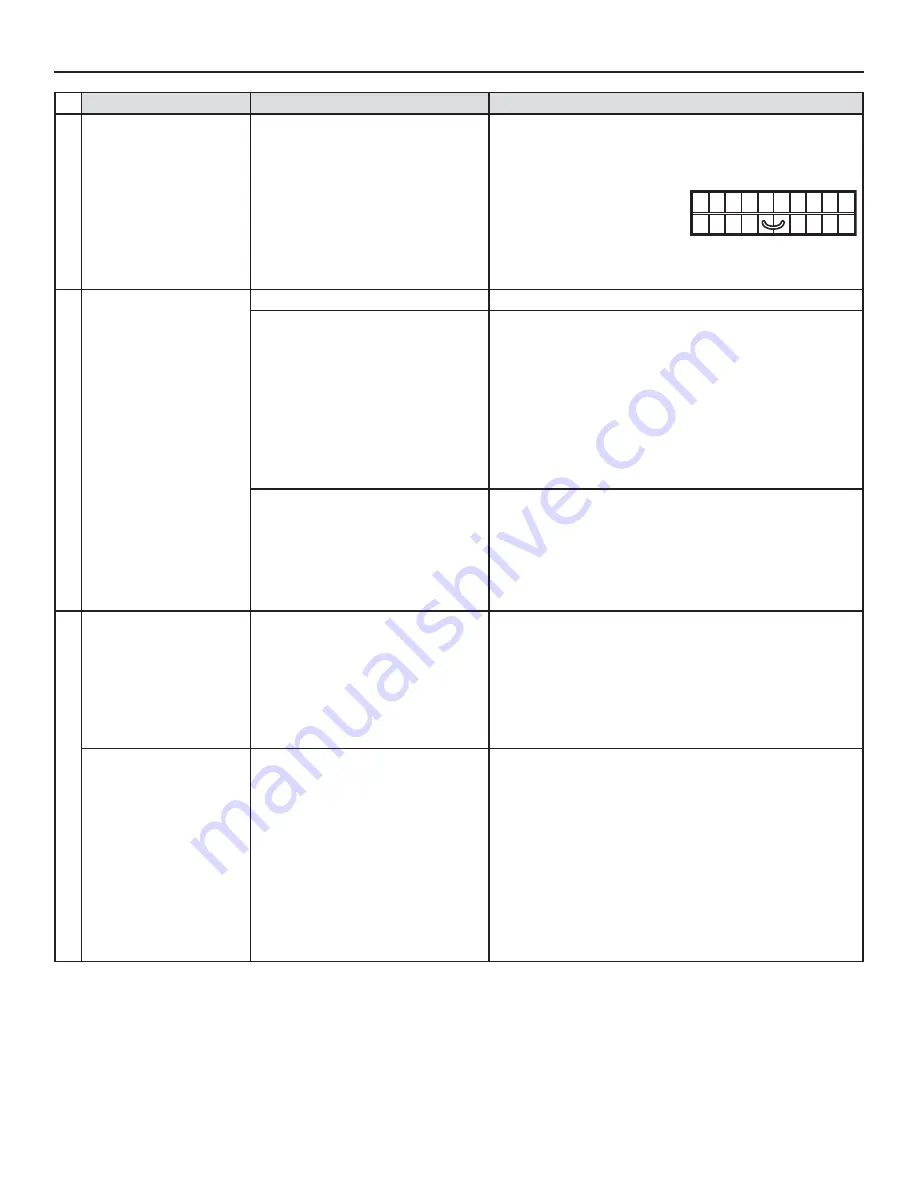
18
8. TROUBLESHOOTING (
CONT
'
D
)
P
ROBLEMS
P
OSSIBLE
CAUSES
Y
OU
SOULD
TRY
THIS
6
The Dehumidistat
OR other auxiliary control
does not work.
• The wires may be in reverse postion.
• The wires may be misconnected.
• The wires may be broken.
• The Dehumidistat or push button may be
defective.
• Ensure that the color coded wires have been connected to their
appropriate places.
• Ensure the wires are correctly connected.
• Inspect every wire and replace any that is damaged. If wires are
hidden into walls, test the control using a shorter wire.
7
The damper system
does not work
(
AMBER error code
).
At power up, no RED LED
.
• See point 5.
At power up, LED lights RED and
there is a clicking sound coming from
electrical compartment, but damper
does not move
:
• Ice or other things hindering the damper
movement.
• J12 unconnected or bad contact.
• Wrong connection of J8.
• The transformer may be defective
(no 24 VAC between J8-1 and J8-2).
• The damper actuator may be defective.
• Remove ice or hindering elements.
• Check J12 connection (both harness side and board side).
• Check J8 connection.
• With unit powered and J9 connected, check if there is about
20-24 VAC between transformer connector J8-1 and J8-2
(ORANGE wires). If no, change the transformer.
• Replace the damper system (entire port assembly).
Damper moves but does not stop when
supposed to
:
• Damper motor turns on reverse side.
• Bad connection of J12 connector.
• Damper PCB defective or damper motor
stripped gear.
• The main PCB is defective.
• Facing the damper motor shaft, the motor should turn
counterclockwise. If not, replace the damper system.
• Check J12 connection (both harness side and board side).
• Replace the damper system.
• Replace the main PCB.
8
A. The supply motor does not
work, but exhaust motor
works.
• The supply motor may be defective.
• The supply motor capacitor or the PCB
may be defective.
• Plug supply motor to J5 connector and exhaust motor to J4
connector. If the integrated control LED flashes RED, the supply
motor is defective. If exhaust motor works, plug back supply motor
to J4 connector and exhaust motor to J5 connector, then check for
supply motor capacitor validity.
• Plug supply motor capacitor to J7 connector and exhaust motor
capacitor to J6 connector. If the integrated control LED flashes
RED, the supply motor capacitor is defective. If there is no change,
the PCB is defective.
B. The integrated control LED
flashes RED.
• The exhaust motor may be defective.
• The exhaust motor capacitor may be
defective.
• Tranformer wire(s) bad connection.
• The transformer or the PCB may be
defective.
• Plug exhaust motor to J4 connector and supply motor to J5
connector. If supply motor works but exhaust motor does not,
exhaust motor is defective. If exhaust motor works, plug back
supply motor to J4 connector and exhaust motor to J5 connector,
then check for exhaust motor capacitor validity.
• Plug exhaust motor capacitor to J6 connector and exhaust motor
capacitor to J7 connector. If exhaust motor works but supply motor
does not, the exhaust motor capacitor is defective. If there is no
change, check validity of transformer or PCB.
• Check J8 and J9 connectors, as well as BLUE and RED wire
connections from J9.
• Move JU1 jumper from pins 2 and 1 to pins 2 and 3. Set the unit on
high speed. If exhaust motor works, the transformer is defective. If
it still does not, change the PCB..
• Jump the
OL
and
OC
terminals.
If the unit switch to high speed,
remove the Dehumidistat or push
button and test it right beside the
unit using another shorter wire. If
it works here, change the wire. If it doesn’t, change the Dehumidistat
or the push button.
NO C NC I OC OL Y R G B
VE0098