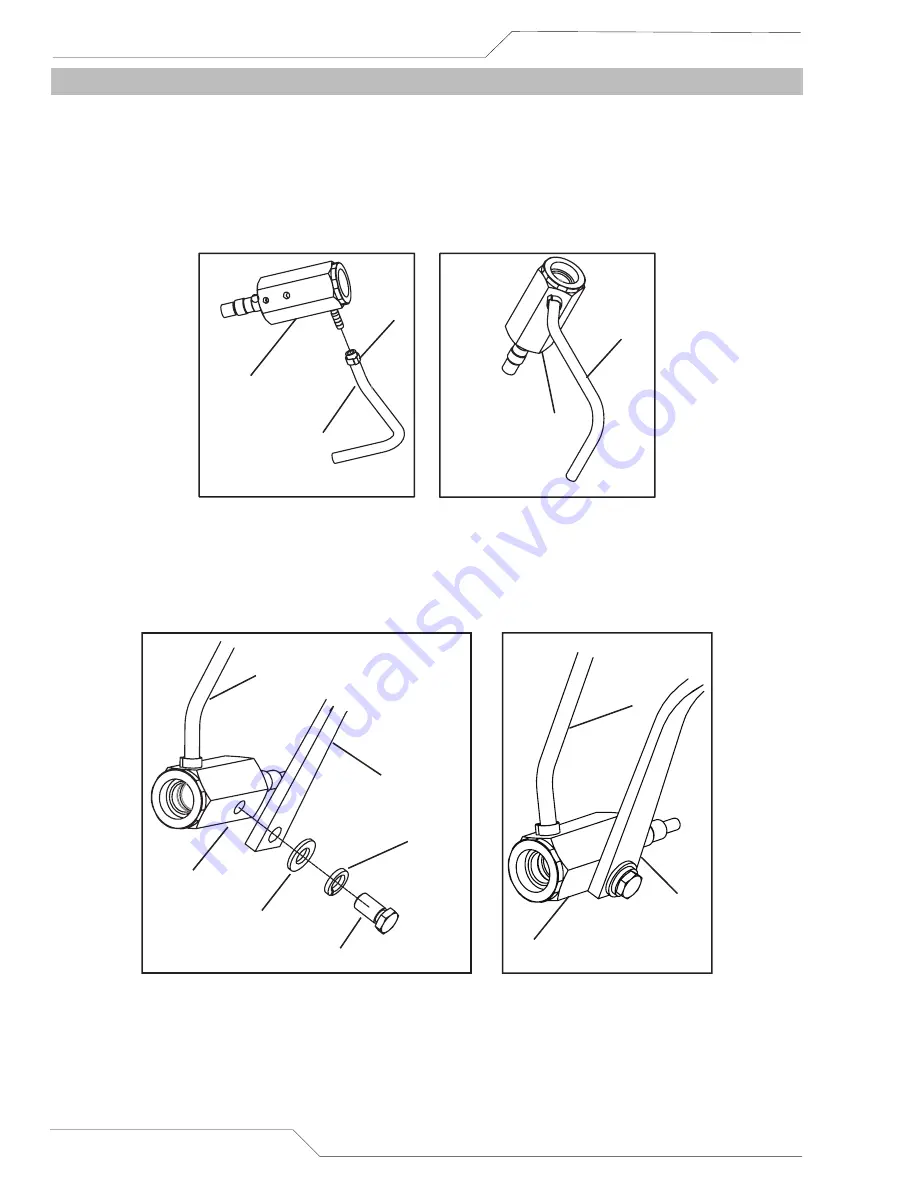
ULTRAFEED VAF-4
7-2 ASSEMBLY PROCEDURE Manual 0-5332
7.02 Installing Tweco No. 4 Adaptor
1. Reconnect the gas hose.
a. Place the hose clamp over gas hose.
b. Push the gas hose onto the Tweco No. 4 Gun Adaptor gas inlet.
c. Slide the hose clamp forward until it sits approximately 5mm from the end of the gas hose.
d. Tighten the hose clamp with a suitable crimping tool.
Gun Adaptor,
Tweco No. 4
Hose Clamp
Gas Hose
Gun Adaptor,
Tweco No. 4
Gas Hose
Art # A-12820
Figure 7-2 Reconnecting Gas Hose
2. Reconnect the welding cable.
a. Attach the welding cable lug to Tweco No. 4 Adaptor, using the M10 Flat Washer, M10 Spring Washer and
M10 × 18 Hex Bolt.
Welding Cable
Flat Washer, M10
Spring Washer, M10
Hex Bolt, M10 × 18
Art # A-12821
Welding Cable
Gun Adaptor,
Tweco No. 4
Gun Adaptor,
Tweco No. 4
Gas Hose
Gas Hose
Figure 7-3 Reconnecting Welding Cable
Содержание ULTRAFEED VAF-4
Страница 68: ...ULTRAFEED VAF 4 4 38 OPERATION Manual 0 5332 Notes...
Страница 100: ...ULTRAFEED VAF 4 6 12 DISASSEMBLY PROCEDURE Manual 0 5332 Notes...
Страница 116: ...ULTRAFEED VAF 4 A 2 APPENDIX Manual 0 5332 Art A 12826 Appendix 2 connection diagram...
Страница 118: ...This Page Intentionally Blank...