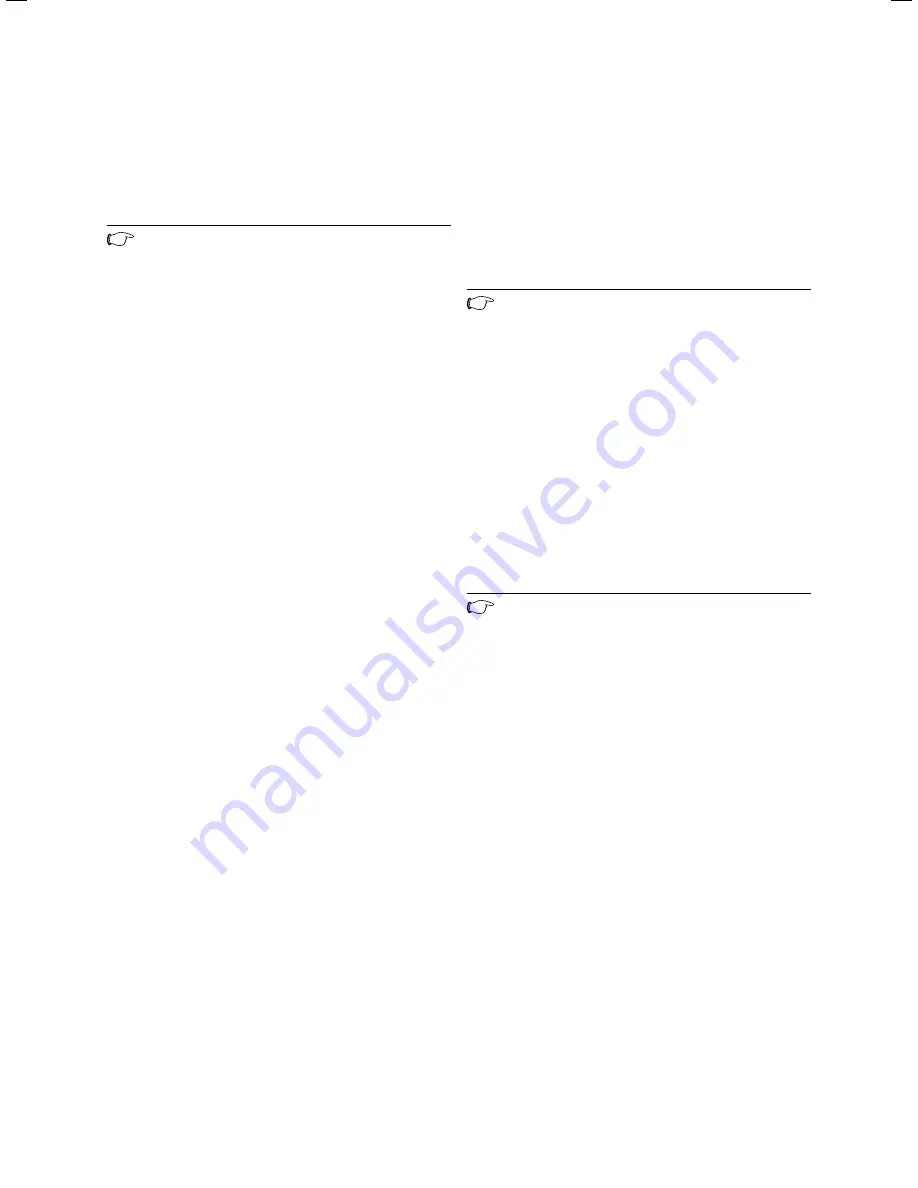
29
Instructions for installation and servicing ecoTEC
4.14.5 Connection details for external time switches
and boiler terminal strip
Fig. 4.19 shows the connection details where a time
switch is used without a room thermostat to control the
boiler.
Note
The numbers with arrows indicate connection to
the relevant terminal in the boiler terminal
strip.
If a room thermostat is to be connected in addition to a
time switch the wire between the time switch “ON” ter-
minal and boiler terminal 4 should be broken by the con-
tacts of the room thermostat (see schematic layout, Fig.
4.20).
4.14.6 Vaillant optional plug in timer accessories
Refer to the instructions supplied with the optional
accessories for connection details. Upon completion of
all electrical connections refit the terminal box cover by
pushing into place. The cover is secured by two locking
clips.
4.15 Controls
(600
series)
4.15.1 External electrical controls
The boiler terminals 3, 4 and 5 are for connecting exter-
nal electrical controls such as a programmer, room ther-
mostat, etc. Terminals 3 and 4 are linked together when
the boiler is supplied. If external controls are used, this
link must be removed, and the controls connected
across terminals 3 and 4. Terminal 5 is an additional
neutral connection for external controls.
4.15.2 Connection of external electrical controls
4.15.3 Connection details using an external wiring
centre
The boiler should be connected to the system controls
using an external wiring centre. Fig. 4.21, 4.22 shows
connection details for a system utilising a 3 port mid
position motorised valve, figure 4.23, 4.24 shows the
connection details for a system utilising two 2 port
motorised valves (Important: the numbers with arrows
indicate connection to the relevant terminal of the exter-
nal wiring centre).
4.16 Thermostatic
radiator
valves
The boiler has a built in automatic by-pass valve making
it ideal for use in systems with thermostatic radiator
valves (no separate system by-pass is required). For opti-
mum fuel economy where TRV’s are used they must be
used in conjunction with a boiler control interlock. A pro-
grammable room thermostat or separate timer and
room thermostat will ensure complete boiler shut down
when the heating demand is satisfied. (The radiator in
the room containing the room thermostat should not be
fitted with a TRV).
4.17 Frost
protection
The boiler has an integral frost thermostat which is
designed for protection of the boiler. To protect remote
or exposed parts of the heating system or property addi-
tional frost protection measures must be taken such as
the installation of an external frost thermostat. This
frost thermostat should be connected across the boiler
terminals 3 and 4, in parallel with any external heating
controls.
Note
External frost protection cannot be used when
plug in timers are utilised.
4.18 Circulating
pump
The boiler incorporates a built in circulating pump that is
fully prewired (no additional wiring is necessary). The
pump incorporates an automatic overrun period after
the boiler switches off.
4.19 Anticycling
‘economiser’
control
The boiler incorporates a built in anticycling control to
ensure that energy wasteful short cycling of the boiler
cannot occur. This control prevents the boiler from re-
igniting for a preset period after central heating opera-
tion (the hot water operation is unaffected by this con-
trol and hot water can be drawn at any time).
Note
To temporarily override the anticycling control
turn the main boiler on/off switch to the off
position “0” and then back to the on position
“I” after a few seconds.
4.20 Automatic pump spin control (APS)
The boiler incorporates a built in control which will spin
the built in circulating pump and operate the diverter
valve (ecoTEC plus 800 and pro) once in a 23 hour peri-
od. This control helps to prevent seizure when the boiler
is not operated for a period of time. This control is not
active when the power supply to the appliance is turned
off.
Boiler installation sequence 4
Содержание ecoTEC pro 28
Страница 55: ......
Страница 56: ...839592_00 GB 11 2004...