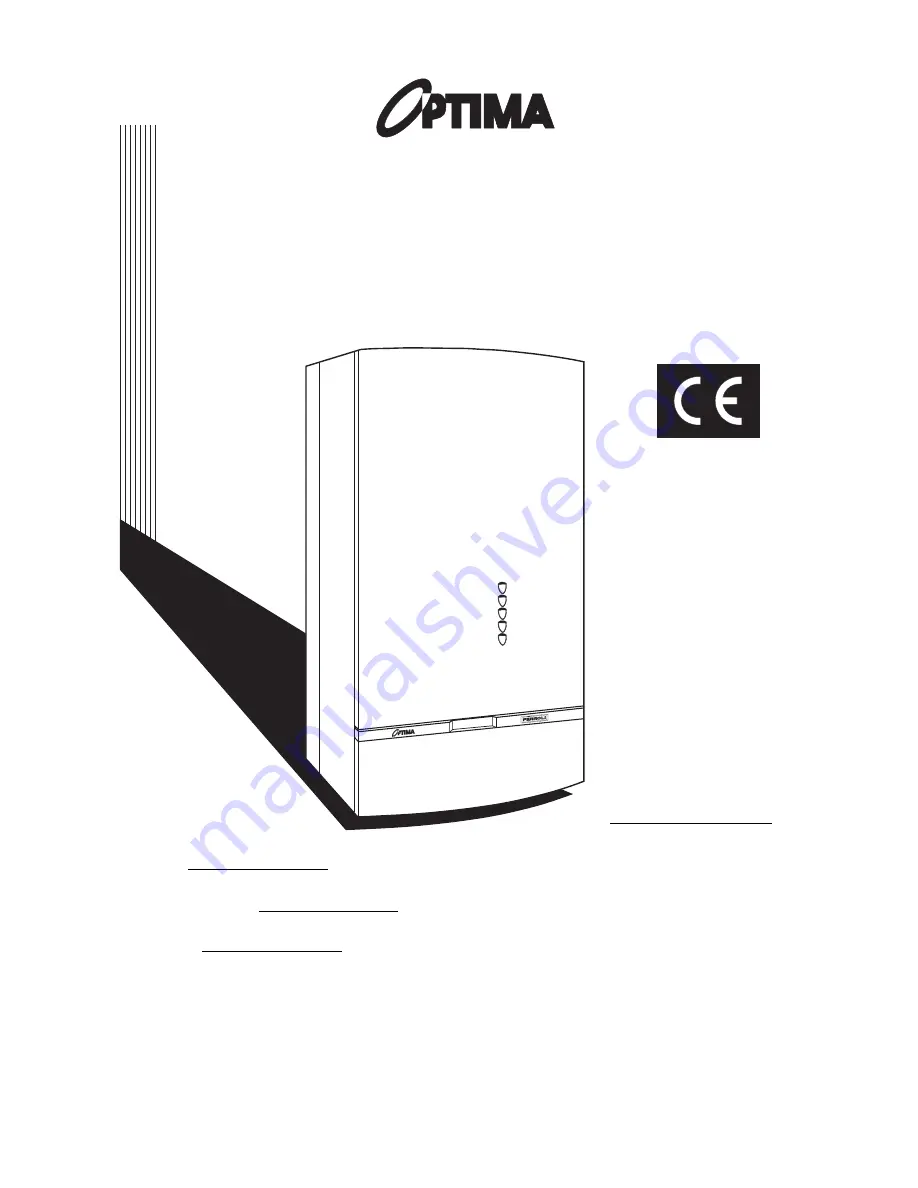
801
WALL MOUNTED, ROOM SEALED,
FAN ASSISTED, GAS COMBINATION BOILER
Stockton Close, Minworth Industrial Park, Minworth, Sutton Coldfield, West Midlands B76 8DH
Tel.: 0121/3523500 - Fax 0121/3523510
ALL SPECIFICATIONS SUBJECT TO CHANGE
Phone numbers:
Installer
Service Engineer
Serial No.
Read these Instructions thoroughly
before using the appliance
FERROLI HELPLINE
FOR SERVICE INFORMATION OR
HELP TELEPHONE: 0121 3523500
ALWAYS QUOTE YOUR SERIAL NUMBER
FOR IMMEDIATE ASSISTANCE
INSTALLATION
INSTRUCTIONS
Appr. Nr. B94.02A CE 0063AQ2150
04/98
G.C. NO: 47-267-17