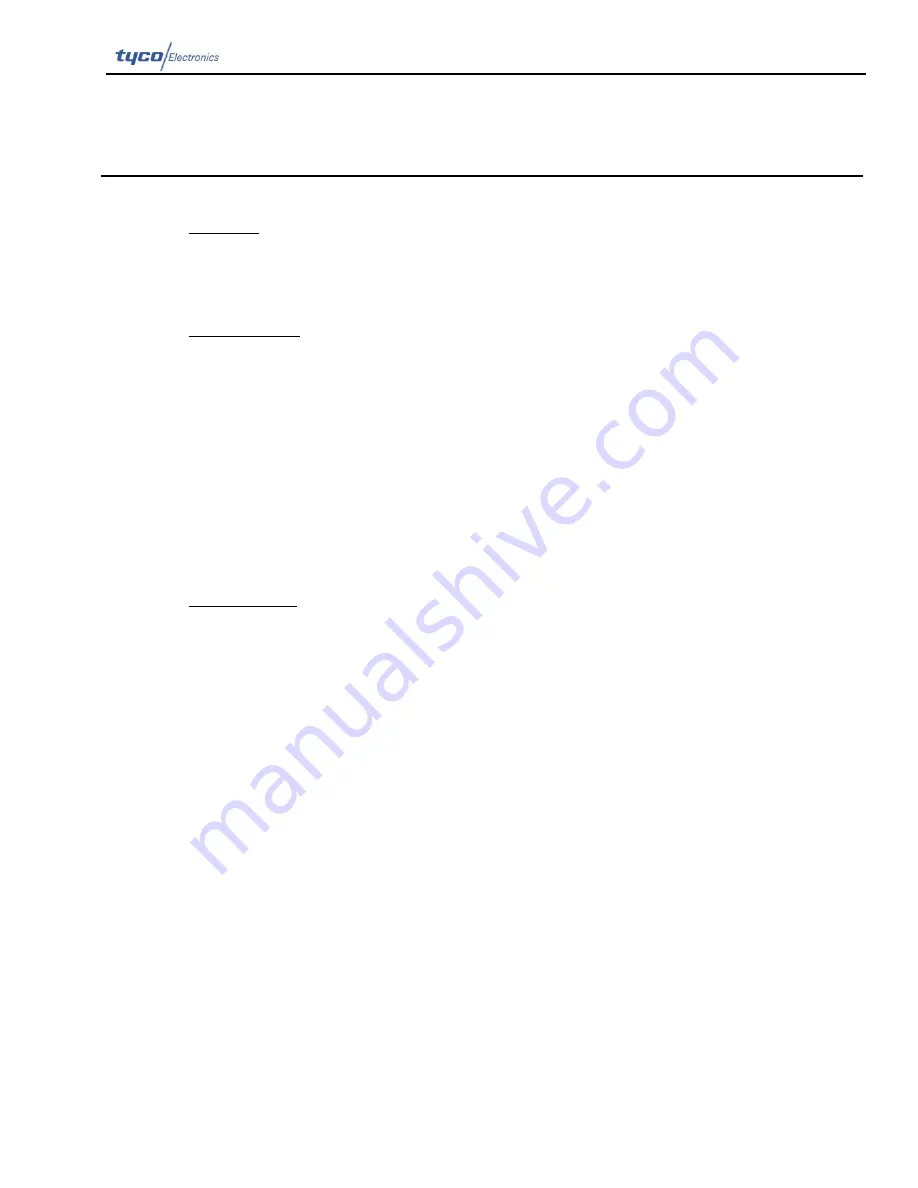
Wire and Harnessing Products
Engineering Specification
No:
ES 61402
Rev:
D
Date: July 9, 1991
Page: 12 of 16
If this document is printed it becomes uncontrolled. Check for the latest revision.
4.0
Calibration Verification Test
4.1 Objective
This procedure is performed to verify whether the Waffle Iron II control system is operating
correctly and the heating temperatures are within the specified ranges. Results of this test will
determine if the heating tool can be used, or if it must be recalibrated by an authorized
Raychem representative. No adjustments are to be performed.
4.2 Tools
Required
o
Test platen:
a. For early model Waffle Iron II's without thermocouple connection on back, the
CE-1406800 calibration platen is required.
b. For late model Waffle Iron II's with thermocouple connection on back of unit, any
platen set in good condition or a CE-1406800 calibration platen can be used.
o
Digital thermometer with peak hold feature, or strip chart recorder; must be
compatible with type K thermocouple.
o
Stop watch
4.4 Test
Procedure
1. Install test platen:
o
For early model Waffle Iron II's without thermocouple connection on back of unit,
remove the production platen and install the CE-1406800 calibration platen. The
calibration platen locks into the lower heat sink the same as a production platen.
o
For late models with thermocouple connection, install the normal production platen
set in the Waffle Iron II. (The CE-1406800 calibration platen may also be used.)
2. Close and latch the upper heat sink.
3. Connect the temperature recording device to the thermocouple.
o
If the Waffle Iron II is an early model without a thermocouple connection, connect
the thermocouple lead of the CE-1406800 calibration platen into the temperature
recording device.
o
If the Waffle Iron II is a late model and has a thermocouple connection, connect the
thermocouple lead (supplied) between the temperature recording device and the
thermocouple connection on the back of the unit.
4. Turn the Waffle Iron II on.