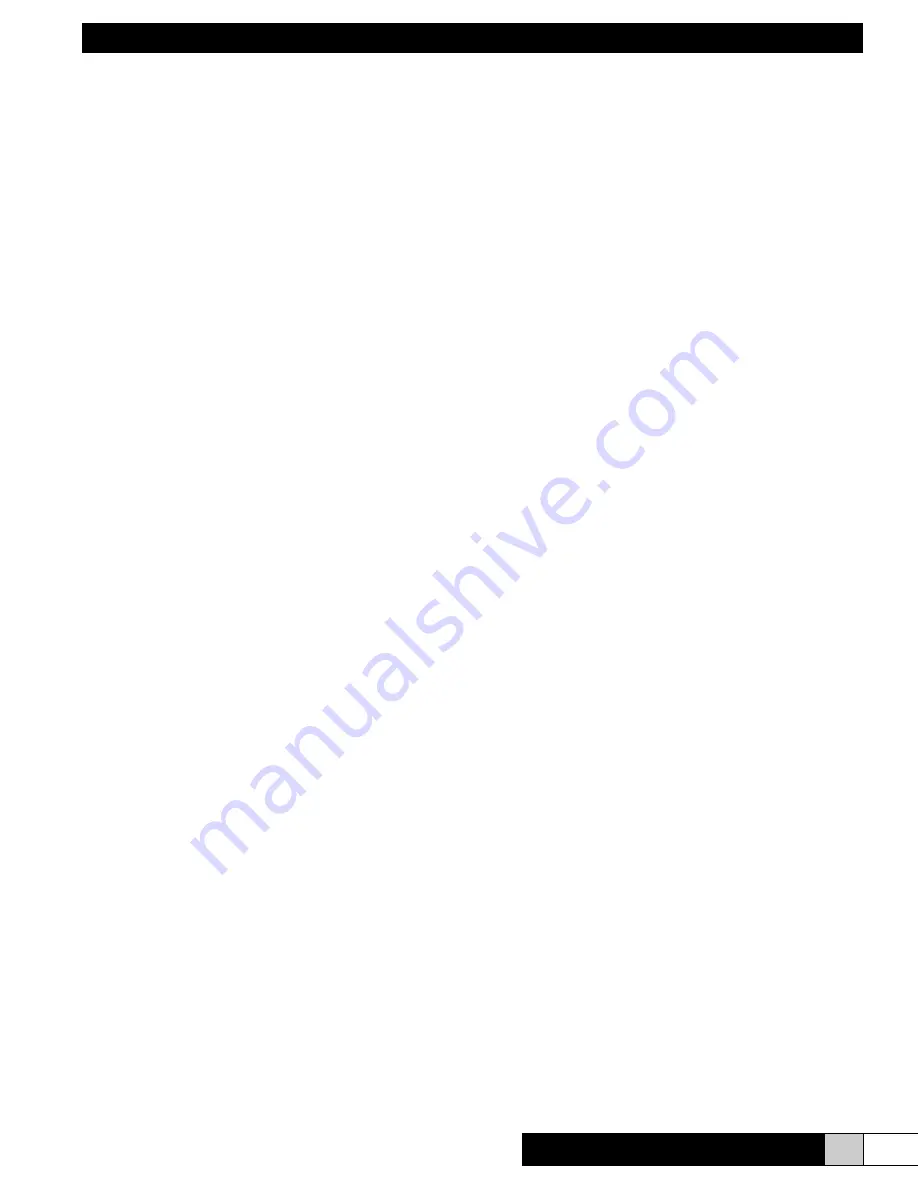
www.trioniaq.com
Grease Viper
10
I n s t a l l a t i o n , O p e r a t i o n , & S e r v i c e M a n u a l
others and require a stronger detergent solution.
Average settings have been factory set. Best possible
settings for any given installation, however, are
determined through experience. Determination can be
made by visually examining the collecting elements
after the first few wash cycles.
To adjust the volume of detergent used within the given
time setting, loosen the knurled knob with an Allen
wrench on the control valve located in the by-pass
line. Refer to the Detergent System Outline. Turning
the knob clockwise increases the volume and counter
clockwise decreases the volume. When adjustment
has been made, be sure to retighten the setscrew.
5. Routine Maintenance
Washing Frequency
The frequency that the collected contaminant is
to be washed from the unit depends upon the type
and amount of contaminant in the air to be cleaned.
Contaminant which is greasy in nature tends to
harden after collection and should be washed away
often. Likewise, units operating under extremely
heavy contaminant loads should be washed more
often as a large build-up of collected material will have
a tendency to “blow-off” if permitted to remain on the
collecting elements for long periods of time. In that the
type and amount of contaminant varies geographically
(and from one location to another in any given area)
it is recommended to start operation with a washing
frequency of at least once a week. This schedule may
then be altered as needed after visual examinations
of the collected material contained on the ionizing-
collecting cells. Daily washing is not unusual for units
operating on heavy welding fume, kitchen exhaust
hoods or similar applications. Start time programming
is recommended to be within one hour of the end of
cooking time.
Detergent
Effective washing is dependent upon detergent. The
detergent reservoir should be examined on a routine
basis, a minimum tank level established, and never
permitted to empty. An empty tank not only means poor
washing, but can also be detrimental to the pump. The
inside of the tank should be kept clean, free from dirt and
foreign objects. The detergent, as supplied by TRION
®
,
is formulated specifically for electronic air cleaners. If
substitutes are used, they must be approved by TRION
®
,
so as to not void the warranty. They should be safe for
use in ventilation systems and non-caustic, as 95% of
the ionizing-collecting cells are constructed of aluminum,
special high voltage insulation and gasket seals.
Electrical Operation
The ESP section(s) access doors have LED indicating
lights to show status of the power supplies. Illumination
of LED(s) indicates proper operation. Flickering or dim
LED(s) indicate arcing within the ionizing-collecting
cell(s). No illumination indicates lack of input power,
dead short in ionizing-collecting cell(s), failed power
supply, and/or failed LED.
6. Periodic Maintenance
Water Wash System - Every 6 Months
The water wash spray pattern should be checked
on each nozzle to be sure that a full spray pattern is
developed. Distorted patterns are usually caused by
contaminant in the nozzle orifice, which can be cleaned
by inserting a small gage, soft copper wire into the
orifice. If any one manifold contains several nozzles
that are restricted, remove the manifold and thoroughly
flush. The main supply line strainer and the strainer in
the detergent system should be checked and cleaned.
Fire Suppression System (IF INSTALLED) - Every
6 Months
Properly trained and qualified personnel shall
complete inspection, cleaning and servicing of the fire
suppression system.
All actuation components, including remote manual pull
stations, mechanical or electrical devices, detectors,
fire-actuated dampers, etc., shall be checked for
proper operation in accordance with the manufacturers
listed procedures. In addition to these requirements,
the specific inspection requirements of the applicable
NFPA standard shall also be followed. If required,
certificates of inspection and maintenance shall be
forwarded to the authority having jurisdiction.
Control Panel - Every 12 Months
The inside of the controller cabinet should be
examined for accumulated dirt and dust. If required,
the components should be cleaned using a good brand
of electrical contact cleaner. All terminal connections
approved should be checked for securement and
tightened or reworked as required.