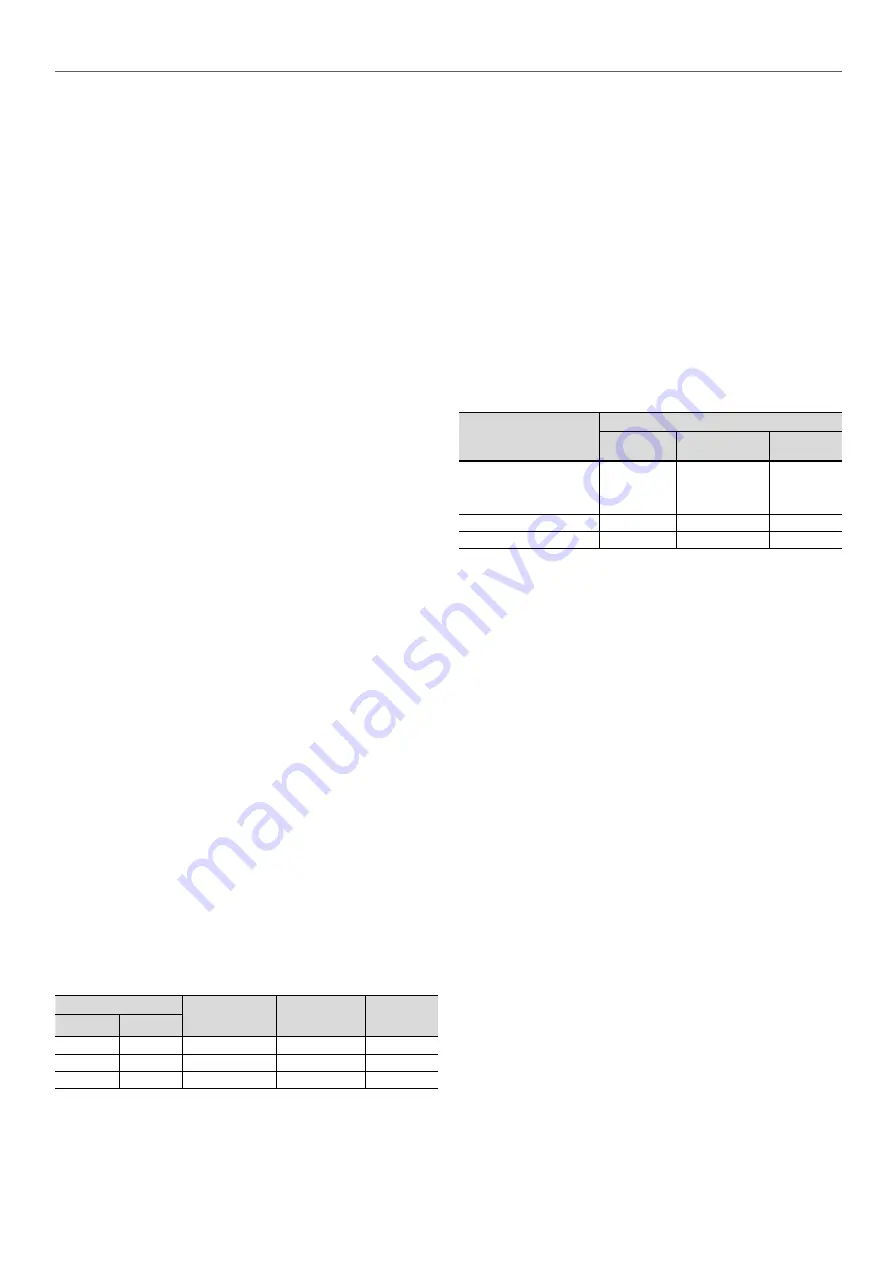
1.3 -
Pressure equipment and components
These products incorporate equipment or components under
pressure, manufactured by Carrier or other manufacturers. We
recommend that you contact your professional body to find out
which regulations affect you as the operator or owner of pressure
equipment or components (declaration, re-qualification, re-testing,
etc.). The characteristics of this equipment/these components are
given on the name plate or in the regulatory documentation
supplied with the products.
These units comply with the European Pressure Equipment
Directive.
The units are intended to be stored and operated in an
environment where the ambient temperature is always within
the allowable temperature range indicated on the nameplate.
Do not introduce significant static or dynamic pressure with
regard to the operating pressures used during operation, or
for tests in the refrigerant circuit or heat exchange circuits.
NOTE: Monitoring during operation, re-qualification, re-
testing and re-testing dispensation:
•
Follow regulations on the monitoring of pressure
equipment.
•
The user or the operator is usually required to create
and maintain a monitoring and maintenance register.
•
In the absence of any regulations, or in addition to the
regulations, follow the guidance in EN 378.
•
Follow the local professional recommendations,
whenever they exist.
•
Regularly inspect the surface of the components for
signs of corrosion. To do this, check an uninsulated
part of the component or check for an accumulation of
rust at the insulation joints.
•
Regularly check for the presence of any impurities (e.g.
sand, grit) in the heat transfer fluids. These impurities
can cause wear and/or pitting corrosion.
•
Install filters in the heat transfer fluid piping.
•
The reports from the regular checks carried out by the
user or operator must be included in the monitoring
and maintenance register.
Repair:
Any repair or modification of a pressurised container is
prohibited.
Only the replacement of the container with an original
manufacturer component is authorised. In this case, the
replacement must be carried out by a qualified operator.
The replacement of the vessel must be entered in the
monitoring and maintenance register.
Recycling:
The pressure equipment can be recycled in whole or in part.
After use, they may contain refrigerant vapours and oil
residue. Some parts are painted.
1.4 - Maintenance safety considerations
Carrier recommends the following table as a guide to completing
the monitoring and maintenance register (logbook) required by
EN 378-2:
Intervention
Name of the
commissioning
engineer
Applicable
national
regulations
Verification
Organism
Date
Nature
(1)
(1) Maintenance, repairs, regular verifications (EN 378), leakage, etc.
Engineers working on the electrical or refrigeration components
must be authorised, trained and fully qualified to do so. All work
on the refrigerant circuit must be carried out by a trained person,
fully qualified to work on these units. He/she must have been
specifically trained on this equipment and system. All welding
operations must be carried out by qualified specialists.
30RQM/30RQP units use high pressure R-410A refrigerant (the
unit operating pressure is above 40 bar; the pressure at an air
temperature of 35°C is 50% higher than for R-22). Special
equipment must be used when working on the refrigerant circuit
(pressure measurement, charge transfer, etc.).
Do not clean the unit with hot water or steam. This may cause
the refrigerant pressure to rise.
Any manipulation (opening or closing) of a shut-off valve
must be carried out by a qualified and authorised engineer,
observing applicable standards (e.g. during draining
operations). The unit must be switched off during maintenance.
NOTE: The unit must never be left shut down with the liquid
line valve closed, as liquid refrigerant can be trapped between
this valve and the expansion device and lead to the risk of a
pressure increase. This valve is situated on the liquid line
before the filter drier.
Equip the engineers that work on the unit as follows:
Personal protection
equipment (PPE)
(1)
Operations
Handling
Maintenance,
service
Welding or
brazing
(2)
Protective gloves,
eye protection,
safety shoe,
protective clothing.
X
X
X
Ear protection.
X
X
Filtering respirator.
X
(1) We recommend to follow the instructions in EN 378-3.
(2) Performed in the presence of A1 refrigerant according to EN 378-1.
Never work on a unit that is still energized.
Never work on any of the electrical components until the
general power supply to the unit has been isolated.
Lock the power supply circuit upstream of the unit in the open
position during maintenance interventions.
If work is interrupted for any reason, check that all circuits
are powered off before resuming work.
CAUTION: Even if the unit has been shut down, the power
circuit remains energized, unless the unit or circuit disconnect
switch is open. Refer to the wiring diagram for further details.
Follow the appropriate safety guidelines. When working on
the fan deck, particularly if the discharge grilles have been
removed, isolate the power supply to the fans to prevent their
operation.
CAUTION: The option Power factor (231) and the variable
frequency drives (VFD) fitted to the 30RQP units and the units
with options 116V, 116W or 28 have capacitor banks whose
discharge time is five (5) minutes after disconnecting the
power supply.
After disconnecting the power supply to the electrical box,
wait for 5 minutes before accessing the electrical box or
variable drives.
Before any intervention, verify that there is no voltage present
on any accessible conducting parts of the power circuit.
It is recommended that an indicating device be installed to
check if any refrigerant has leaked from the relief valve.
The presence of oil at the outlet orifice is a useful indicator
that refrigerant has leaked. Keep this orifice clean to ensure
that any leaks are obvious. The calibration of a valve that has
leaked is generally lower than its original calibration. The new
calibration may affect the operating range. To avoid nuisance
tripping or leaks, replace or re-calibrate the valve.
CAUTION: If refrigerant circuit service valves are installed,
ensure the protective caps are fitted in order to avoid
leakages.
1 - INTRODUCTION
5
Содержание Carrier 30RQM 160
Страница 63: ......