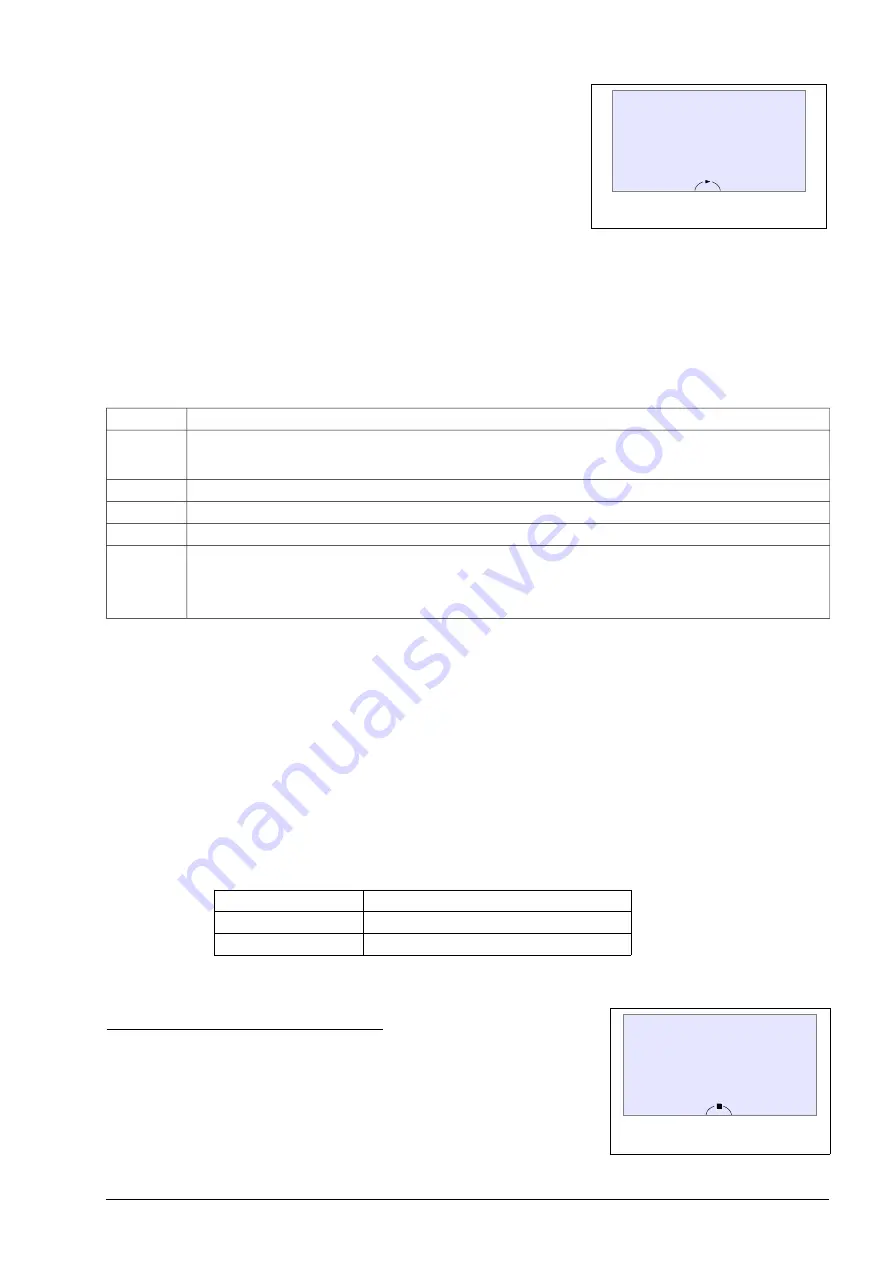
3.8. Changing the rotational speed of the motor (output frequency) from the control panel
The motor speed can be easily changed from the control panel, provided that
at least one of the following conditions is met:
•
the source of the motor speed is the control panel
(par. 2.2 = „133 Keyb. ref.”),
•
The PID controller reference-unit was set to be controlled from the
control panel (par. 2.60 = „143 Keyb.P”),
•
one of the four user’s referencing-units is active (see chapter 11.5).
Then, in the "Basic view", using the up / down „
” „ ”
arrow keys you can
change the motor speed - fig. 3.5. You can return to the "basic view" by
pressing the ESC key.
Note: Only one (or none) of the above-mentioned referencing-unit can be
active at a time.
3.9. PD access levels and parameters locks
If there is a padlock symbol on the left side of the parameter, it means that it is locked and it is impossible to
change its value. Possible causes of parameter editing lock:
•
some parameters can be changed only when the converter is not running (the motor is stopped),
•
the active access level does not allow the parameter to be modified.
Table 3.3 - Parameters responsible for locks and access levels
Parameter
Description
4.1
Switching On the parameter change lock. When set to "001 YES", it will not be possible to change parameters (except
for "4.1 Par. block." and "4.2 Level/CODE"). The lock has two variants, depending on whether the code to access level
1 (PD 1) is set to 0 (default value) or to a different number - see section 3.9.2 "Parameter locks".
4.2
Active PD access level (reading), entering the access code (writing).
4.3
Changing the access code for the active level (see par. 4.2).
4.4
Load a set of factory settings of the drive
4.5
Lock of physical parameter writing to EEPROM memory.
Service parameter - do not use.
Setting this parameter to "000 NO" causes that all changes made to parameter settings are saved only in the
temporary memory and will be lost after power off or reset of the converter.
3.9.1. PD access levels
In order to protect the converter settings against unauthorized changing, 3 levels of PD access to parameters
are avaible:
•
PD 0 (level 0 - lowest)
– parameters cannot be changed. Parameter "4.1 Par. block." always has the value
"001 YES" and it cannot be changed.
•
PD 1 (level 1 - default)
– it is possible to edit parameters (except for "4.4 Fact. set." and "4.5 En. EEPROM").
•
PD 2 (level 2 - highest)
– designed to load factory parameters – see chapter 3.7 “Restore factory settings”.
Each PD access level has its own number (code) assigned, which is a number from 0 to 9999. The change of
the PD access level is done indirectly by entering par. "4.2 Level/CODE" of the corresponding code number as shown in
table 3.4.
If a code not assigned to any of the PD access levels is entered, then after confirming the entered value with
the Enter key, the PD access level will not be changed.
Table 3.4 - Default code values assigned to PD access levels
PD access level
Code (default)
1
0
2
1
A user can assign a different code to a given access level - see section 3.9.3 “Change of access codes”.
Example of changing the access level to PD 2
By default, the access level PD 2 is assigned a code with the value 1. This
value should be entered in par. "4.2
Level/CODE
" and confirmed with the Enter
key
„ ”
. The screen changes to fig. 3.6.
Note 1: The PD 2 access level is intended for loading predefined factory
settings - section 3.7 “Restore factory settings”.
Note 2: After power off or reset of the converter (caused by e.g. loading of
factory settings) the PD access level will automatically return to the PD 1 level.
MFC710 User Manual - TWERD Power Electronics
25
A
LO
LO
PD = 2
4 Disp, RS, user
4.2 Level
Fig. 3.6 - Screen view when access
level PD = 2
A
LO
LO
Keypad reference
[ 0020.0]
Hz
Fig. 3.5 - Change of frequency
output from the control panel