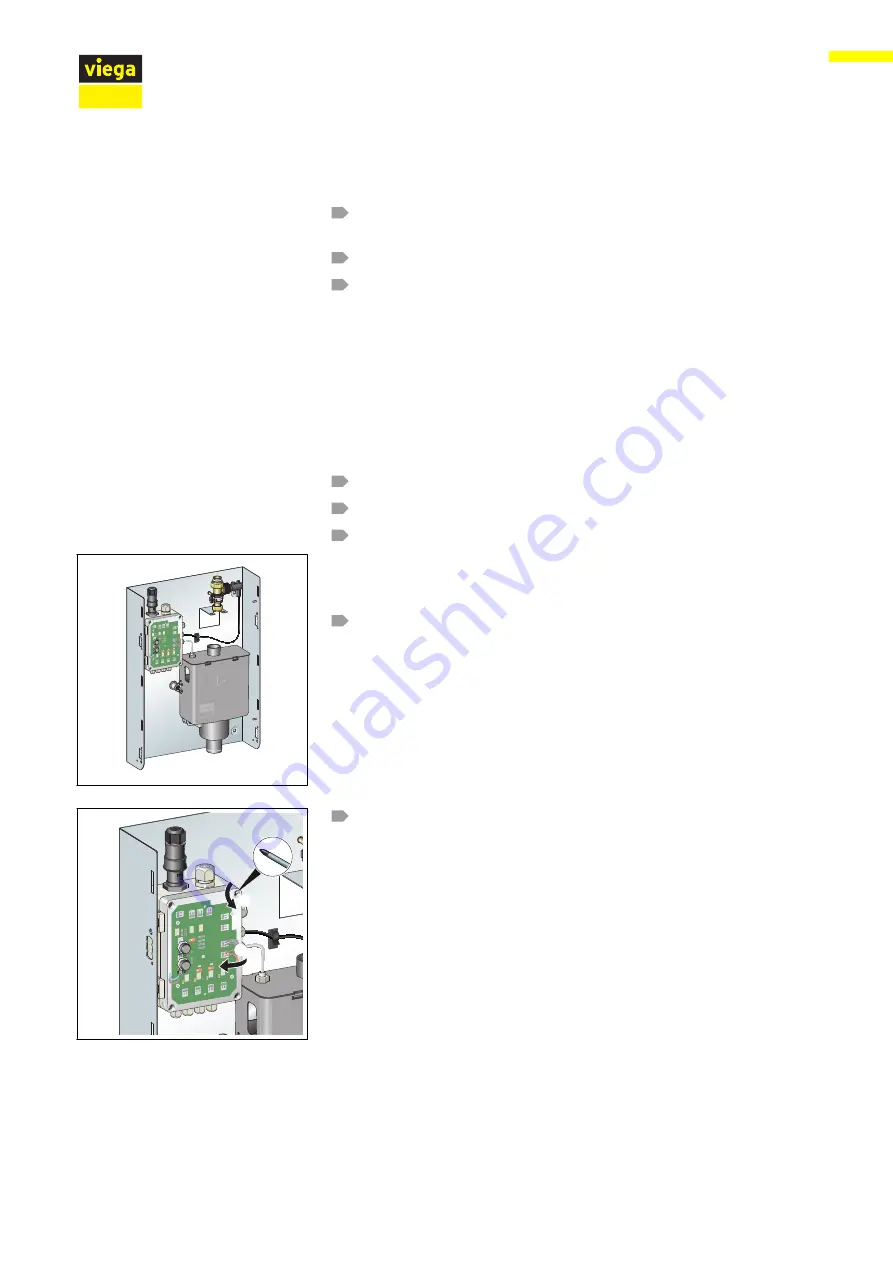
Press the Test button and keep pressed until the indication "Flow
switch" emits light (already with 1 valve).
Release the Test button.
Carry out a test flushing.
3.6.4
Repairing
In case of a malfunction, several components may require repairs. In
this case, proceed as described in the following:
Shut the water off.
De-energise the flush valve.
Disconnect the mains plug from the control.
CAUTION! Risk of burning due to hot magnetic coils! After pro-
longed water exchange, the magnet coils get hot. Do not touch
them.
Remove the magnet valve (SW 30).
Use a Phillips-tip screwdriver to remove the lid from the control.
Checking the flow switch
Replacing the floating switch
4x
45°
1.
2.
Handling
Flush valve universal
58 from 62