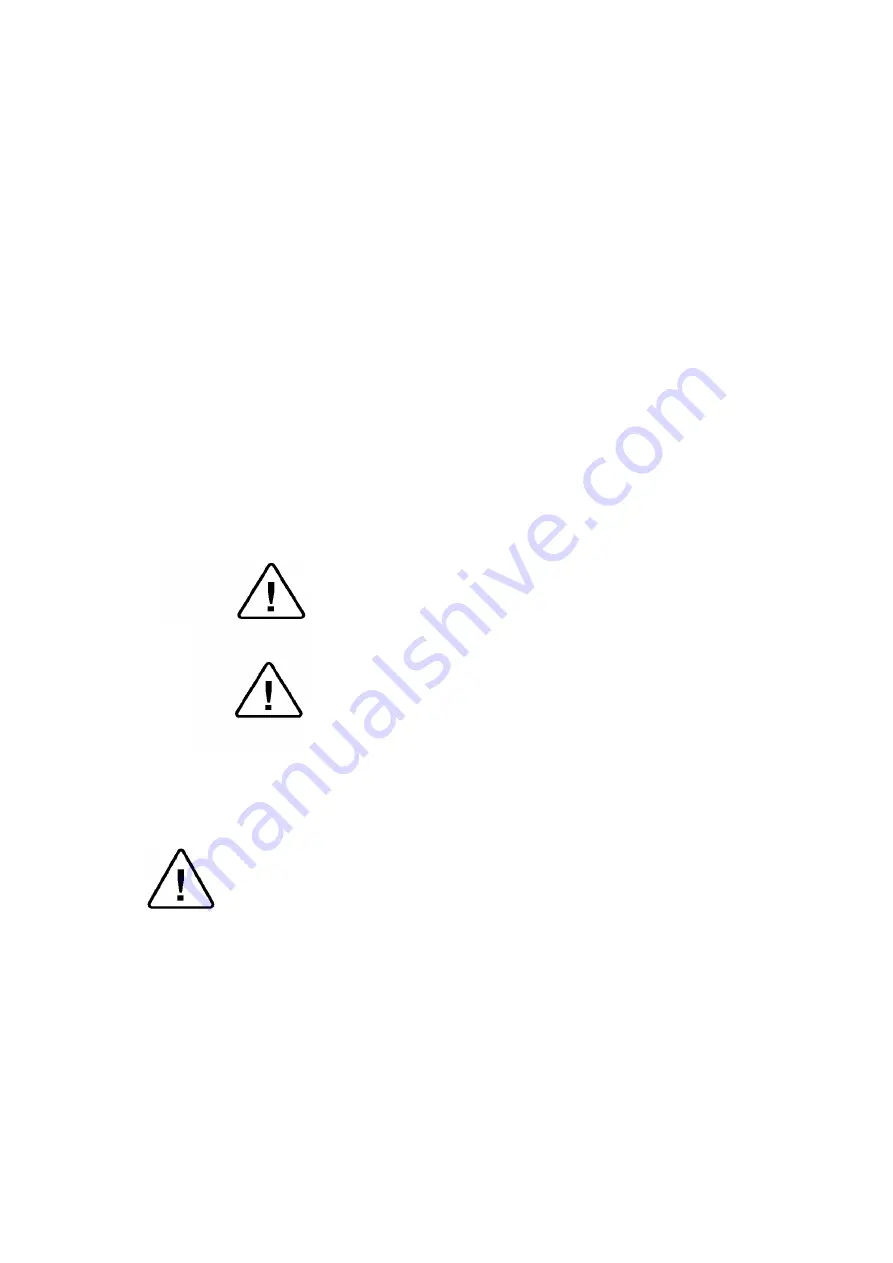
32
6.2.3
Checking the automatic fill
To check the automatic fill, follow these steps:
1.
Remove any water that is in the chamber.
2.
Make sure the unit is turned on.
3.
Place a collecting vessel under the autoclave's door.
4.
With the door open, press and hold the door switch, then press
the
START
key.
5.
When water starts flowing into the chamber, release the door
switch.
6.
Water should come beyond the groove at the front of the
chamber, and a small amount will pour into the collecting
vessel.
7.
After the automatic filling is completed, tilt the autoclave and
pour all the water in the chamber into the collecting vessel.
8.
Measure and verify that the amount of water pumped into the
chamber is 500-600 ml.
9.
If the water is not filling correctly, follow the adjustment
procedure above.
Warning:
If it becomes necessary to RESET the software program, it
will be essential to repeat all steps listed above. This will
ensure that the correct amount of water enters the chamber
for operation.
VERY IMPORTANT – Due to the fact that the water lines
are empty when the unit is shipped, air may become trapped
in the lines. It is recommended that, for the first operation,
these steps are followed to make sure water is flowing freely.
Open the door, press the Water Inlet key. When water enters
the chamber, release the key and remove the water.
6.3
Lifting and Carrying
Caution:
Before moving the autoclave, make sure that the electric cord is
disconnected from the power and there is no pressure in the chamber.
1.
Disconnect the power supply cord.
2.
Drain the water from the reservoir and vessel.
To avoid injuries, lifting and carrying should be done by two people.
Do not drop this device!
Содержание 1730E
Страница 2: ......
Страница 16: ...14 REAR VIEW EA EKA only Cut Out Thermostat Reset button...
Страница 18: ...16 FRONT PANEL KEYBOARD NEW TYPE BLUE Note See section 3 2 for a description of the Keyboard buttons...
Страница 41: ...39 MAINTENANCE INSTRUCTIONS...