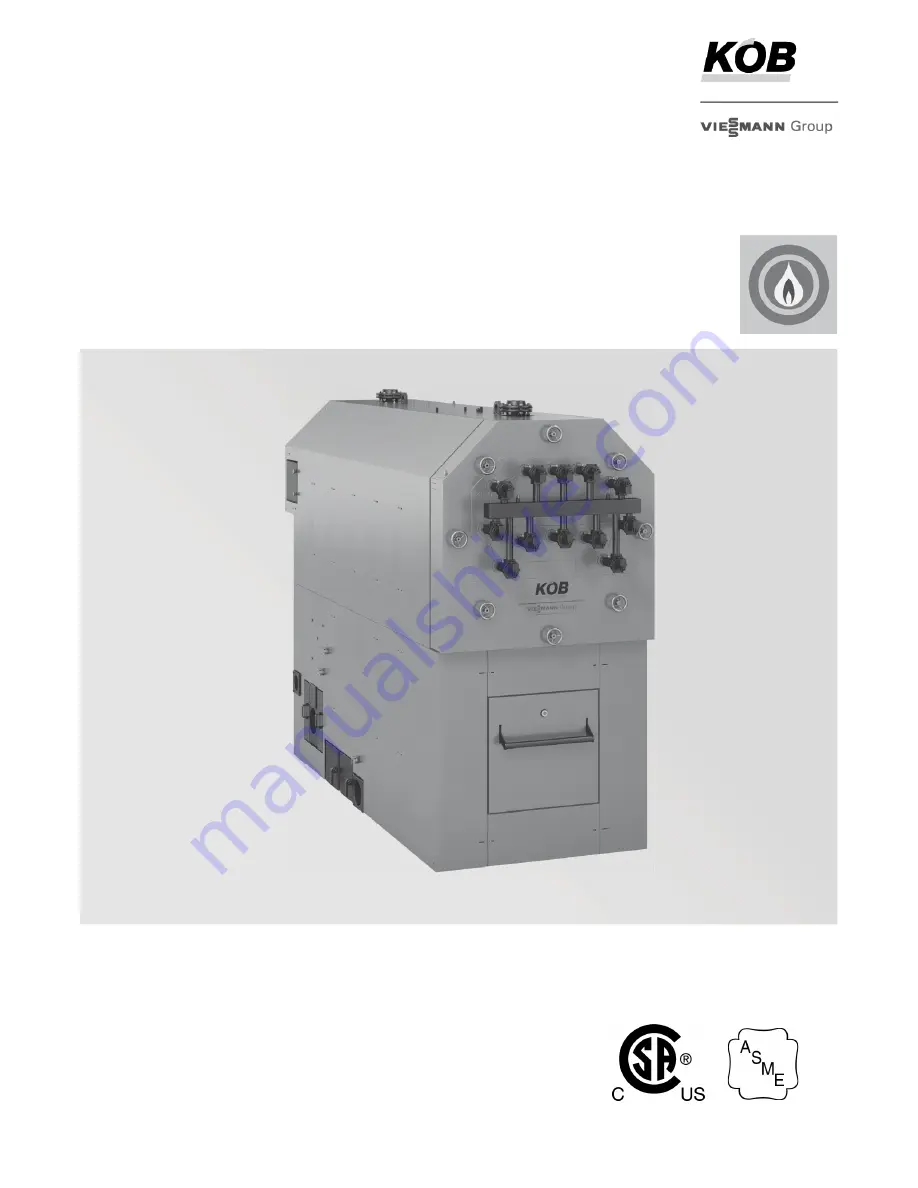
Technical Data Manual
for use by engineers and heating contractors
5443 113 v1.9 05/2013
Pyrotec
r
Wood-fired Boiler
KPT 390 to KPT 1250 Series
Pyrotec with an attached external grate and a moving
annealing grate to achieve optimal combustion results.
A feed auger continuously moves the wood fuel onto
the burner trough where gasification takes place.
The combustible gases blend with precisely controlled
secondary air, resulting in a complete combustion and
the thermal energy is released into the boiler’s triple-pass
heat exchanger.
Max. output: 390 to 1250 kW (1331 to 4266 MBH)
Min. output: 98 to 370 kW (334 to 1263 MBH)
Product may not be exactly as shown