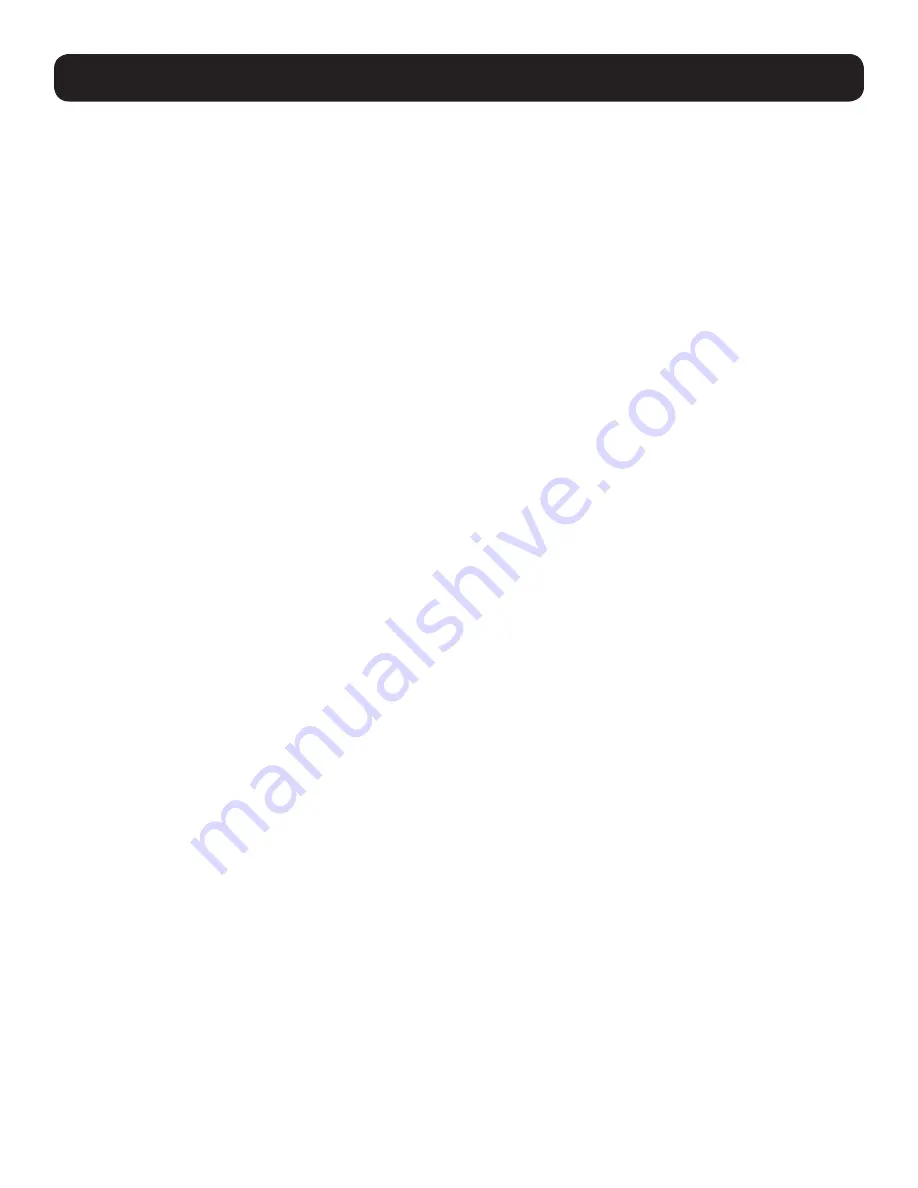
28
9. Basic Test Procedure
9.2.3 Compressor Replacement
The following procedure applies when replacing components in the sealed refrigeration circuit or repairing refrigerant leaks.
This includes the compressor, condenser, evaporator, capillary tube, refrigerant leaks, etc.
1. Recover the refrigerant from the system at the high-side service port (HP) and low-side service port (LP). Apply gauge from
the service port(s) to an EPA-approved recovery system. Recover CFCs in system to at least 5%.
2. Disconnect the high-side service port (HP) and make sure it is closed.
3. Connect the line from the nitrogen tank to the low-side service port (LP).
4. Drift dry nitrogen through the system and unsolder the more distant connection first (filter drier, high side process tube,
etc.).
5. Replace the inoperative component. Always install a new filter drier. Drift dry nitrogen through the system when making
these connections.
6. Pressurize system to 30 PSIG with proper refrigerant and boost refrigerant pressure to 150 PSIG with dry nitrogen.
7. Leak test the complete system with an electric halogen leak detector, correcting any leaks found.
8. Reduce the system to zero-gauge pressure.
9. Connect a vacuum pump to the high-side service port (HP) and low-side service port (LP). When connecting to the system,
make sure to deep vacuum hoses or copper tubing (
do not use regular hoses
).
10. Evacuate the system to maximum absolute holding pressure of 200 microns or less.
Note:
This process can be sped up by use of heat lamps, or by breaking the vacuum with refrigerant or dry nitrogen at 5,000 microns.
Pressure system to 5 PSIG and leave in system for a minimum of 10 minutes. Recover refrigerant and proceed with
evacuation of a pressure of 200 microns or a minimum of 10%.
11. Break vacuum by charging the system from the high-side service port (HP) with the correct amount of refrigerant specified.
This will prevent boiling the oil out of the compressor.
Note:
If the entire charge will not enter the high side, allow the remainder to enter the low side in small increments while operating the
unit.
12. Restart the unit several times after allowing pressures to stabilize. Disconnect all the hoses and close both the high-side
service port (HP) and low-side service port (LP).
9.2.4 Special Procedure in the Event of Compressor Motor Burnout
1. Recover all refrigerant and oil from the system (see section
9.2.3 Compressor Replacement
for details).
2. Remove compressor, capillary tube and filter drier from the system.
3. Flush the evaporator, condenser and all connecting tubing with dry nitrogen or equivalent to remove all contamination from
system. Inspect suction and discharge line for carbon deposits. Remove and clean if necessary.
Notes:
• A chemical flushing agent can be used.
• When using a chemical flushing agent, force out the agent with nitrogen.
4. Reassemble the system, including new drier strainer and capillary tube.
5. Proceed with processing as outlined under hermetic component replacement (see section
9.2.3 Compressor
Replacement
for details).
Содержание SRCOOL33K
Страница 4: ...4 2 Unit Dimensions 78 4 in 1991 mm 42 7 in 1085 mm 23 6 in 599 mm...
Страница 7: ...7 5 PCB and Wiring Diagrams 5 1 Circuit Diagram UPPER FAN MOTOR LOWER FAN MOTOR...
Страница 10: ...10 5 PCB and Wiring Diagrams 5 2 1 3 Power PCBA Gerber Layout...
Страница 14: ...14 5 PCB and Wiring Diagrams 5 2 3 2 Translator PCBA Gerber Layout...
Страница 39: ...39 2 Dimensiones de la Unidad 1991 mm 78 4 1085 mm 42 7 599 mm 23 6...
Страница 45: ...45 5 Diagramas del Cableado y PCB 5 2 1 3 Diagrama PCBA Gerber de Energ a...
Страница 49: ...49 5 Diagramas del Cableado y PCB 5 2 3 2 Diagrama del Traductor PCBA Gerber...
Страница 71: ...71...
Страница 72: ...72 18 06 003 93 3868_RevA 1111 W 35th Street Chicago IL 60609 EE UU www tripplite com support...