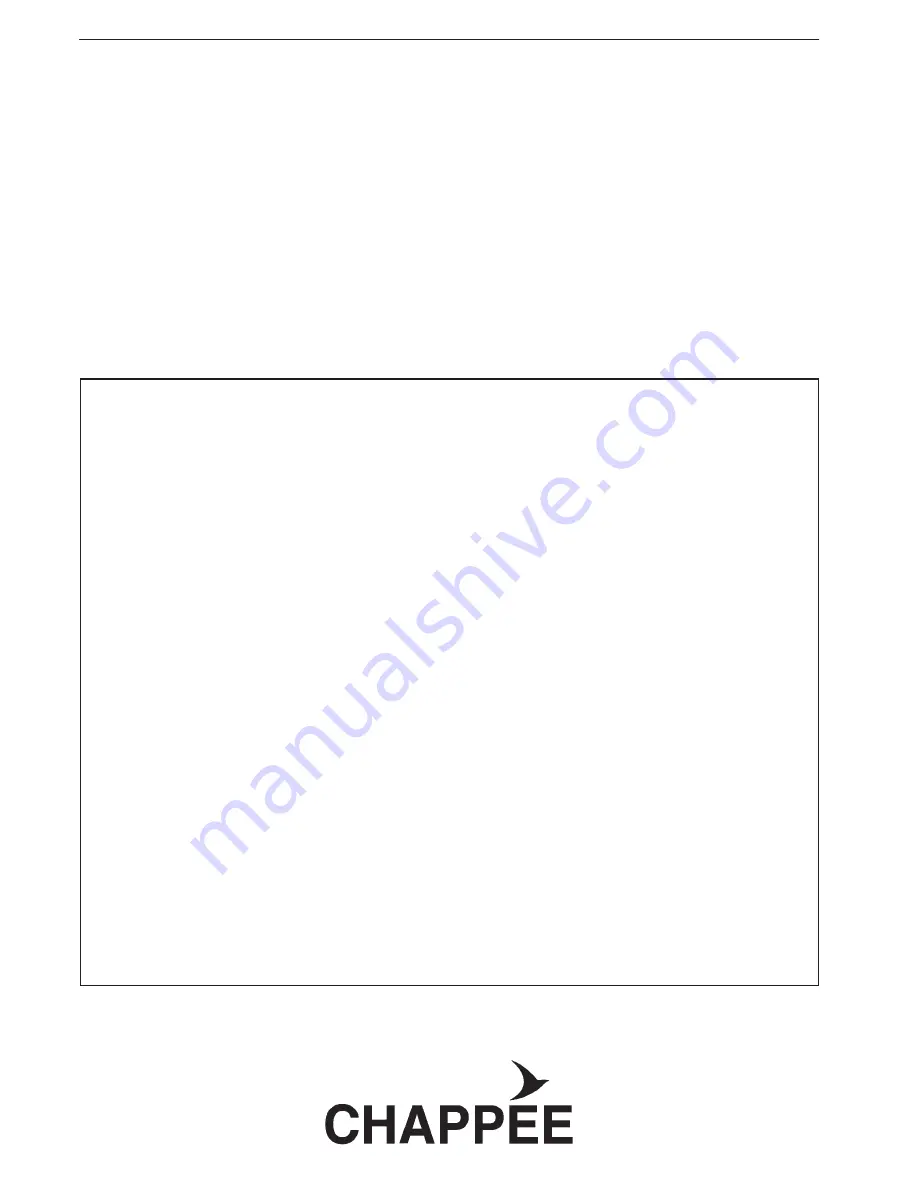
1
Ref. : CH - 1249 - A - 2
1 . Standards - Regulations
2 . General
3 . Assembly and installation
4 . Installing the options
5 . Commissioning
6 . Maintenance
HIGH-EFFICIENCY, PRESSURIZED,
CAST IRON, OIL OR GAS BOILERS
70 / 290 kW
Ref. : CH - 1249 - A - 2 - EN 07/01
I N S T A L L A T I O N M A N U A L
N X R 3
Summary of Contents for NXR3
Page 19: ...19 Ref CH 1249 A 2 ...