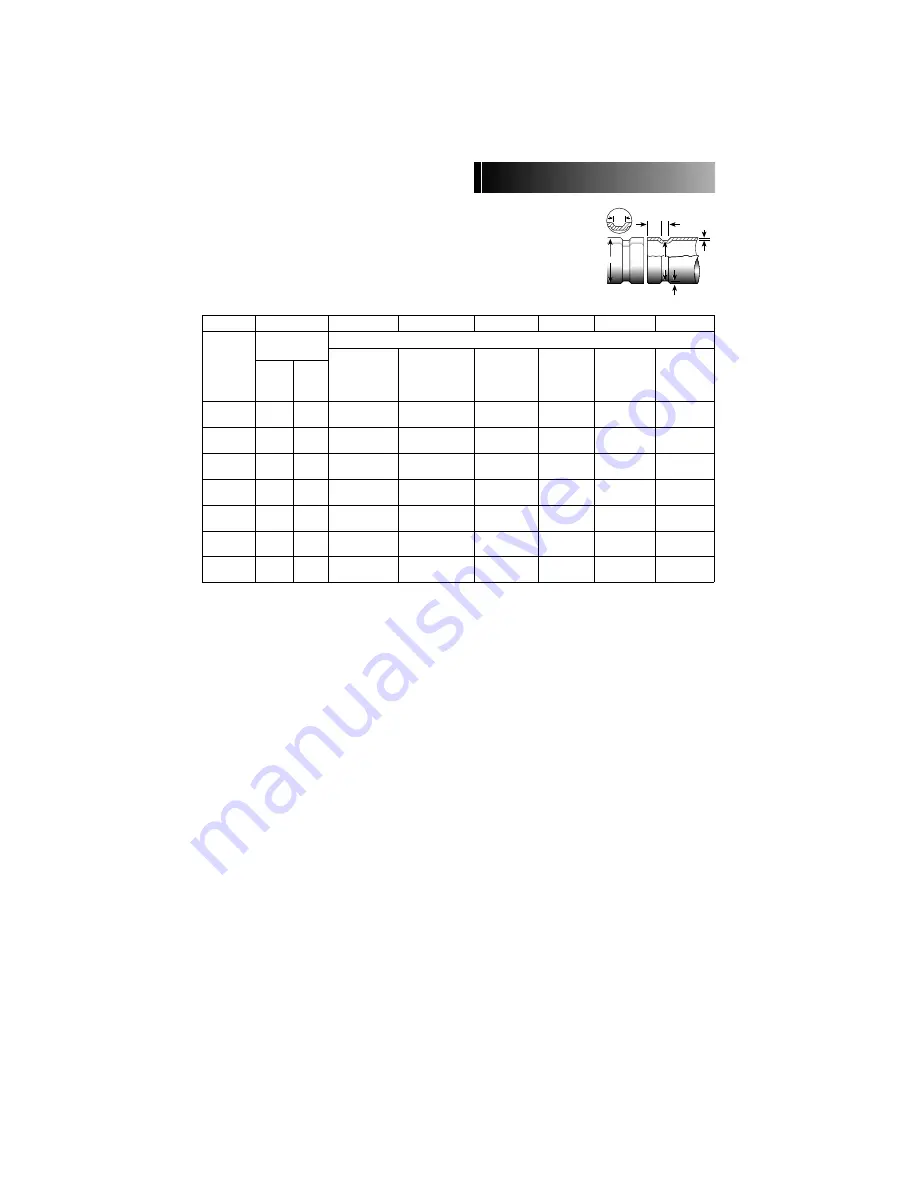
37
VE414
DRAWN COPPER TUBING
25.06-1A
1
2
3
4
5
6
7
8
SIZE
Nominal
Inches
Actual
mm
Pipe O.D.
Inches/
mm
Dimensions – Inches/
millimeters
Gasket Seat
A
±0.03/
±0.76
Groove Width
B
+0.03/-0.00
+0.76/-0.00
Groove
Diameter
C
+0.00
Groove
Depth
(ref.)
D
Min.
Allow.
Wall Thick.
T
Max.
Allow.
Flare Dia.
Basic
Tol.
2
2.125
±0.002
0.610
0.300
2.029
0.048
0.064
2.220
60.3
54.0
±0.05
15.5
7.6
51.5
1.2
1.6
56.4
2
¹⁄₂
2.625
±0.002
0.610
0.300
2.525
0.050
0.065
2.720
73.0
66.7
±0.05
15.5
7.6
64.1
1.2
1.7
69.1
3
3.125
±0.002
0.610
0.300
3.025
0.050
DWV
3.220
88.9
79.4
±0.05
15.5
7.6
76.8
1.2
81.8
4
4.125
±0.002
0.610
0.300
4.019
0.053
DWV
4.220
114.3
104.8
±0.05
15.5
7.6
102.1
1.4
107.2
5
5.125
±0.002
0.610
0.300
4.999
0.053
DWV
5.220
141.3
130.2
±0.05
15.5
7.6
127.0
1.4
132.6
6
6.125
±0.002
0.610
0.300
5.999
0.063
DWV
6.220
168.3
155.6
±0.05
15.5
7.6
152.3
1.6
158.0
8
8.125
*
0.610
0.300
7.959
0.083
DWV
8.220
219.1
206.4
*
15.5
7.6
202.2
2.1
208.8
*Tolerances for 8" (219.1 mm) are + 0.002 (0.5 mm) –0.004 (–.10 mm).
COPPER TUBING ROLL SPECIFICATIONS NOTES
COLUMN 1:
Nominal ASTM B-88 drawn copper tubing size.
COLUMN 2:
Outside diameter –
The outside diameter of roll grooved tubing shall not vary more than the tolerance listed. The
maximum allowable tolerance from square cut ends is 0.030" (0.8 mm) for 2 - 3" (60.3 - 88.9 mm); 0.045" (1.1 mm) for 4 - 6"
(114.3 - 168.3 mm), measured from true square line.
COLUMN 3:
Gasket seat –
The tubing surface shall be free from indentations, roll marks, and projections from the end of the tubing
to the groove, to provide a leak-tight seat for the gasket. All loose scale, dirt, chips and grease must be removed.
COLUMN 4:
Groove width –
Bottom of groove to be free of loose dirt, chips and scale that may interfere with proper coupling as-
sembly.
COLUMN 5:
Groove outside diameter –
The groove must be uniform depth for the entire tubing circumference. Groove must be
maintained within the “C” diameter tolerance listed.
COLUMN 6:
Groove depth –
For reference only. Groove must conform to the groove diameter “C” listed.
COLUMN 7:
ASTM B-306 –
Drain waste and vent (DWV) is minimum wall thickness copper tubing which may be roll grooved.
COLUMN 8:
Maximum allowable end flare diameter –
Measured at the most extreme tubing end dia.
A B
OD
C
B
D
T