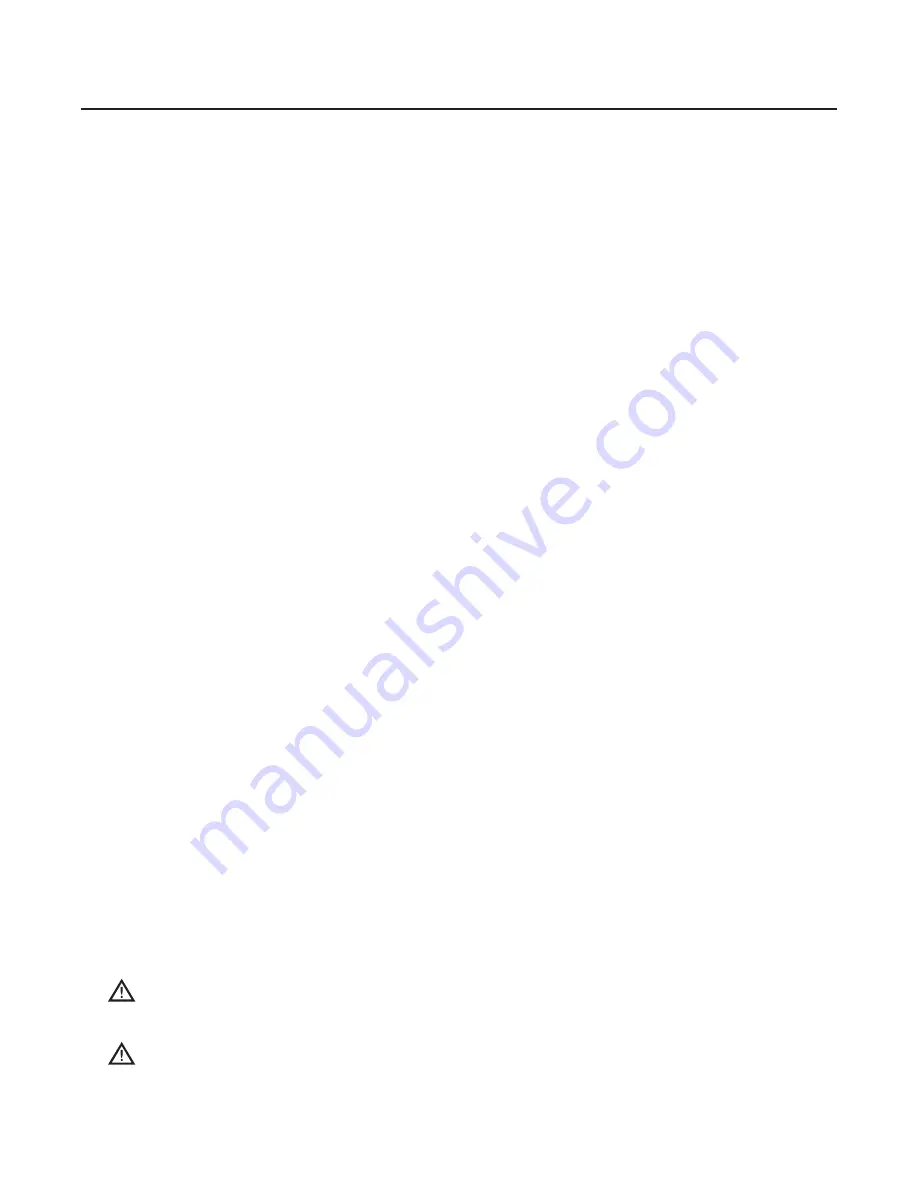
START-UP
9. Verify
proper
fl
ame recti
fi
cation.
a. Ensure the oven is in the off or cooling down
mode.
b.
Remove
the
fl
ame signal ground wire from the
ignition
module.
c. Connect a DC multipurpose meter that is able
to read micro amps (
u
A) in series with the
fl
ame
signal
ground
wire.
i. Connect the red (+) meter lead to the free end
of the
fl
ame signal ground wire.
ii. Connect the black (-) meter lead to the quick
connect
fl
ame signal ground wire terminal on
the ignition module.
d. From the off or cooling down mode, select a
cooking
pro
fi
le to operate the oven burner.
e. The reading must be above 1.5 DC
u
A and it
must be steady.
The oven control system uses basic
fl
ame recti
fi
cation
to verify if a
fl
ame is present. The micro amps must
be greater than 1.5 DC
u
A. If the reading is below
1.5
DC
u
A or is not steady, remove the burner
assembly and investigate the cause. Look for a loose
ignition/sensor wire, or defective sensor assembly.
Follow the troubleshooting steps outlined in the
service
manual.
10. Con
fi
rm all pressure taps have been properly closed
off by performing a soap solution test (see
Connections, pages 10-11). Look for any enlarging
bubbles on all the gas connections. Always adhere
to local gas codes and required methods of leakage
testing in the immediate location (refer to the
regulations in force in the country in which the
appliance is being installed). The prevailing authority
is the local code (or regulations).
11. On the Start-Up Checklist, indicate if the gas
connections passed the soap test.
Ventilation
Performing a ventilation test is required. TurboChef
suggests using a smoke test; however, check with the local
code authority to ensure that no other test is required (re-
fer to the regulations in force in the country in which the
appliance is being installed). The prevailing authority is
the local code (or regulations). Smoke testers are available
through TurboChef. Call 800.90
TURBO
(+1 214-379-6000) for pricing and availability.
1. Perform a smoke test.
a. Turn on the ventilation hood.
b. Turn the oven(s) on.
c. Ready the oven for the smoke test.
i. Select a cooking pro
fi
le.
ii. Press the temperature key.
iii. Press and hold the up arrow until the
display reads above 500°F (260°C).
5. Turn the oven on and select a cooking pro
fi
le.
During warmup (or while both fan speeds are set to
65%), verify the gas pressure at the main burner
during
100%
fl
ame. Take this reading from the
lower tap of the gas valve (
fi
g.
Gas, Steps 4-7
). This
tap shows the gas valve’s internal regulator settings.
The maximum operating pressure for natural gas
and propane is 3.5” W.C. (88.9 mmH
2
O, 8.71 mb),
unless operating I
2L
gas — see note below. If needed,
using an 8mm nut driver, adjust the 8mm nut (
fi
g.
Gas, Steps 4-7
) until the manometer reads 3.5” W.C.
(88.9
mmH
2
O, 8.71 mb) unless operating I
2L
gas —
see note below. Turn the 8mm nut driver clockwise
to increase the pressure, or counterclockwise to
decrease the pressure.
NOTE:
The oven operates at the same pressures for all
types of gas, except I
2L
(4” W.C. [101.6 mmH
2
O,
9.96 mb]).
NOTE:
Pressures are factory set and require only minimal
adjustment. Verify oven operation on the display. Con-
fi
rm the oven is operating at 100% at the time of the test.
6. Verify the gas pressures at minimum
fl
ame. This
measurement is taken from the lower tap of the gas
valve while either the red or white wire is
disconnected (page 11,
fi
g.
Gas, Steps 4-7
). This tap
will show the gas valve’s internal minimum
fl
ame
regulator settings. The pressure for both natural gas
and propane is 0.10” W.C. (2.54 mmH
2
O, 0.249
mb). If needed, using a 5mm nut driver, adjust the
5mm nut (page 11,
fi
g.
Gas, Steps 4-7
) until the
electronic manometer reads 0.10” W.C. (2.54 mm
H
2
O, 0.249 mb). Reconnect the wire you
disconnected.
NOTE:
To ensure the burner is operating at the mini-
mum
fl
ame, disconnect the red wire from the modulating
coil of the gas valve (page 11,
fi
g.
Gas, Steps 4-7
).
7. Verify the incoming gas pressure (operating). This
is the pressure sent to the oven from the existing
piping system when the oven is operating at 100%
fl
ame. Take this reading from the upper tap of the
gas valve (page 11,
fi
g.
Gas, Steps 4-7
). This tap will
show the incoming pressure before the regulator
inside the gas valve. The pressures must be no less
than 6” W.C. (152.4 mm H
2
O, 14.94mb)
and no
more than 14” W.C. (350.6 mm H
2
O, 34.87 mb).
CAUTION: A pressure of less than 6” W.C. (152.4
mm
H
2
O, 14.94mb) can cause potential cook
problems.
WARNING: The pressures must be no more than
14” W.C. (350.6 mm H
2
O, 34.87 mb).
Otherwise,
severe damage to the equipment can occur.
8. On the Start-Up Checklist, indicate if any
adjustments were made.
12
Содержание HHC-3240
Страница 2: ......
Страница 3: ...For further information call 800 90TURBO or 1 214 379 6000 ...
Страница 20: ......
Страница 21: ......