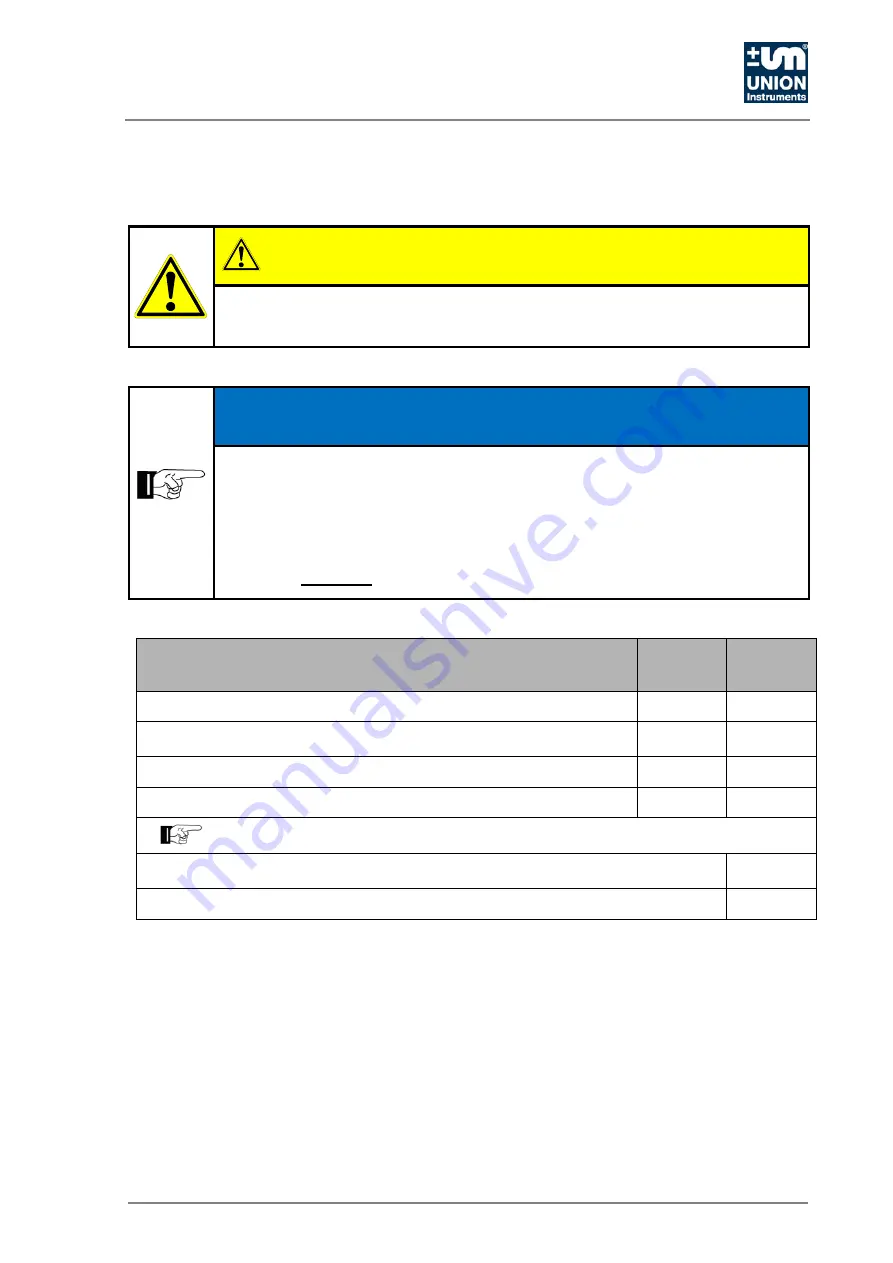
49
9 Decommissioning/switching off
ATTENTION
To decommission the process gas analyser and the linked system components
according to their operating instructions.
NOTE
The following table contains the steps for removing the analyser from service for
a long period.
If you only wish to switch off the process gas analyser temporarily, a few steps
can be omitted:
Column Switch off!
Steps
Turn off
Removing
from
service
Disconnect the device from the process, close the line professionally.
X
X
Rinse the process gas analyser with ambient air. (Start calibration with
purge gas)
X
Shut down the linked system components.
X
X
Turn off the main switch.
X
X
If you only wish to switch off the process gas analyser temporarily, follow the
procedure here to the end!
If required, disconnect / switch off the operator's energy and media supply and the
signal transmission professionally.
X
If applicable, pack process gas analyser in a suitable way.
X
Содержание INCA4004
Страница 1: ...Apr 2016 V1 10 Translation of the original operating instructions Process gas analyser INCA4004 ...
Страница 3: ...3 Dimensions ...
Страница 4: ...4 ...
Страница 8: ...8 ...
Страница 12: ...EU Declaration of Conformity 12 ...
Страница 32: ...Transport setup and acceptance 32 ...
Страница 34: ...Startup switching on 34 ...
Страница 48: ...Operation 48 ...
Страница 50: ...Decommissioning switching off 50 ...
Страница 54: ...Maintenance 54 ...
Страница 58: ...Service 58 ...
Страница 60: ...Accompanying documents 60 ...
Страница 62: ...Disposal 62 ...
Страница 64: ...Spare parts 64 ...
Страница 65: ...65 16 Annex ...
Страница 66: ...Annex 66 EU Declaration of Conformity Flame arrester ...
Страница 67: ...Annex 67 ...