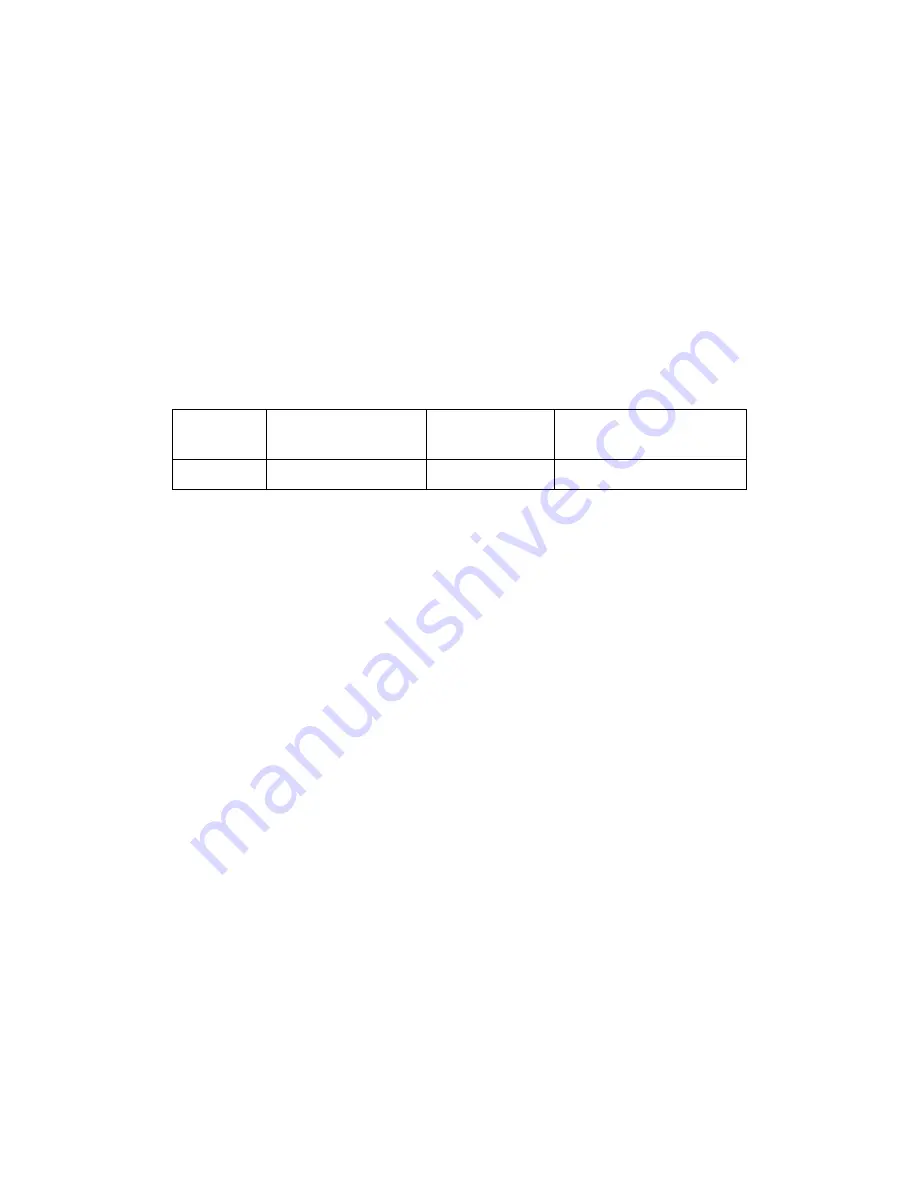
7-8
If there is a power interruption to the crankcase heater, the heater should be energized for at least two hours
before restarting the machine. This allows for evaporation of refrigerant that may have condensed in the
crankcase during the shutdown period. If the level is low after start-up, it should begin to return after a short
period of operation.
The oil level should be checked frequently, particularly during the start-up operation, to make sure a sufficient
amount of oil remains in the crankcase. While it is important to observe the oil splash during operation, the true
level can be obtained only when the compressor is stopped. With the compressor idle, the oil level should be at
a height of 1/4 to 3/4 of the sight glass but never out of sight above it.
The machine is shipped with the proper amount of oil for operating water-cooled systems. However, it may
become necessary to add some oil if new refrigerant is added to the system at a later date. Generally, air-cooled
machines will require additional refrigerant and oil to compensate for long piping runs to the condenser.
The tables below detail the type of oil required for the HFO10
’
s screw compressor. Using any other types of oil
will void the machine warranty.
Table 9: Required Compressor Lubricants and Capacity
Refrigerant Required Lubricants
Lubricant Type
Water-Cooled Oil Charge
oz (ml)
R-513A
Bitzer BSE 170
Polyol Ester Oil
305 (30)
Note:
The oil specified for this machine is very hygroscopic (it attracts and holds water molecules from the
surrounding environment) and should be protected from the atmosphere to all extents possible.
If the compressor needs more oil, use an oil pump. To add oil, remove the large refrigerant valve cap on the Oil
Drain/Fill valve in Figure 27. Backseat the valve (large stem out) to close off the 1/4-in (DN 8) side port on the
valve body. Remove the 1/4-in. (DN 8) brass seal cap to access the oil fill port on the valve body. Once the seal
cap is removed, connect a refrigerant hose to the 1/4-in. (DN 8) port and front seat the valve (large stem in) to
open the 1/4-in. (DN 8) port. Using an oil pump, add oil directly to the compressor crankcase until the oil
reaches the oil fill mark on the side of the compressor body.
After all oil is added, backseat the valve (large stem out) to close off the 1/4-in. (DN 8) side port on the valve
body, remove the refrigerant hose, and replace the 1/4-in. (DN 8) brass seal cap. Front seat the valve (large stem
in) and check for leaks at the brass seal cap. If no leaks are found, replace the large refrigerant valve cap on the
Oil Drain/Fill valve.
The Bitzer screw compressor is equipped with an opto-electronical oil level sensor, which monitors the
compressor’s oil level and
automatically stops the machine if the oil level is too low. This helps avoid damage to
the compressor.
For other compressor maintenance procedures, refer to the Bitzer service bulletin SB-170 operating manual.
Содержание Tube-Ice HFO10
Страница 2: ......
Страница 6: ......
Страница 10: ......
Страница 12: ......
Страница 16: ...2 4 Figure 3 Water Cooled Piping Schematic ...
Страница 17: ...2 5 Figure 4 Air Cooled Piping Schematic ...
Страница 36: ......
Страница 40: ......
Страница 43: ...6 3 Figure 16 Panel Layout 60 Hz Non CE Machines ...
Страница 44: ...6 4 Figure 17 Electrical Schematic Control Circuit All Voltages 50 Hz ...
Страница 45: ...6 5 Figure 18 Electrical Schematic Control Circuit All Voltages 60 Hz ...
Страница 46: ...6 6 Figure 19 Electrical Schematic 3 Phase Power All Voltages 50 Hz ...
Страница 47: ...6 7 Figure 20 Electrical Schematic 3 Phase Power All Voltages 60 Hz ...
Страница 68: ......
Страница 96: ......
Страница 110: ...Notes ...
Страница 111: ...Notes ...