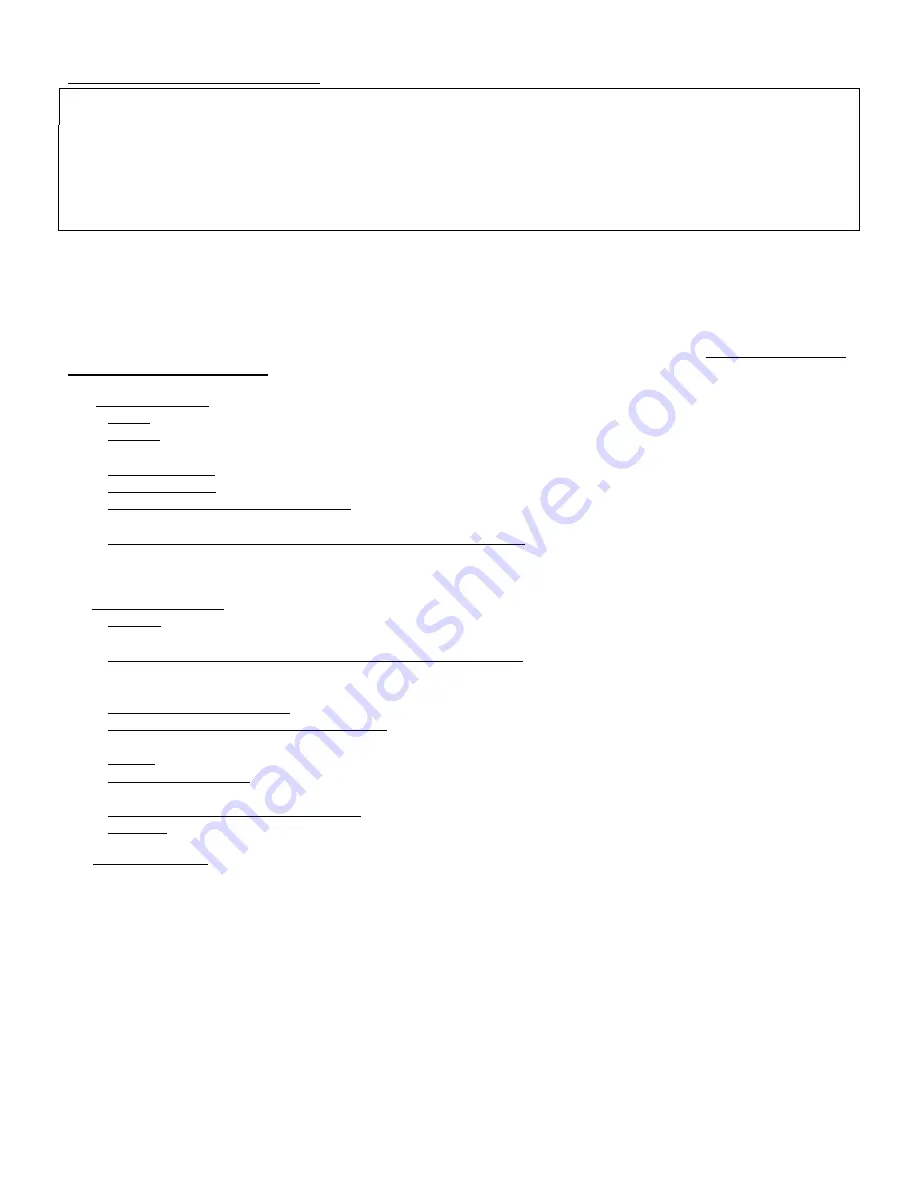
Rev. 9/25/2017
HDC-450, MANUAL
Copyright 2017 Vestil Manufacturing Corp. Page 23 of 26
Inspections & Maintenance:
Regular maintenance is required to keep this product in normal condition.
o
Relieve hydraulic pressure whenever the unit is not in use by fully lowering the pivot arm.
o
Keep the product clean & dry. Lubricate moving parts at least once per month.
o
If repairs are necessary, only install manufacturer-approved replacement parts. Vestil is not responsible for
problems or malfunctions that result from the use of unapproved replacement parts.
o
ONLY use ISO AW-32 hydraulic fluid or its equal in the hydraulic system.
Do not use brake fluid or jack oils in the
hydraulic system. If oil is needed, use an anti-wear hydraulic oil with a viscosity grade of 150 SUS at 100°F, (ISO
32 cSt @ 40°C), or Dexron transmission fluid.
Before using the unit for the first time, make a written record of its appearance. Include observations about each
component. Include details about the appearance and function of the saddle, drum retainer, chain clamp, and gear
train mechanisms. How much effort is required to turn the saddle handle (HDC-450-60) or to pull the gear chain (all
other models)? Raise and lower the pivot arm. Include observations about how the unit sounds as the arm rises and
descends. Make note of how much effort is required to move the pump pedal (standard models) or how quickly the
unit responds to pushbutton signals (electric powered models). This record establishes “normal condition”. During
future inspections, compare the unit to the written record to determine if it is in normal condition. DO NOT use the unit
unless it is in normal condition.
(A) Before Each Use--Inspect the following:
1. Wiring: inspect the electrical wiring for cuts and frays.
2. Casters: examine each caster. Casters should be solidly fastened to the frame. Look for areas of severe wear
and damage. Each caster should roll smoothly and without wobbling.
3. Hydraulic hoses: check for pinches, punctures, and loose connections.
4. Frame elements: inspect the legs, vertical members, and braces for cracked welds, bends, etc.
5. Saddle, drum retainer, and pivot arm: visually examine each element for damage. Pay particular attention to
pivot points: 1) pivot arm connection to frame; 2) saddle and retainer connections to pivot arm.
6. Handheld pushbutton controller and modular power unit (MPU): inspect the controller and look for damage that
exposes internal components. Make sure that the cover of the MPU is not punctured or in other ways noticeably
damaged.
(B) Monthly Inspections--at least once per month check the following:
1. Oil level: oil should be 1" to
1-1/2"
below the top of the tank with the arm in the lowered position. Add oil as
necessary. Look for oil leaks from hoses, the cylinder, and the reservoir.
2. MPU, hand control, and battery (electric powered models only): Remove the cover of the MPU and visually
inspect the components. Check the water level in the battery
.
Check for worn or damaged hydraulic hoses,
electrical wires, and cords. Repair as necessary.
3. Clevis pins and pivot points: inspect for excessive wear.
4. Cylinder, foot pump or modular power unit: confirm that the cylinder extends and retracts smoothly. The cylinder
should not be bent, cracked, etc. Only normal effort should be required to work the foot pump.
5. Chains: inspect chain links for elongations, breaks, twists, etc.
6. Saddle and pivot arm: observe the arm as it cycles up and down. Make note of unusual noise and motion (e.g.
binding). Rotate the saddle in both directions while watching and listening for unusual behaviors.
7. Labels (see “Labeling diagram”; p. 25): confirm that all labels are in place and are in good, readable condition.
8. Surfaces: wash the unit to remove dirt and debris
.
(C) Yearly Inspection
Hydraulic oil should be changed at least once a year or sooner if the oil darkens or becomes gritty. Oil should also
be changed if it has a milky appearance, which indicates that water is present.
If oil is needed,
use HO150 hydraulic
fluid. Any anti-wear hydraulic fluid with a viscosity grade of 150 SUS at 100° F (ISO 32 @ 40° C) such as AW 32 or
Dexron transmission fluid is acceptable.
Flush the reservoir with new oil before refilling it.