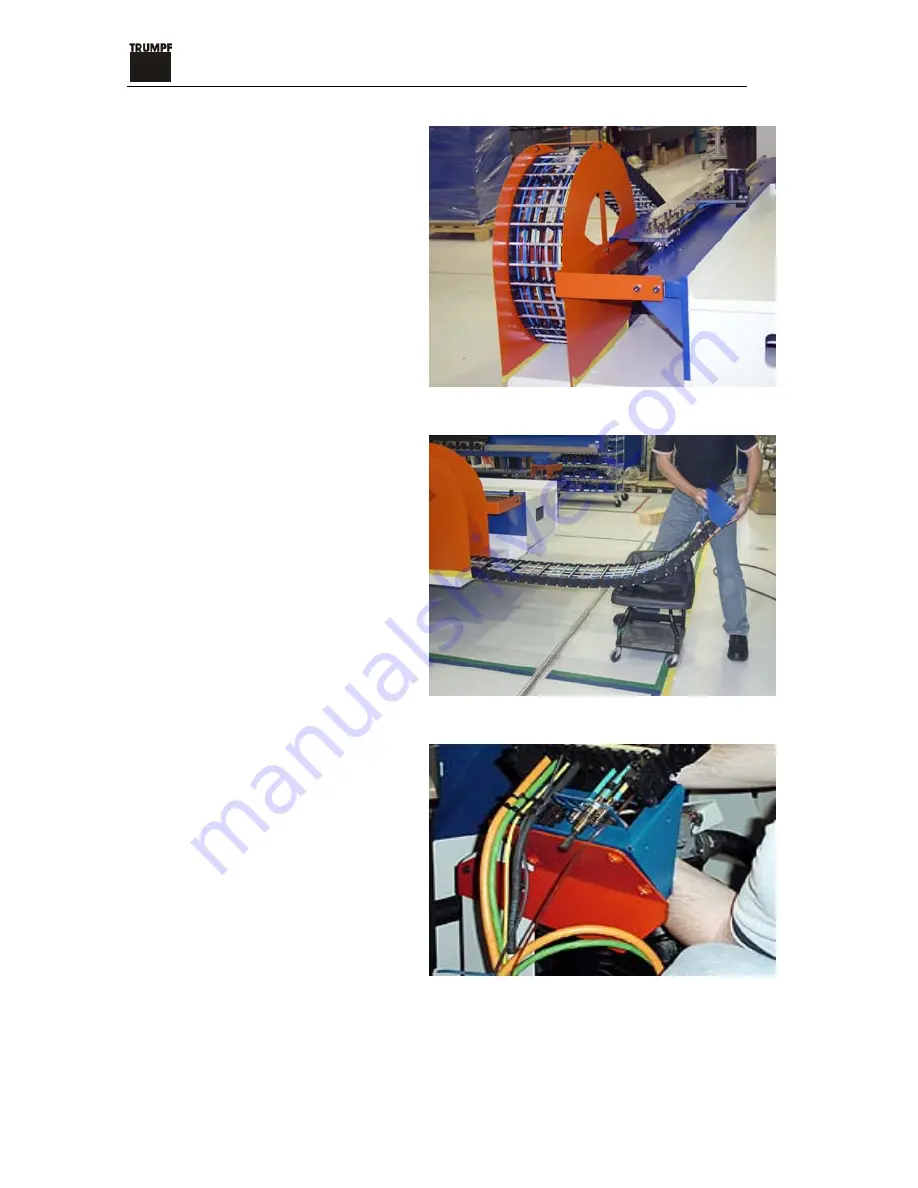
TC 2020R Installation
TR22.1 2020 Installation with SMC_July_03
14
31. Remove shipping bracket for the
energy chain.
Figure 32. Energy chain shipping bracket
32. Pay attention to the energy chain.
Do not snap the chain.
Figure 33. Lay the energy chain on a support
33. Remove the energy chain hold-
down bracket.
Figure 34. Energy chain hold-down bracket