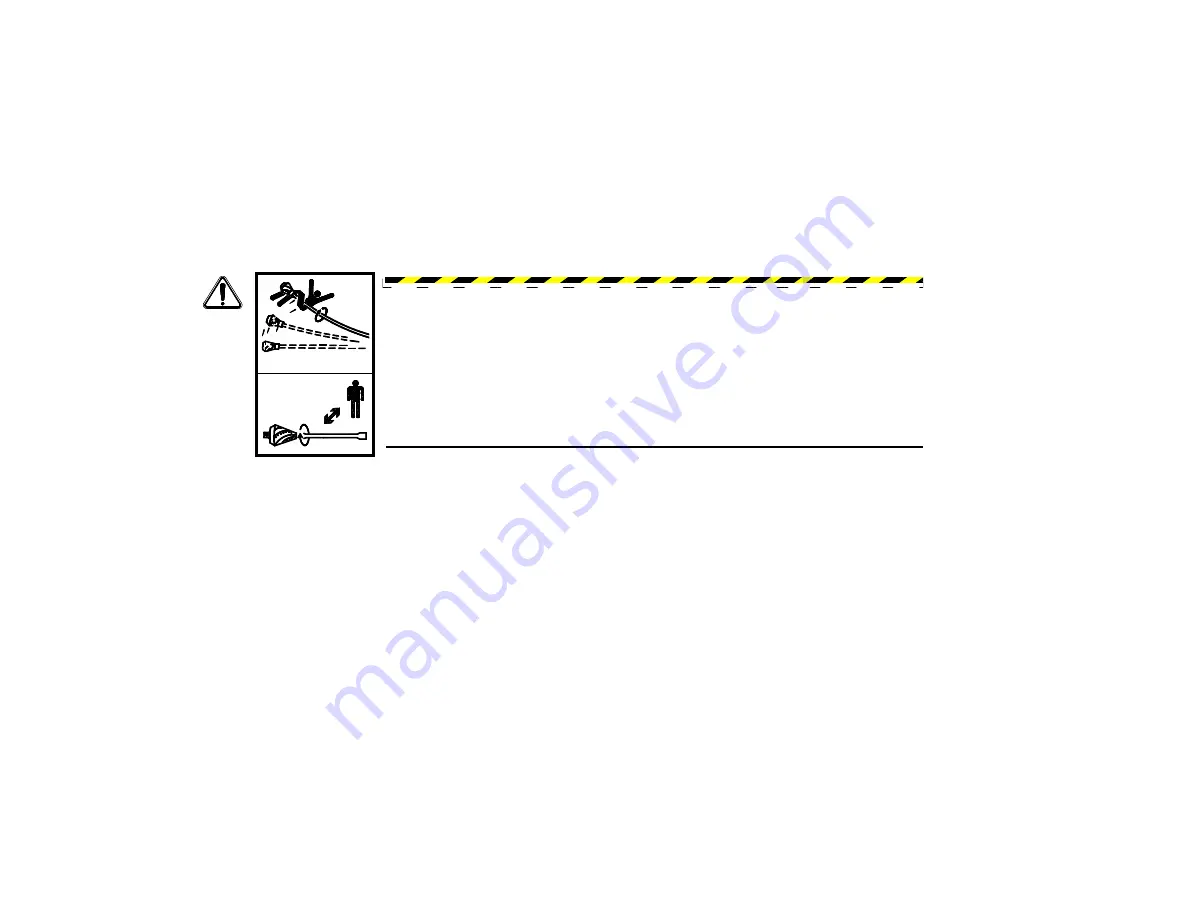
D20x22 Series II Navigator HDD
Operation 50-31
P
ULLBACK
- S
TART
Step 1:
Turn on drilling fluid.
To prevent reamer from moving sideways, pull tooling up to exit hole before rotating.
Each rotation of the drill rod can cause an 8˝ (20 cm) diameter reamer to rapidly travel 2 ft (60 cm) and a 16˝ (41
cm) reamer to travel 4 ft (1.2 m).
Step 2:
Rotate clockwise and retract the drill rods from the ground.
Step 3:
Stop rotation.
Step 4:
Clamp front vise, clamp rear vise, and rotate rear vise to break rod joint.
DANGER:
Drill string and tooling can rapidly move sideways along the ground at
the exit location if rotation is started when drill rod or tooling is on the ground, away
from the exit hole. The larger the diameter of the reamer and the more drill string
exposed the faster and farther the reamer and drill string can travel. Death or
serious injury will occur if anyone is entangled or struck by drill string or tooling.
Pull tooling up to exit hole before rotating. Everyone must be well away from exposed
drill string and tooling before rotation is started.
Содержание D20x22 Series II
Страница 14: ...This page intentionally left blank ...
Страница 28: ...This page intentionally left blank ...
Страница 84: ...This page intentionally left blank ...
Страница 218: ...This page intentionally left blank ...
Страница 224: ...This page intentionally left blank ...