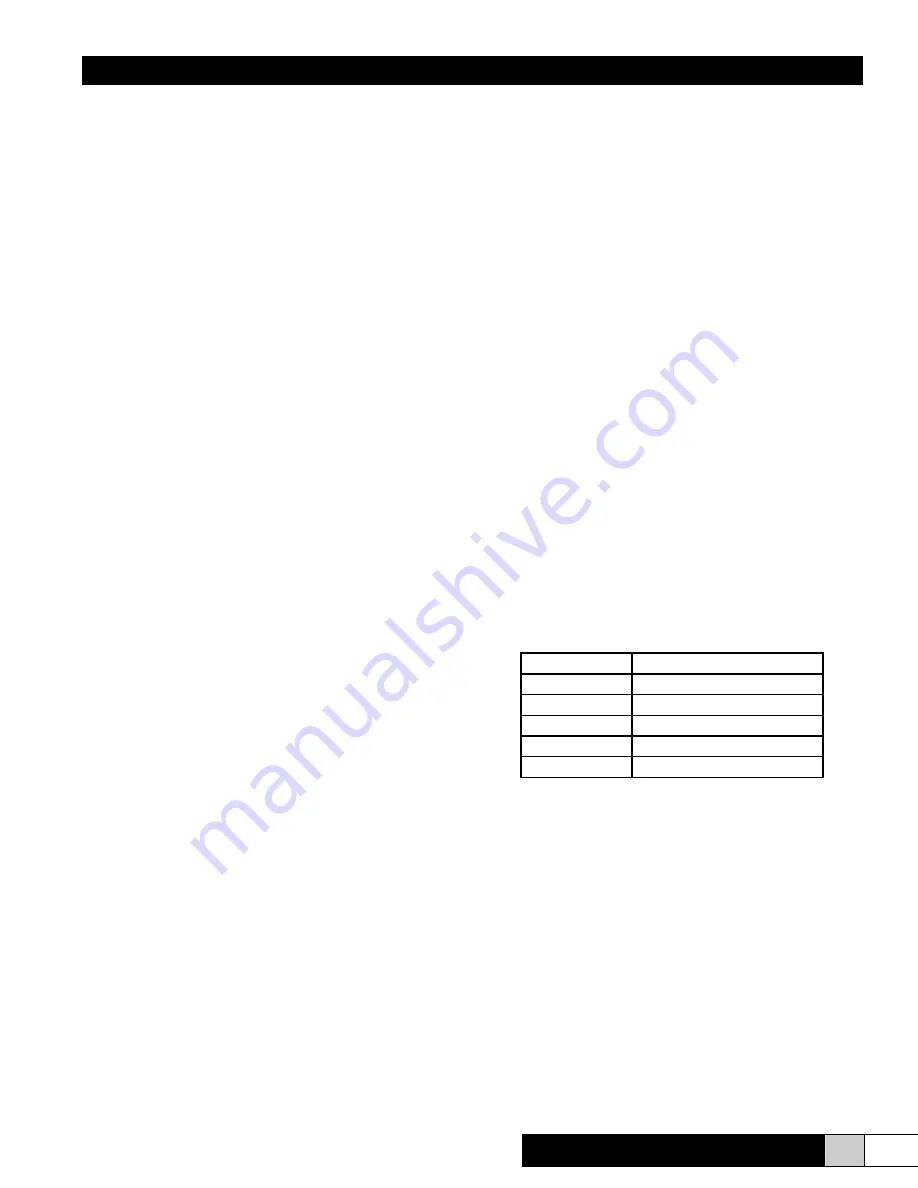
Dual Pneumatic
I n s t a l l a t i o n , O p e r a t i o n & S e r v i c e M a n u a l
11
www.trioniaq.com
Adjust air pressure regulator of control section to 30 psi.
Slowly move the CONTROL humidistat to a higher RH
until you hear a “click” indicating the 2-way solenoid valve
on the air control section has opened. NOTE: If only one
humidistat is used, follow above procedure slowly raising
RH setting, or if switch is used, turn to ON. Reduce the
setting on the SAFETY humidistat until you hear a click
indicating the 3-way solenoid on the water line has closed.
(If no safety humidistat is used, skip this step.) Open the
AIR valve ONLY on one pair of heads. There should be a
constant flow of air from the heads with no flow of water.
This will indicate that the controls for the control section
are properly wired. Make any corrections needed. Close
the air valve after determining wiring is correct. Repeat
the above at each control section in the system.
5. CLEAN DISTRIBUTION LINES FROM CONTROL
SECTIONS TO HEAD ASSEMBLIES.
IMPORTANT:
Be sure all air and water valves at head assemblies are
closed (Step 2). AIR LINES: Put on safety glasses. With
CONTROL humidistat ON and air valve at control section
open, place bucket and cloth over hose bib at end of each
air line and slowly open the hose bib and allow line to
blow clean. DO NOT LOOK INTO BUCKET WHILE AIR
IS BLOWING. Close hose bib. Repeat on all air lines
from each control section. WATER LINES: (Air valve at
control section should be open.) Set SAFETY humidistat
at maximum and CONTROL humidistat ON. Open water
valve at control section. Place bucket or hose on ends
of water lines and slowly open hose bibs. Allow water to
flow until clean. Throttle valve to avoid splashing. Close
hose bib. Close air and water valves at control section.
Repeat on all water lines from each control section.
6. STARTING THE SYSTEM.
Close air and water valves
at all control sections. Open air valves only at all head
assemblies. Set humidistats high enough to assure
system operation. Open AIR valve at control section.
With air flowing through heads, adjust primary air
pressure regulator (or compressor) to maintain 55 psi.
Adjust control section air pressure regulator to 30 psi.
With water valve open at water source, open the control
section water valve and the water valve of the ONE
head assembly located the GREATEST distance from
the control section. Adjust the primary water pressure
reducer to provide 45-50 psi to the control section.
Adjust control section water valve to provide 32-38 psi
to heads. Open the water valve at each head assembly,
checking and correcting for air and water leaks as you
go. CAUTION: Never let water pressure get below
air pressure as air will then get into water lines and
necessitate bleeding of lines. Repeat procedure on all
control sections and primary reducers. Normally, with all
heads operating, it will be necessary to again adjust the
primary water pressure reducer to 45-50 psi and control
section water pressure regulator to 32-38 psi. Tighten
the locknut on all WATER pressure regulators - primary
and control section. All further adjustments will be made
on air controls and at heads. With the entire system in
full operation, check for leaks in all air and water lines,
fittings, connections, valves, control sections, and head
assemblies. Correct as required.
7. FINAL ADJUSTMENTS TO HEADS.
Remove cap
(253206-00X) of each head. This cap is at the non-
discharge end of the head and covers the head adjusting
“spring tension nut” (253207-00X). Slowly turn this
adjusting nut in a clockwise direction until no water is
discharged by the head. Use care to avoid damage to
the valve seat. Then, back off this adjusting nut TWO full
turns counter clockwise. This may result in an excessively
heavy spray, but this will be adjusted later in the control
section. Replace cap. Repeat this operation on every
head on the system. NOTE: Maintain air pressure at 30
psi and water pressure at 32 - 38 psi. Do NOT let air
pressure exceed water pressure.
8. BALANCING THE SYSTEM.
The final and most
important adjustment will be made at the air pressure
regulator of each control section. Adjust the air regulator
to 30 psi; adjust water pressure for proper head capacity.
Increasing the air pressure to the heads results in smaller
droplet size in discharge pattern - and vice versa. Spray
pattern should be visible to at least 10’ from the head to
assure rated capacity. With the system in full operation,
adjust the safety humidistat to 10% above the desired
level. Remove the cover of this humidistat and set the
low and high limit stops to the RH setting so the setting
cannot be changed. Replace cover. Move the CONTROL
humidistat setting alternately lower and higher to cycle
the system OFF and ON several times until all gauges
become repetitive in action and readings.
Water Pressure Settings
Head Capacity
Water Pressure Setting (PSI)
6
32
8
38
10
33
12
35
15
37
Note: A new system may require some adjustment until all parts are
properly seated during break-in. This period may last about two weeks.
After that, adjustments may not be required but should be checked on a
regular schedule. Set the humidistat at the desired level.
CAUTION:
1. Do not balance the system by adjusting individual heads. Each
head has been adjusted to provide its design capacity.
2. Do not throttle any valves at control sections or head assemblies to
get final adjustment.
VI. OPERATING INSTRUCTIONS
The Dual Pneumatic Atomizing System utilizes air and water
under pressure to atomize the water into tiny droplets (2-
15 microns with an average of 7.5). These droplets rapidly
evaporate to a gaseous state to raise the level of relative
humidity.