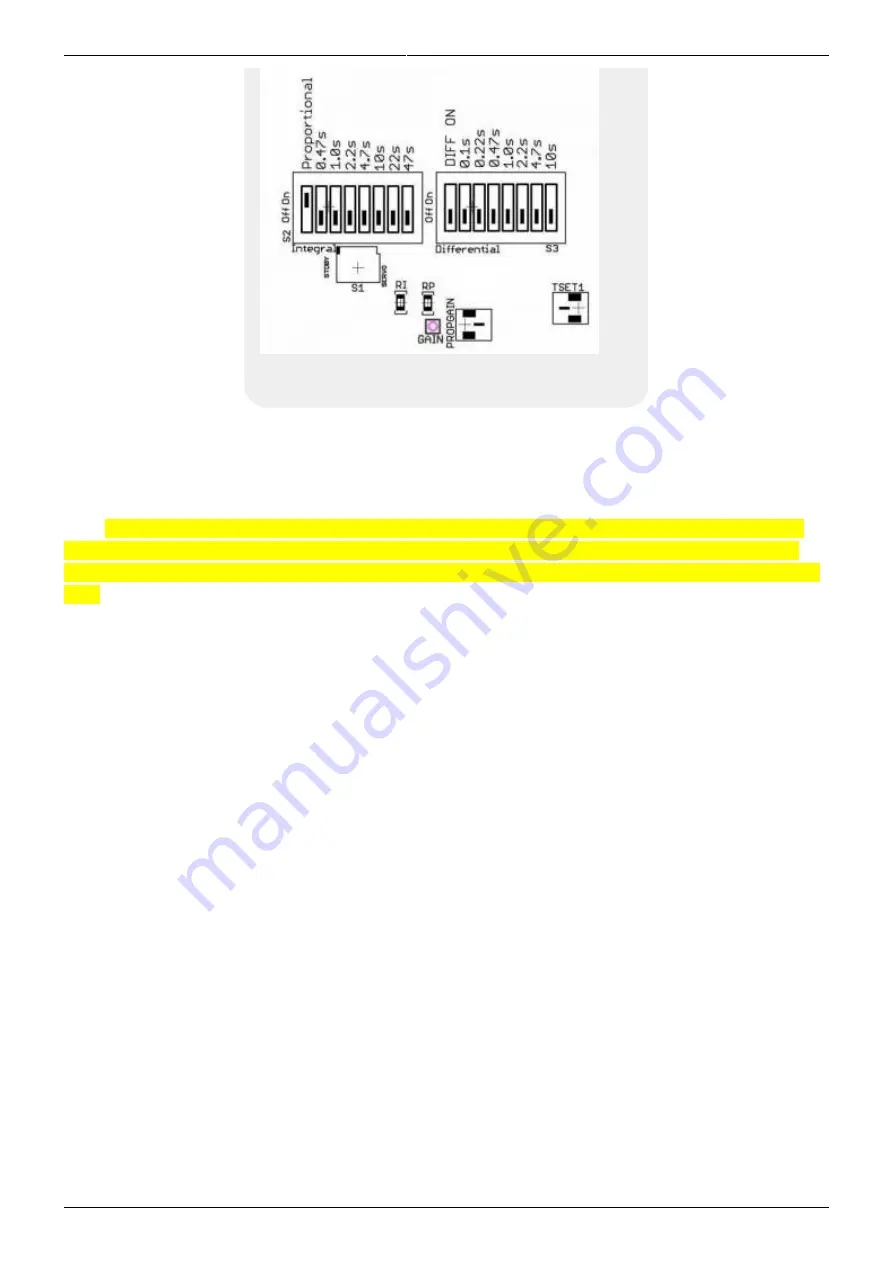
2021/12/18 07:41
17/19
Laser Controller
Product Manuals - https://www.vescent.com/manuals/
Fig.
6: Side Panel Adjustment of Poles for D2-105
User Control of the Poles and Gain
If you remove the right side panel on the Laser Controller, for each stage of temperature control, you
will see the panel shown in
. The set of click switches labeled “Integral” controls the PI (ω
1
)
pole. Clicking the first switch, labeled “proportional,” into the on position removes the integral gain
(but not the differential gain). If the “proportional” switch is in the off position (integral gain is now
on), then the sum of the times for all switches in the on position gives the RC time-constant for the PI
pole. For example, if the 2
nd
(0.47s) switch and the 4
th
(2.2s) switch are in the on position (and the rest
off), then the time constant is 2.7s and ω
1
= 1/2.7s = 0.37 Hz.
Similarly, the switches labeled “Differential” control the D (ω
2
) pole. If the first switch, labeled “Diff
On” is in the off position, then there is no differential pole. If the “Diff On” switch is on, then the D
pole has an RC time-constant given by the sum of the times of all the switches in the on position,
same as with the Integral bank of switches.
The “PROPGAIN” trimpot tunes the overall gain of the system and is adjustable by a factor of 200.
Additionally, the TSET1 trimpot is used to adjust the set-point temperature for stage 1 (stage 2 is
controlled on the front panel).
The “STBY / SERVO” switch can disable temperature controller for either stage by placing the switch
into STBY (standby) mode. In this mode, a red light will be shown on the front-panel to show that the
stage has been disabled.
Tuning the Thermal Loop
Although there are numerous methods for tuning the loop parameters, these instructions will use the
Ziegler-Nichols tuning method.
For nested stages (one stage is inside a housing whose temperature is controlled by another stage),
we recommend tuning the outside stage first with the inside stage turned off. Then tune the inside
stage while the outside stage is turned on. For the stage directly controlling the laser temperature, we
recommend running the tuning procedure while the laser is on. For each stage, follow the steps below
to tune the plants according to the Ziegler-Nichols tuning method:
Connect thermal load to Laser Controller.
1.