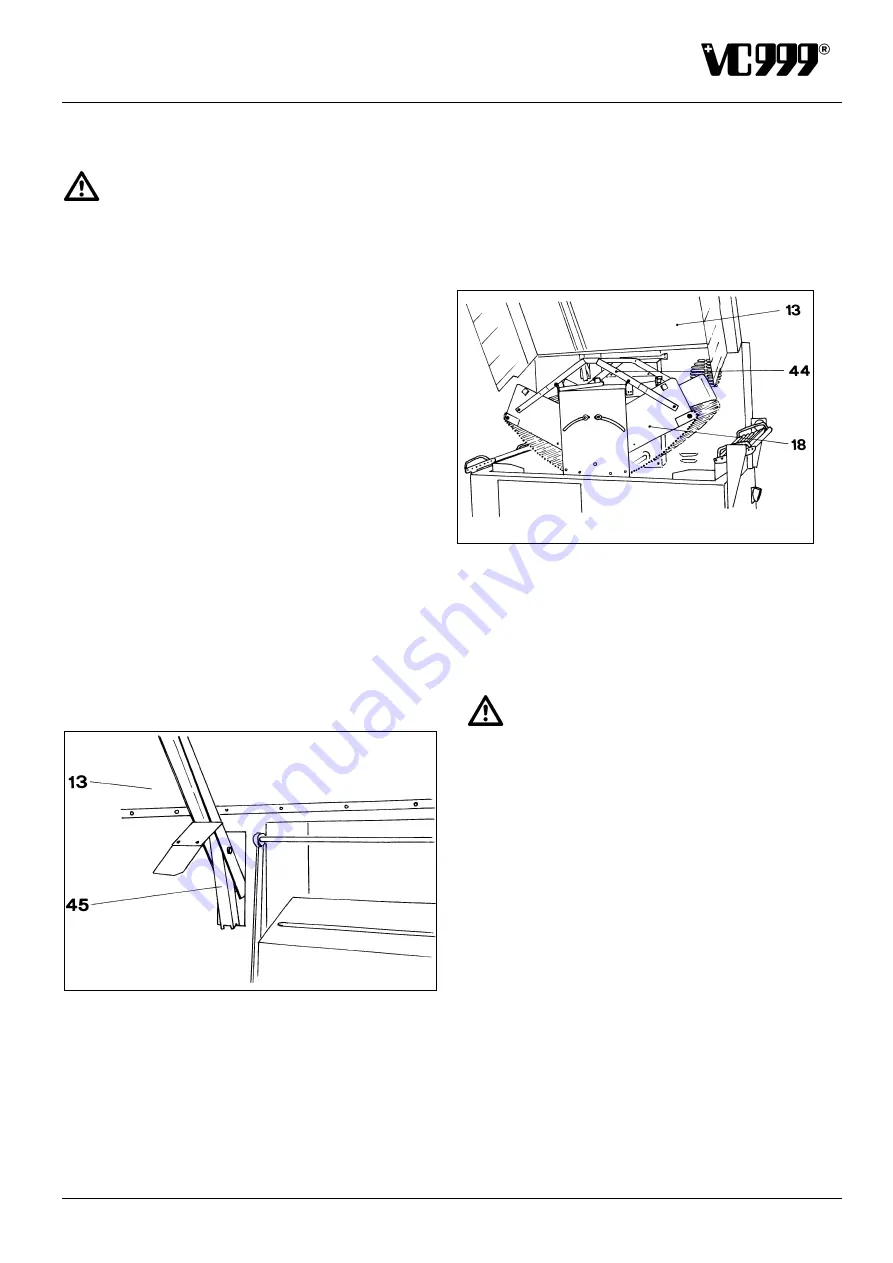
Shrink Tank VC999 85.47i
Page 28/34
Art. no. 512.320
2009-11-17
13. Maintenance
WARNING
Before cleaning or service work switch off the
machine with the
OFF
key (3) and the main switch
(16).
Waste disposal
In choosing cleaning materials have regard to
environmental factors, health risks, waste disposal
regulations and their local application.
•
Note manufacturer’s instruction
13.1 Cleaning
13.1.1 Cleaning Materials
Use commercial neutral cleaners (non-abrasive) which
meet hygiene requirements.
Use commercial stainless steel cleaners for outer
surfaces of the machine.
13.1.2 Cleaning Schedules
Daily
•
Open steam hood (13) till catch (45) engages and
inspect immersion platform (18) for bag- or product
residues. Remove any such residue found. Close
hood (13) by raising the hood (13) and pressing the
catch (45).
Fig. 8
•
Clean outside of machine.
Keep workplace around machine clean and tidy.
Weekly
•
Clean or remove lime deposits from inside of tank
−
Switch off machine with
OFF
key (3).
−
Empty tank through drain (6).
−
Open steam hood (13) till catch (45) engages.
−
Swing immersion platform (18) into the cleaning
position using the shackle (44) and engage
shackle.
Fig. 9
−
Remove wrapper residues
−
Lower immersion platform (18) into the working
position.
−
Add about 3.5 measures of decalcifier (obtainable
from the VC999 Customer Service) to the water.
WARNING
Risk of injuries! Decalcifier contains citric acid
(toxicity class 4 BAG T No. 37.282). Do not swallow,
avoid contact with eyes.
−
Close steam hood (13).
−
Activate the decalcifying program in the ABC level of
the control (see chapter 11.2.5).
•
Autom. water filling
•
Set water temperature 80°C
•
Dwell time 10 sec
−
Activate the heating.
−
Use the
START
button to activate the program once
the set water temperature has been reached.
−
Run about 20 immersions and stop with the
STOP
button.
−
Empty tank again and rinse with fresh water.
−
Check visually that all parts (tank, immersion
platform, heating elements, temperature sensors
etc.) are free from lime residues. If necessary repeat
decalcifying treatment.
−
The Shrink Tank is now ready for use.
Содержание 85.47i D
Страница 4: ......
Страница 21: ...Shrink Tank VC999 85 47i 2009 11 17 Art no 512 320 Page 21 34 Flow chart for program Level...
Страница 23: ...Shrink Tank VC999 85 47i 2009 11 17 Art no 512 320 Page 23 34 Decalcifying program...
Страница 24: ...Shrink Tank VC999 85 47i Page 24 34 Art no 512 320 2009 11 17 Flow chart ABC level...
Страница 32: ...Shrink Tank VC999 85 47i Page 32 34 Art no 512 320 2009 11 17 16 Pneumatics diagram...
Страница 33: ...Shrink Tank VC999 85 47i 2009 11 17 Art no 512 320 Page 33 34 17 Circuit diagrams...
Страница 34: ...Shrink Tank VC999 85 47i Page 34 34 Art no 512 320 2009 11 17...