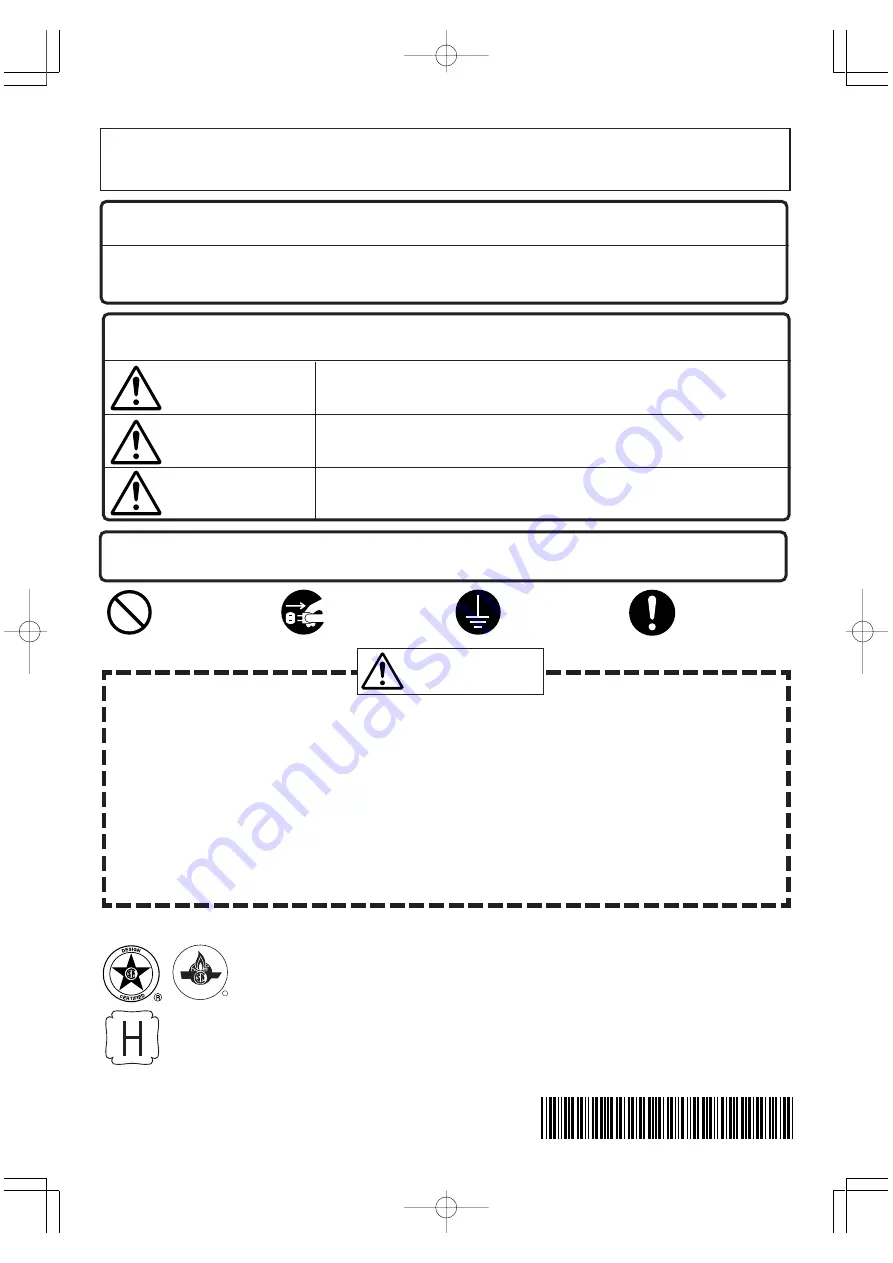
SAR8582-2
Rev. 09/07
NH-2001-DV
(Indoor Installation)
NH-1501-DV
(Indoor Installation)
GAS-FIRED DIRECT VENT BOILER
NORITZ AMERICA
CORPORATION
Potential dangers from accidents during installation and use are divided into the following three
categories. Closely observe these warnings, they are critical to your safety.
Prohibited
Disconnect
Power
Ground
Be sure to do
WARNING:
If the information in this manual is not followed exactly, a fire or explosion may result
causing property damage, personal injury or death.
DANGER indicates an imminently hazardous situation which,
if not avoided, will result in death or serious injury.
WARNING indicates a potentially hazardous situation which,
if not avoided, could result in death or serious injury.
CAUTION indicates a potentially hazardous situation which,
if not avoided, may result in minor or moderate injury.
DANGER
WARNING
CAUTION
Requests to Installers
Installation must conform with local codes, or in the absence of local codes, the
National Fuel Gas Code, ANSI Z223.1/NFPA 54- latest edition and/or CSA
B149.1, Natural Gas and Propane Installation Code (NSCNGPIC).
Where required by the authority having jurisdiction, the installation must con-
form to the Standard for Controls and Safety Devices for Automatically Fired
Boilers, ANSI/ASME CSD-1.
Noritz America reserves the right to discontinue, or change at any time, the
designs and/or specifications of its products without notice.
CAUTION
CERTIFIED
R
Low NOx
Approved by
SCAQMD
Noritz America Corporation
11160 Grace Avenue,
Fountain Valley, CA 92708
www.noritz.com
*SAR8582 C*
Installation and Instruction Manual
• In order to use the boiler safely, read this installation and instruction manual carefully, and follow
the installation instructions.
• Failures and damage caused by erroneous work or work not as instructed in this manual are not
covered by the warranty.
• Check that the installation was done properly in accordance with this installation and instruction
manual upon completion.
• After completing installation, please either place this installation and instruction manual in a
plastic pouch and attach it to the side of the boiler or hand it to the customer. Also, be sure to fill in
all of the required items on the warranty and to hand the warranty to the customer along with the
User's information manual.
Summary of Contents for NH-1501-DV
Page 31: ...31 ...